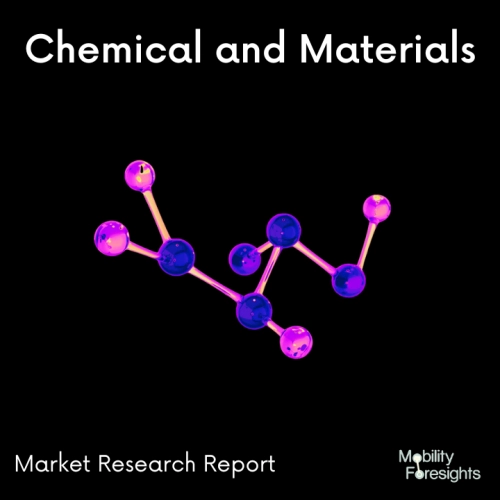
- Get in Touch with Us
Last Updated: Apr 25, 2025 | Study Period: 2024-2030
A form of glass known as chemically strengthened glass has improved strength as a result of a chemical procedure that occurs after manufacture. Similar to float glass, it nevertheless breaks into long, pointed splinters when it is broken. Because of this, it is not regarded as a safety glass and needs to be laminated if one is needed. Yet chemically enhanced glass typically has a strength of six to eight times that of float glass.
Gorilla glass is the most popular brand name for this type of glass. A surface polishing procedure gives the glass a chemical boost. At a temperature of roughly 300 °C, glass is immersed in a bath of molten potassium salt. As a result, potassium ions from the bath replace sodium ions on the glass surface.
Due to their larger size compared to sodium ions, these potassium ions move into the spaces left by the smaller sodium ions as they migrate to the molten potassium nitrate. The glass surface is compressed and the core is under compensating strain as a result of the replacement of ions. Glass that has been chemically reinforced can have a surface compression of up to 690 megapascals.
The strengthening process is based on the fact that glass has a substantially higher compressive strength than tensile strength. It takes some bending before one of the glass's surfaces can even enter tension because both of its surfaces are already compressed.
To obtain the tensile strength, more bending is necessary.Simply put, the compressive tension on the opposite surface increases. But because the compressive strength is so much higher, there is no compressive failure.
The Global Chemically Strengthened Glass Market accounted for $XX Billion in 2022 and is anticipated to reach $XX Billion by 2030, registering a CAGR of XX% from 2023 to 2030.
SATINAL, a global provider of cutting-edge technologies for the production of safety glass, introduces chemically Strengthened glass for the maritime industry. Glass is chemically tempered by submerging it in a bath of molten potassium nitrate salts that is heated to temperatures above 400°C.
As a result of the potassium ions in the salt replacing the sodium ions inside the glass, compression stresses are created throughout the entire surface and over the edges. When subjected to the same stress, chemically tempered glass has mechanical qualities that are up to six times more resistant to bending than thermally tempered glass. The surface compression used in this particular production technique boosts impact and scratch resistance.
Sl no | Topic |
1 | Market Segmentation |
2 | Scope of the report |
3 | Abbreviations |
4 | Research Methodology |
5 | Executive Summary |
6 | Introduction |
7 | Insights from Industry stakeholders |
8 | Cost breakdown of Product by sub-components and average profit margin |
9 | Disruptive innovation in the Industry |
10 | Technology trends in the Industry |
11 | Consumer trends in the industry |
12 | Recent Production Milestones |
13 | Component Manufacturing in US, EU and China |
14 | COVID-19 impact on overall market |
15 | COVID-19 impact on Production of components |
16 | COVID-19 impact on Point of sale |
17 | Market Segmentation, Dynamics and Forecast by Geography, 2024-2030 |
18 | Market Segmentation, Dynamics and Forecast by Product Type, 2024-2030 |
19 | Market Segmentation, Dynamics and Forecast by Application, 2024-2030 |
20 | Market Segmentation, Dynamics and Forecast by End use, 2024-2030 |
21 | Product installation rate by OEM, 2023 |
22 | Incline/Decline in Average B-2-B selling price in past 5 years |
23 | Competition from substitute products |
24 | Gross margin and average profitability of suppliers |
25 | New product development in past 12 months |
26 | M&A in past 12 months |
27 | Growth strategy of leading players |
28 | Market share of vendors, 2023 |
29 | Company Profiles |
30 | Unmet needs and opportunity for new suppliers |
31 | Conclusion |
32 | Appendix |