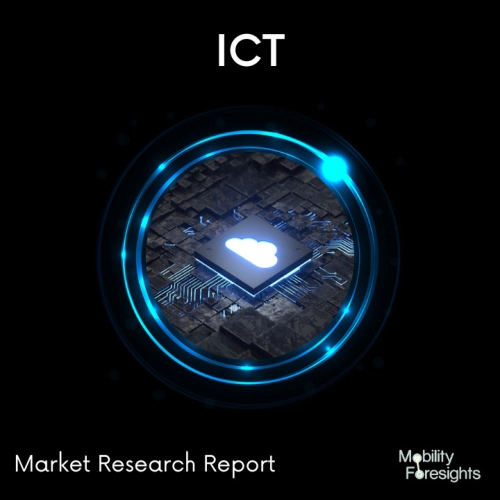
- Get in Touch with Us
Last Updated: Apr 25, 2025 | Study Period: 2022-2030
Sensors and actuators were coupled to the inputs and outputs of programmable logic controllers (PLCs), which were then connected to human-machine interfaces in traditional industrial automation systems (HMIs). This led to excellent performance and acceptable security, at least locally.
However, establishing a connection to these local resources from a distance, getting to the data, and processing it needed a lot of time-consuming computational and networking resources.There are more recent cloud -based PLCs that can link directly to cloud services and eliminate this pain point without the need for intermediary processing .
It seems like a brilliant idea to connect industrial automation sources to the cloud, and many consumer and business apps already do it successfully. However, operational firms are worried about protecting their data from being misused, and they need to protect.
The Global cloud-based PLCs market accounted for $XX Billion in 2021 and is anticipated to reach $XX Billion by 2030, registering a CAGR of XX% from 2022 to 2030.
For effective and simple remote monitoring and control of operational state of facilities such as on/off status, pressure, and temperature, the RDL Cloud-based PLC 4.0 series specifies a new method of converting factories into smart/intelligent factories.
Wide variety of industrial protocols are supported by RDL Cloud-based PLC 4.0.Modbus, MQTT, JSON, RESTful, TCP/UDP, and SNMP protocol are just a few examples of open source APIs that make it simpler than ever for IT engineers to monitor and integrate solutions.
With the help of RDL Cloud-based PLC 4.0, a custom industrial monitoring and control system for PLC, SCADA, HMI, VFD, motors, servos, valves, and energy metres may be built.industrial sensors, RFID and fingerprint readers, actuators, relays, encoders, and many more with the operational advantages listed below.
logging network is made simpler because RDL Data Logger includes a variety of functions.Production environment without paper, production figures, and rejections.availability of the equipment and downtime.Performance forecasting for preventive maintenance enables IT management.
Sl no | Topic |
1 | Market Segmentation |
2 | Scope of the report |
3 | Abbreviations |
4 | Research Methodology |
5 | Executive Summary |
6 | Introduction |
7 | Insights from Industry stakeholders |
8 | Cost breakdown of Product by sub-components and average profit margin |
9 | Disruptive innovation in the Industry |
10 | Technology trends in the Industry |
11 | Consumer trends in the industry |
12 | Recent Production Milestones |
13 | Component Manufacturing in US, EU and China |
14 | COVID-19 impact on overall market |
15 | COVID-19 impact on Production of components |
16 | COVID-19 impact on Point of sale |
17 | Market Segmentation, Dynamics and Forecast by Geography, 2022-2030 |
18 | Market Segmentation, Dynamics and Forecast by Product Type, 2022-2030 |
19 | Market Segmentation, Dynamics and Forecast by Application, 2022-2030 |
20 | Market Segmentation, Dynamics and Forecast by End use, 2022-2030 |
21 | Product installation rate by OEM, 2022 |
22 | Incline/Decline in Average B-2-B selling price in past 5 years |
23 | Competition from substitute products |
24 | Gross margin and average profitability of suppliers |
25 | New product development in past 12 months |
26 | M&A in past 12 months |
27 | Growth strategy of leading players |
28 | Market share of vendors, 2022 |
29 | Company Profiles |
30 | Unmet needs and opportunity for new suppliers |
31 | Conclusion |
32 | Appendix |