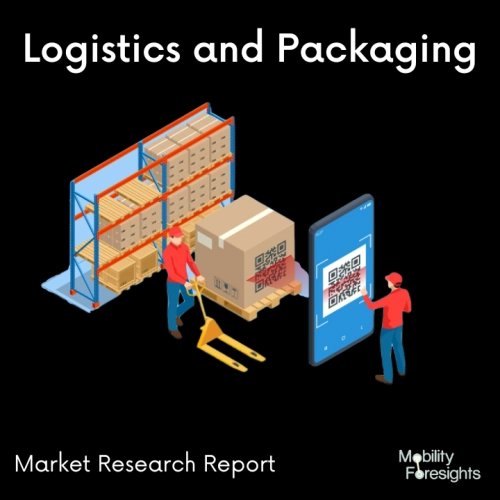
- Get in Touch with Us
Last Updated: Apr 25, 2025 | Study Period: 2023-2030
The famous carbonated soft drink bottle is a container option made especially for fizzy drinks. It serves as a practical and effective means of transporting, storing, and consuming carbonated beverages including soda, cola, energy drinks, and sparkling water, making it a crucial part of the beverage business.
To ensure that it can resist the pressure created by carbonation, the CSD Bottle is often built of sturdy materials like glass or plastic. It has a tight closing device, either a screw cap or a snap-on lid, that stops carbon dioxide from escaping and keeps the drink's carbonation level constant.
Usually built of tough materials like glass or plastic, the CSD Bottle is capable of withstanding the pressure brought on by carbonation. It has a tight closing device, either a screw cap or a snap-on lid, that keeps the drink's carbonation level constant and prevents carbon dioxide from escaping.
The CSD Bottle's capacity to maintain the freshness and fizz of carbonated beverages is one of its significant advantages. The bottle's shape reduces the amount of time that the contents are exposed to elements like light and air, which can degrade the beverage's flavour and quality.
It gives customers a pleasing fizz and a pleasurable drinking experience by maintaining the carbonation.CSD Bottles are available in a variety of sizes to accommodate diverse consumer preferences.
The Global Carbonated Soft Drink (CSD) Bottle market accounted for $XX Billion in 2022 and is anticipated to reach $XX Billion by 2030, registering a CAGR of XX% from 2023 to 2030.
Coca-Cola introduces its first prototype bottle built from plant-based materials in the market for carbonated soft drinks.Coca-Cola Unveils New Bottle Prototype Made Totally Of Plant-Based Materials.
The Coca-Cola Company today unveiled a next-generation prototype bottle, the first to be constructed entirely of plant-based plastic (bPET), with the exception of the cap and label, and built with methods that are now prepared to be scaled up commercially throughout the sector (1).
This builds on a technological advance that was revealed last week for the first anticipated commercialization of methods to produce plant-based monoethylene glycol (bMEG), one of the two molecules required to make bPET, using second-generation biomass.
1 | Market Segmentation |
2 | Scope of the report |
3 | Abbreviations |
4 | Research Methodology |
5 | Executive Summary |
6 | Introduction |
7 | Insights from Industry stakeholders |
8 | Cost breakdown of Product by sub-components and average profit margin |
9 | Disruptive innovation in the Industry |
10 | Technology trends in the Industry |
11 | Consumer trends in the industry |
12 | Recent Production Milestones |
13 | Component Manufacturing in US, EU and China |
14 | COVID-19 impact on overall market |
15 | COVID-19 impact on Production of components |
16 | COVID-19 impact on Point of sale |
17 | Market Segmentation, Dynamics and Forecast by Geography, 2023-2030 |
18 | Market Segmentation, Dynamics and Forecast by Product Type, 2023-2030 |
19 | Market Segmentation, Dynamics and Forecast by Application, 2023-2030 |
20 | Market Segmentation, Dynamics and Forecast by End use, 2023-2030 |
21 | Product installation rate by OEM, 2023 |
22 | Incline/Decline in Average B-2-B selling price in past 5 years |
23 | Competition from substitute products |
24 | Gross margin and average profitability of suppliers |
25 | New product development in past 12 months |
26 | M&A in past 12 months |
27 | Growth strategy of leading players |
28 | Market share of vendors, 2023 |
29 | Company Profiles |
30 | Unmet needs and opportunity for new suppliers |
31 | Conclusion |
32 | Appendix |