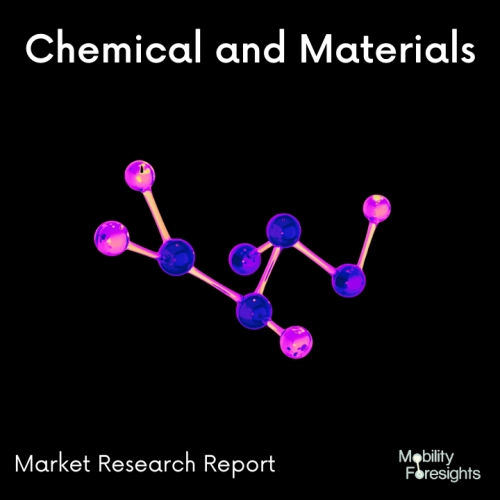
- Get in Touch with Us
Last Updated: Apr 25, 2025 | Study Period: 2024-2030
Ceramic nanowires are nanostructures that are composed of ceramic materials. They have a unique combination of properties, such as their size, strength, electrical conductivity, and excellent chemical stability.
These properties enable them to be used in a variety of applications ranging from electrical and thermal conductivity to sensing, drug delivery, and energy storage.
Ceramic nanowires are typically composed of oxides such as aluminum oxide, titanium oxide, and silicon oxide. They can also be composed of other ceramic materials such as boron nitride, zinc oxide, and yttrium oxide.
Due to their small size and shape, ceramic nanowires have a high surface area, which allows them to absorb more light and heat than traditional ceramic materials.
This makes them ideal for use in solar cells and other energy conversion technologies.Ceramic nanowires are also used in sensors, due to their ability to detect changes in their environment.
They can be used to measure pressure, temperature, pH, and other parameters. Furthermore, they can be used in drug delivery, due to their controlled release of drugs when exposed to certain conditions.
Ceramic nanowires can also be used in energy storage devices such as supercapacitors. They can store a large amount of energy due to their high surface area and ability to store both cations and anions.
This makes them ideal for use in devices such as electric cars, drones, and portable electronics.Overall, ceramic nanowires have a wide range of applications due to their unique combination of properties.
They are used in a variety of industries, from energy storage to drug delivery, due to their ability to absorb light and heat, detect changes in their environment, and store energy.
The Global Ceramic Nanowire market accounted for $XX Billion in 2023 and is anticipated to reach $XX Billion by 2030, registering a CAGR of XX% from 2024 to 2030.
Inconel 718 ceramic nanowire powder for AM was developed by MIT researchers. For usage in metal PBF AM techniques, a group of engineers led by MIT discovered a straightforward, low-cost method of fortifying Inconel 718 with ceramic nanowires. According to the team, many more materials could be improved by applying their basic method.
The development of more resilient materials for harsh settings is always critically needed. Future applications of this technique, in their opinion, should be rather promising for a variety of materials.
In order to achieve "the homogeneous decoration of nano-ceramics on the surfaces of Inconel particles," they grind commercial Inconel 718 powders with a tiny quantity of ceramic nanowires.
The powder that is produced is then used in laser powder bed fusion to make parts. Comparing parts manufactured with their novel powder to those made only of Inconel 718, the researchers discovered that parts made in this manner have far less porosity and cracks. And that results in parts that are not only much stronger but also have many other benefits.
For instance, they have far greater resilience to radiation and high-temperature loading and are more ductile, or flexible. Furthermore, because the procedure "works with existing 3D printing machines," it is not expensive in and of itself. Simply apply this powder for much improved performance.
The cooling rate of ultrathin metal alloy layers produced by 3D printing is far faster than that of bulk objects made by traditional melt-solidification methods, which could establish a whole new avenue for alloy creation.
Consequently, "this type of 3D printing doesn't seem to be subject to many of the chemical composition regulations that apply to bulk casting." With the inclusion of ceramics, they thus have a significantly larger composition space to investigate for the base metal.
It was rather thrilling to see these real-world outcomes for this composition, given it was one of the initial choices. There is still a lot of room for investigation. They will continue to investigate novel Inconel composite compositions in order to develop materials that can tolerate increasingly severe environments.
Sl no | Topic |
1 | Market Segmentation |
2 | Scope of the report |
3 | Abbreviations |
4 | Research Methodology |
5 | Executive Summary |
6 | Introduction |
7 | Insights from Industry stakeholders |
8 | Cost breakdown of Product by sub-components and average profit margin |
9 | Disruptive innovation in the Industry |
10 | Technology trends in the Industry |
11 | Consumer trends in the industry |
12 | Recent Production Milestones |
13 | Component Manufacturing in US, EU and China |
14 | COVID-19 impact on overall market |
15 | COVID-19 impact on Production of components |
16 | COVID-19 impact on Point of sale |
17 | Market Segmentation, Dynamics and Forecast by Geography, 2024-2030 |
18 | Market Segmentation, Dynamics and Forecast by Product Type, 2024-2030 |
19 | Market Segmentation, Dynamics and Forecast by Application, 2024-2030 |
20 | Market Segmentation, Dynamics and Forecast by End use, 2024-2030 |
21 | Product installation rate by OEM, 2023 |
22 | Incline/Decline in Average B-2-B selling price in past 5 years |
23 | Competition from substitute products |
24 | Gross margin and average profitability of suppliers |
25 | New product development in past 12 months |
26 | M&A in past 12 months |
27 | Growth strategy of leading players |
28 | Market share of vendors, 2023 |
29 | Company Profiles |
30 | Unmet needs and opportunity for new suppliers |
31 | Conclusion |
32 | Appendix |