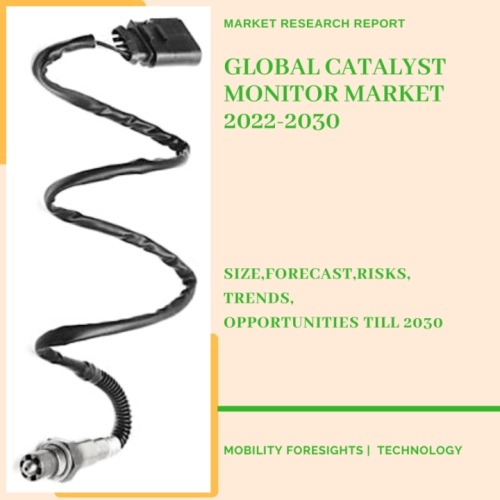
- Get in Touch with Us
Last Updated: Apr 25, 2025 | Study Period: 2022-2030
Internal mechanisms known as catalytic monitors evaluate the converter's ability to decrease dangerous pollutants.Other components of flue gas will be broken down by oxygen from the engine exhaust when the catalysts are working properly (or pollutants).
All of the oxygen that hits the converters will be in use under the normal closed-loop fuel management operating conditions.The catalytic converter monitor is a set of tests carried out by the car's computer (ECM) to ascertain whether the converter is operating normally. Sensors are necessary for all monitors, including the catalyst monitor. The O2 sensors are the important sensors in the catalyst monitor scenario.
The Global Catalyst Monitor market accounted for $XX Billion in 2021 and is anticipated to reach $XX Billion by 2030, registering a CAGR of XX% from 2022 to 2030.
The Dynalco Catalyst Monitor is made to comply with EPA regulations requiring close monitoring of pressure ratio and catalyst intake temperature on diesel and spark-ignited engines. It can log all parameters onto an internal flash memory and read up to six input channels at once. It can also calculate differential values, provide alarm and shutdown outputs, and provide outputs for alarm and shutdown.
Additionally included is an RS-485 Modbus link for communicating with a DCS or PLC. Additionally, the Catalyst Monitor can determine the engine catalyst input temperature using a 4-hour rolling average in accordance with the most recent EPA standards.
By using predictive analytics to monitor, anticipate, and reduce inpatient risk, Health Catalyst's new surveillance module for its Patient Safety Monitor suite intends to assist hospitals in safeguarding patient safety.
The maintenance of the catalytic converter's performance is required for emissions-related on-board components. The only tried-and-true method for monitoring hydrocarbon catalyst performance is the dual exhaust gas oxygen sensor approach. The dual oxygen sensor approach is based on the idea that a catalyst with a high oxygen storage capacity will perform better than one with a low OSC.
To establish a connection between changes in OSC and HC performance, a statistical relationship has been established. The current algorithm is susceptible to false illumination of the malfunction Indication Light (MIL) for a variety of reasons, including the precision with which the algorithm consistently predicts a malfunctioning and the precision with which the diagnostic algorithms can predict a catalyst malfunctioning condition.
The correlation between the EGO sensor signals and hydrocarbon emissions has been significantly improved by a new generation of algorithm.
The capacity of a metric to diagnose the catalyst's performance during transient operation is the most important test of any diagnosing algorithm. This is because OBD 2 requires the on-board diagnostic method to monitor the catalyst during each key on and to turn on if emissions fall during two key ons consecutively.
The OBD mandates that the catalyst's hydrocarbon performance be continuously monitored and connected to the vehicle's electronic control unit. To correlate a characteristic of the catalysis process with the HC emissions, a number of different approaches have been proposed.
The catalyst system's ability to accurately predict a catalyst malfunction condition and monitor the catalyst during any transient operation, regardless of the drive cycle, is the main feature of the diagnoistic algorithm presented here.
The demand for the product in petrochemicals and chemicals applications has increased as a result of manufacturers' efforts to produce value-added petrochemicals and chemicals like methanol and polyolefins in order to increase the value of their feedstock or refinery.
Demand for oil has decreased significantly for the first time in a decade as a result of the unprecedented COVID-19 outbreak, which has resulted in the closure of factories and manufacturing facilities.
Additionally, oil prices have significantly decreased as a result of the price war between Russia and KSA. Alkanes and naphthenes are produced when aromatics and olefins are broken down and rearranged by these metals at a faster rate.
Sl no | Topic |
1 | Market Segmentation |
2 | Scope of the report |
3 | Abbreviations |
4 | Research Methodology |
5 | Executive Summary |
6 | Introduction |
7 | Insights from Industry stakeholders |
8 | Cost breakdown of Product by sub-components and average profit margin |
9 | Disruptive innovation in the Industry |
10 | Technology trends in the Industry |
11 | Consumer trends in the industry |
12 | Recent Production Milestones |
13 | Component Manufacturing in US, EU and China |
14 | COVID-19 impact on overall market |
15 | COVID-19 impact on Production of components |
16 | COVID-19 impact on Point of sale |
17 | Market Segmentation, Dynamics and Forecast by Geography, 2022-2030 |
18 | Market Segmentation, Dynamics and Forecast by Product Type, 2022-2030 |
19 | Market Segmentation, Dynamics and Forecast by Application, 2022-2030 |
20 | Market Segmentation, Dynamics and Forecast by End use, 2022-2030 |
21 | Product installation rate by OEM, 2022 |
22 | Incline/Decline in Average B-2-B selling price in past 5 years |
23 | Competition from substitute products |
24 | Gross margin and average profitability of suppliers |
25 | New product development in past 12 months |
26 | M&A in past 12 months |
27 | Growth strategy of leading players |
28 | Market share of vendors, 2022 |
29 | Company Profiles |
30 | Unmet needs and opportunity for new suppliers |
31 | Conclusion |
32 | Appendix |