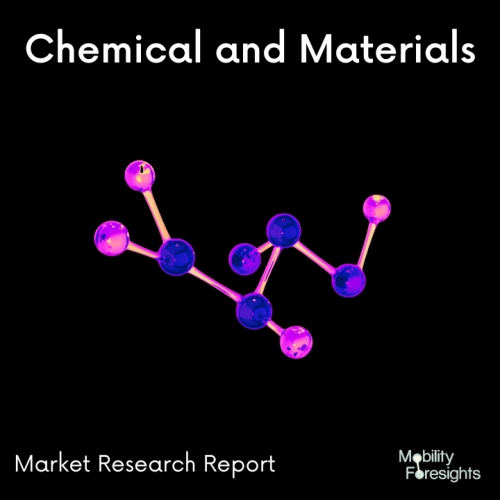
- Get in Touch with Us
Last Updated: Apr 25, 2025 | Study Period: 2024-2030
A "cermet" is made up of both metal and metal-oxide ceramic components. It is used as an intermediary Cermet coatings between the metallic bond coat and the ceramic top coat to manage the thermal expansion mismatch between the substrate and the functional coating.
Cermets were first intended for use in turbine applications like thick clearance control coatings and thermal barriers. A basic two-layer coating system can prematurely fail in many applications where this class of materials can be helpful due to intense temperature cycling.
Cutting tools: Cermet is a material that is frequently used to make milling cutters, saw blades, and drill bits. For cutting hard materials like metal, wood, and plastic, the material's great hardness and wear resistance make it the best choice.
Cermet is also employed as a coating substance to increase the wear resistance of a variety of surfaces, including engine parts, turbine blades, and industrial machinery.
The material is perfect for shielding vital components in severe environments because of its resilience to corrosion and erosionCermet's strong strength-to-weight ratio, tolerance to high temperatures, and corrosion resistance make it a popular material in the aerospace sector. It is employed in the production of heat shields, engine parts, and other crucial aerospace components.
The Global Cermet coatings market accounted for $XX Billion in 2023 and is anticipated to reach $XX Billion by 2030, registering a CAGR of XX% from 2024 to 2030.
Thermally-sprayed tungsten carbide (WC)-based cermet coatings have been widely used for a large variety of wear resistance applications. More recently, these coatings are being used as an alternative to hard chrome plating, especially in the aerospace and automotive industries.
Utilizing the automated spray systems and the commercial availability of spray grade powders with different compositions, the WC-based cermet coatings that are conventionally used for wear protection are now being extended for simultaneous corrosion protection.
Therefore, the corrosion behavior of various WC-based cermet coatings as a function of matrix composition, feedstock type and deposition technique exposed to a variety of corrosion mediums has been critically reviewed.
The corrosion mechanisms of WC-based cermet coatings studied using various analytical tools have also been comprehensively discussed. The interrelationship between the microstructural integrity and the corrosion behavior has been critically assessed. Further, the influence of pre- and post-treatments to improve the overall corrosion resistance of the coatings has also been highlighted.
Sl no | Topic |
1 | Market Segmentation |
2 | Scope of the report |
3 | Abbreviations |
4 | Research Methodology |
5 | Executive Summary |
6 | Introduction |
7 | Insights from Industry stakeholders |
8 | Cost breakdown of Product by sub-components and average profit margin |
9 | Disruptive innovation in the Industry |
10 | Technology trends in the Industry |
11 | Consumer trends in the industry |
12 | Recent Production Milestones |
13 | Component Manufacturing in US, EU and China |
14 | COVID-19 impact on overall market |
15 | COVID-19 impact on Production of components |
16 | COVID-19 impact on Point of sale |
17 | Market Segmentation, Dynamics and Forecast by Geography, 2024-2030 |
18 | Market Segmentation, Dynamics and Forecast by Product Type, 2024-2030 |
19 | Market Segmentation, Dynamics and Forecast by Application, 2024-2030 |
20 | Market Segmentation, Dynamics and Forecast by End use, 2024-2030 |
21 | Product installation rate by OEM, 2023 |
22 | Incline/Decline in Average B-2-B selling price in past 5 years |
23 | Competition from substitute products |
24 | Gross margin and average profitability of suppliers |
25 | New product development in past 12 months |
26 | M&A in past 12 months |
27 | Growth strategy of leading players |
28 | Market share of vendors, 2023 |
29 | Company Profiles |
30 | Unmet needs and opportunity for new suppliers |
31 | Conclusion |
32 | Appendix |