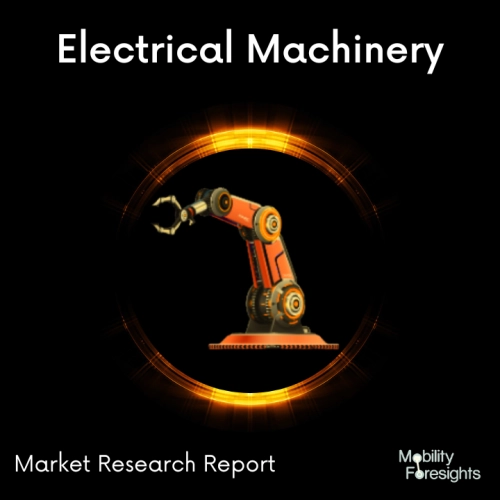
- Get in Touch with Us
Last Updated: Apr 25, 2025 | Study Period: 2024-2030
The centrifugal casting technique involves pouring molten metal into a quickly rotating cylindrical mold, where the centrifugal force from the rotation applies pressure to the molten metal, producing pipes.
A sound cast metal quality, devoid of cavities and inclusions, is achieved through directional solidification, beginning from the outside face in contact with the metal mold.
A hollow cylindrical product with constant wall thickness is the result of centrifugal force. Because there is nothing to disturb solidification shrinkage, residual tension after casting is minimized with the centrifugal casting technique.
The Global Centrifugal Casting Pipe market accounted for $XX Billion in 2023 and is anticipated to reach $XX Billion by 2030, registering a CAGR of XX% from 2024 to 2030.
The current invention relates to a centrifugal casting technique for producing cold drawn seamless pipes made of ultralow-carbon dual-phase stainless steel.
The productive technologies of the present invention are principally characterised in that a medium frequency melting furnace adopts a non-oxidizing method for smelting or a vacuum induction electric furnace for smelting to prevent carbon rising and control S, P indices.
Chemical compositions, especially the amounts of Cr, Ni, Mo, and N, are rigorously regulated to assure the ratio of A to F in the metallographic structures of the steel pipes.
In order to avoid cracking in cold drawing, a sigma phase is avoided by solution treatment and rapid cooling.The rate of cold drawn seamless steel pipes being produced at a higher rate, particularly large calibre and thick-walled steel pipes, is a result of improved production technologies.
This results in finished products that are more intense and suitable for use in environments with high levels of C1 ion, H2S, CO2, etc. Additional improvements are made to the pipes' mechanical and welding performance.
Next, perform rotary casting, using electronics to maintain control over each required amount of molten steel in the cast tube, and then adopt horizontal centrifugal casting in accordance with the specifications for centrifugally cast pipes, with a melting temperature of 1620â1640 °C, a pouring speed of 10-15 kg per second, and a rotating speed of 400â1600 rev/min;
Sl no | Topic |
1 | Market Segmentation |
2 | Scope of the report |
3 | Abbreviations |
4 | Research Methodology |
5 | Executive Summary |
6 | Introduction |
7 | Insights from Industry stakeholders |
8 | Cost breakdown of Product by sub-components and average profit margin |
9 | Disruptive innovation in the Industry |
10 | Technology trends in the Industry |
11 | Consumer trends in the industry |
12 | Recent Production Milestones |
13 | Component Manufacturing in US, EU and China |
14 | COVID-19 impact on overall market |
15 | COVID-19 impact on Production of components |
16 | COVID-19 impact on Point of sale |
17 | Market Segmentation, Dynamics and Forecast by Geography, 2024-2030 |
18 | Market Segmentation, Dynamics and Forecast by Product Type, 2024-2030 |
19 | Market Segmentation, Dynamics and Forecast by Application, 2024-2030 |
20 | Market Segmentation, Dynamics and Forecast by End use, 2024-2030 |
21 | Product installation rate by OEM, 2023 |
22 | Incline/Decline in Average B-2-B selling price in past 5 years |
23 | Competition from substitute products |
24 | Gross margin and average profitability of suppliers |
25 | New product development in past 12 months |
26 | M&A in past 12 months |
27 | Growth strategy of leading players |
28 | Market share of vendors, 2023 |
29 | Company Profiles |
30 | Unmet needs and opportunity for new suppliers |
31 | Conclusion |
32 | Appendix |