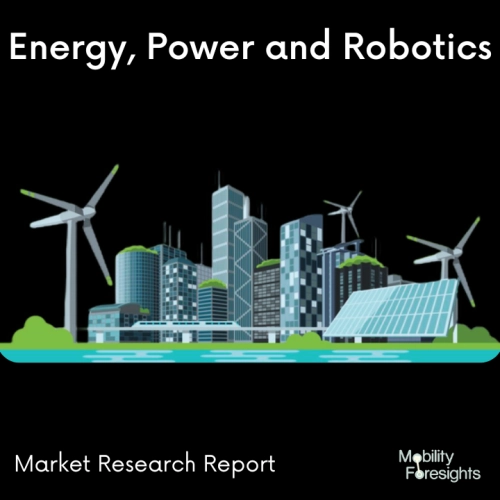
- Get in Touch with Us
Last Updated: Apr 25, 2025 | Study Period: 2023-2030
A battery separator that has a ceramic layer or coating added to it is referred to as a ceramic-coated battery separator. To enhance the battery's performance and safety features, a ceramic coating is often placed on the surface of the separator material, which is typically a polymeric film made of polyethylene (PE) or polypropylene (PP).
In battery applications, the ceramic coating has numerous functions.More improved thermal stability and better resilience to high temperatures are provided by the ceramic layer. This is crucial for operating high-power or high-temperature batteries because it helps prevent the separator from shrinking, melting, or deteriorating at high temperatures.
This improved thermal stability increases the battery's overall safety by reducing the possibility of thermal runaway.Increased puncture resistance: The battery separator's mechanical strength and puncture resistance can both be improved by the ceramic coating.
By lowering the possibility of heat events and enhancing the battery's general stability, it aids in preventing internal short circuits brought on by electrode penetration.Dendrite growth can be inhibited by ceramic coatings, which can function as a barrier to the development of metallic dendrites inside the battery.
On the electrodes, dendrites, which are minute metallic growths, may develop and perhaps result in short circuits. The ceramic layer aids in preventing or reducing dendrite formation, extending the battery's lifespan and cycle life.
Improved electrolyte wettability: The ceramic coating can be created with regulated porosity or surface properties that enhance the electrolyte's wetting behavior. Better ion transport and more effective use of the battery's active components are made possible as a result, leading to better performance and higher energy density.
Advanced battery technologies, including lithium-ion batteries, where safety, stability, and long cycle life are crucial, make heavy use of ceramic-coated battery separators. Depending on the battery chemistry and application requirements, a different ceramic material and coating procedure may be used.
Batteries can perform better overall, be safer, and last longer if they have a ceramic coating added to improve the thermal, mechanical, and electrochemical characteristics of the separator.
The Global Ceramic Coated Battery Separator Market accounted for $XX Billion in 2022 and is anticipated to reach $XX Billion by 2030, registering a CAGR of XX% from 2023 to 2030.
With great pleasure, Celgard announces that it and Morrow Batteries AS have signed a multi-year joint development agreement. In order to create, test, and market next-generation dry-process battery separators for use in high-voltage Morrow lithium nickel manganese oxide (LNMO) cathode battery cells for electric vehicle (EV) and energy storage system (ESS) applications, Celgard will collaborate with Morrow.
A subsidiary of Polypore International, LP (Polypore), Celgard, LLC (Celgard) is happy to announce that it has formed a strategic relationship with C4V, a leader in lithium-ion battery technology, to accelerate the creation of next-generation, high-performance, high-voltage battery cells.
In order to produce separator products for the lithium-ion battery industry that are most suited for C4V's high-voltage bio-mineralized lithium mixed metal phosphate (BM-LMP) cathode material, Celgard and C4V will work together.
Sl no | Topic |
1 | Market Segmentation |
2 | Scope of the report |
3 | Abbreviations |
4 | Research Methodology |
5 | Executive Summary |
6 | Introduction |
7 | Insights from Industry stakeholders |
8 | Cost breakdown of Product by sub-components and average profit margin |
9 | Disruptive innovation in the Industry |
10 | Technology trends in the Industry |
11 | Consumer trends in the industry |
12 | Recent Production Milestones |
13 | Component Manufacturing in US, EU and China |
14 | COVID-19 impact on overall market |
15 | COVID-19 impact on Production of components |
16 | COVID-19 impact on Point of sale |
17 | Market Segmentation, Dynamics and Forecast by Geography, 2023-2030 |
18 | Market Segmentation, Dynamics and Forecast by Product Type, 2023-2030 |
19 | Market Segmentation, Dynamics and Forecast by Application, 2023-2030 |
20 | Market Segmentation, Dynamics and Forecast by End use, 2023-2030 |
21 | Product installation rate by OEM, 2023 |
22 | Incline/Decline in Average B-2-B selling price in past 5 years |
23 | Competition from substitute products |
24 | Gross margin and average profitability of suppliers |
25 | New product development in past 12 months |
26 | M&A in past 12 months |
27 | Growth strategy of leading players |
28 | Market share of vendors, 2023 |
29 | Company Profiles |
30 | Unmet needs and opportunity for new suppliers |
31 | Conclusion |
32 | Appendix |