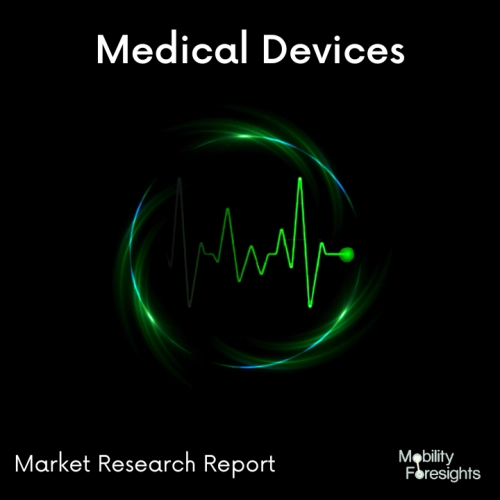
- Get in Touch with Us
Last Updated: Apr 25, 2025 | Study Period: 2024-2030
The method of producing the end of a thermoplastic tube using a thermally conductive mould is known as catheter tipping, sometimes known as end forming. There are various typical techniques for applying energy to the mould that is appropriate for making medical devices, including: processing with hot air. Electric heating.
Apparatus for tipping catheters For all of your catheter tipping needs, including catheter tip shaping, bonding, flares, and flanges,offers cutting-edge technology. The method of producing the end of a thermoplastic tube using a thermally conductive mould is known as catheter tipping, sometimes known as end forming.
It is necessary to heat a die to a specified temperature and then insert the shaft material to a specific depth in order to thermoform a catheter's distal tip into the required rounded or tapered shape.
Global catheter tipping equipment market accounted for $XX Billion in 2022 and is anticipated to reach $XX Billion by 2030, registering a CAGR of XX% from 2024 to 2030.
The automated tipping system (ATS), which ASG Medical Systems claims is the first completely automated gadget of its kind, was revealed at the expo last week. "The automation that ATS offers, such as the loading of catheters and the cutting and loading of the individual soft tips into the tipping process, have always been distinct, manual procedures.
More specifically, the ATS uses the Accu-Cut tube cutting and Accu-Feed tube feeding technologies from ASG and Sebra to deliver a fully automated catheter-tipping operation. The system's capabilities include precision length cutting, assembly, necking and flaring, singulation, thermal bonding of two catheter materials for soft-tip applications, and singulation.
According to the creators, the device makes exact lengths and clean, square cuts in addition to being user-friendly and simple. It does not require operator data entry and has a high-resolution touch screen interface.
Additionally, by reducing the time it takes to launch new products, reliably meeting customer delivery deadlines, and maintaining a leading position in medical packaging innovation, manufacturers can compete on their capacity to make a significant, long-lasting impact on the success of medical device companies.
The capacity to propel these advancements is increasingly built on a foundation of ongoing gains in precision manufacturing.
Sl no | Topic |
1 | Market Segmentation |
2 | Scope of the report |
3 | Abbreviations |
4 | Research Methodology |
5 | Executive Summary |
6 | Introduction |
7 | Insights from Industry stakeholders |
8 | Cost breakdown of Product by sub-components and average profit margin |
9 | Disruptive innovation in the Industry |
10 | Technology trends in the Industry |
11 | Consumer trends in the industry |
12 | Recent Production Milestones |
13 | Component Manufacturing in US, EU and China |
14 | COVID-19 impact on overall market |
15 | COVID-19 impact on Production of components |
16 | COVID-19 impact on Point of sale |
17 | Market Segmentation, Dynamics and Forecast by Geography, 2024-2030 |
18 | Market Segmentation, Dynamics and Forecast by Product Type, 2024-2030 |
19 | Market Segmentation, Dynamics and Forecast by Application, 2024-2030 |
20 | Market Segmentation, Dynamics and Forecast by End use, 2024-2030 |
21 | Product installation rate by OEM, 2023 |
22 | Incline/Decline in Average B-2-B selling price in past 5 years |
23 | Competition from substitute products |
24 | Gross margin and average profitability of suppliers |
25 | New product development in past 12 months |
26 | M&A in past 12 months |
27 | Growth strategy of leading players |
28 | Market share of vendors, 2023 |
29 | Company Profiles |
30 | Unmet needs and opportunity for new suppliers |
31 | Conclusion |
32 | Appendix |