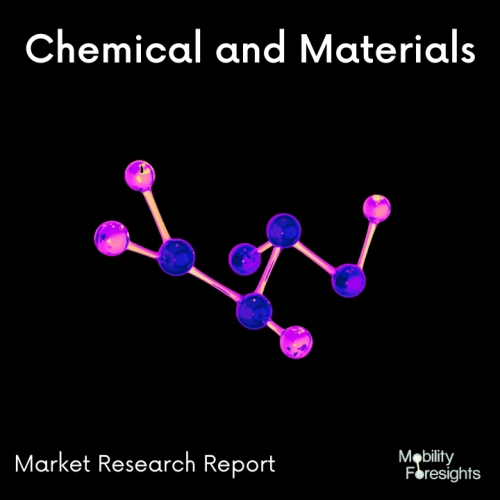
- Get in Touch with Us
Last Updated: Apr 25, 2025 | Study Period: 2024-2030
Chemically recycled bioplastics are a promising and innovative solution to address the environmental challenges posed by traditional plastics.These bioplastics are derived from renewable biomass sources, making them more sustainable than fossil fuel-based plastics.
However, what sets chemically recycled bioplastics apart is their ability to be recycled multiple times without losing their original properties and quality.
This characteristic opens up new horizons in the quest for a circular economy and a greener future.
Conventional plastics, derived from petroleum, have been a major environmental concern due to their non-biodegradable nature and the significant carbon footprint associated with their production.
In contrast, bioplastics are manufactured from renewable resources such as plant-based feedstocks (e.g., corn, sugarcane, and algae) or waste biomass from agricultural, forestry, and food industries.
The utilization of these renewable sources significantly reduces the reliance on finite fossil fuels and helps to mitigate greenhouse gas emissions.
However, while bioplastics offer a more sustainable alternative to conventional plastics, their potential impact is limited if they end up in landfills or as litter in the environment.
This is where the concept of chemical recycling comes into play.
Unlike traditional mechanical recycling, which involves melting and reshaping plastics, chemical recycling breaks down the polymer chains of bioplastics into their original monomers through various processes such as depolymerization or pyrolysis.
The recovered monomers from chemically recycled bioplastics can then be used to create new plastic products without any loss in quality.
This closed-loop approach enables a continuous recycling cycle, reducing the need for virgin materials and minimizing the environmental impact associated with plastic waste.
In conclusion, chemically recycled bioplastics hold immense potential in transforming the plastic industry and advancing towards a more sustainable future.
Derived from renewable biomass sources, these materials offer a greener alternative to traditional plastics.
Their ability to be recycled multiple times without compromising their original properties makes them a crucial component in achieving a circular economy.
By incorporating chemically recycled bioplastics into various applications, we can significantly reduce our dependence on fossil fuels, minimize plastic waste, and mitigate environmental impacts.
However, further research, investment, and collaboration are necessary to overcome existing challenges and fully unlock the benefits of this groundbreaking technology.
The Global Chemically Recycled Bioplastic Market accounted for $XX Billion in 2023 and is anticipated to reach $XX Billion by 2030, registering a CAGR of XX% from 2024 to 2030.
This is a new grade of Ingeo⢠Biopolymer that is made from 100% recycled content.
It is a high-performance material that is suitable for a wide range of applications, including packaging, foodservice, and consumer goods.
NatureWorks⢠Ingeo⢠Biopolymer 4021 is chemically recycled, which means that it can be recycled back into its original building blocks and then used to make new products.
This process is more energy-efficient than traditional recycling methods, and it produces a higher-quality product.
NatureWorks⢠Ingeo⢠Biopolymer 4021 is made from a variety of recycled materials, including corn starch, sugar, and vegetable oils.
These materials are first converted into a monomer, which is then polymerized to form the final product.
The chemical recycling process breaks down the polymer into its original monomers, which can then be used to make new products.
This is a chemically recycled biopolymer that is made from recycled PET and polylactic acid (PLA).
It is a versatile material that can be used for a variety of applications, including packaging, foodservice, and consumer goods.
BASF Ecovio⢠Recyclate is a sustainable choice for businesses that are looking to reduce their environmental impact.
BASF Ecovio⢠Recyclate is made by breaking down recycled PET and PLA into their original monomers.
These monomers are then polymerized to form the final product.
The chemical recycling process uses less energy and produces fewer emissions than traditional recycling methods.
Sl no | Topic |
1 | Market Segmentation |
2 | Scope of the report |
3 | Abbreviations |
4 | Research Methodology |
5 | Executive Summary |
6 | Introduction |
7 | Insights from Industry stakeholders |
8 | Cost breakdown of Product by sub-components and average profit margin |
9 | Disruptive innovation in the Industry |
10 | Technology trends in the Industry |
11 | Consumer trends in the industry |
12 | Recent Production Milestones |
13 | Component Manufacturing in US, EU and China |
14 | COVID-19 impact on overall market |
15 | COVID-19 impact on Production of components |
16 | COVID-19 impact on Point of sale |
17 | Market Segmentation, Dynamics and Forecast by Geography, 2024-2030 |
18 | Market Segmentation, Dynamics and Forecast by Product Type, 2024-2030 |
19 | Market Segmentation, Dynamics and Forecast by Application, 2024-2030 |
20 | Market Segmentation, Dynamics and Forecast by End use, 2024-2030 |
21 | Product installation rate by OEM, 2023 |
22 | Incline/Decline in Average B-2-B selling price in past 5 years |
23 | Competition from substitute products |
24 | Gross margin and average profitability of suppliers |
25 | New product development in past 12 months |
26 | M&A in past 12 months |
27 | Growth strategy of leading players |
28 | Market share of vendors, 2023 |
29 | Company Profiles |
30 | Unmet needs and opportunity for new suppliers |
31 | Conclusion |
32 | Appendix |