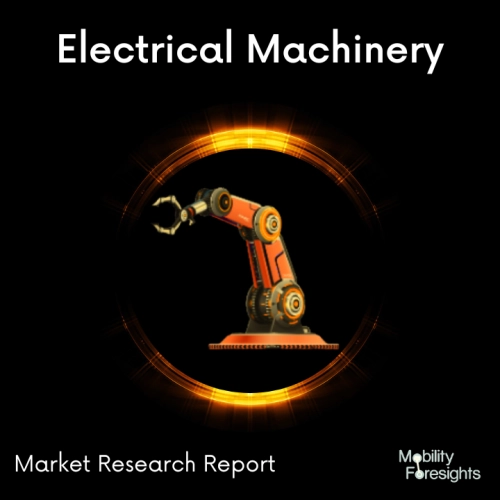
- Get in Touch with Us
Last Updated: Apr 25, 2025 | Study Period: 2024-2030
Multi-tasking Turning Several cutting tools can be used in the cut independently or concurrently using multi-spindle and multi-turret configurations on multitasking turning centres, which are available for both tiny, high-production parts and large, heavy-duty applications.
Multi-tasking Turning machining is a type of manufacturing that uses tools that can move in at least four different directions to mill away extra material, water jet cut, or laser cut items out of metal or other materials. Initially, mechanically operated, massive, sophisticated machines were used to carry out this type of machining.
These machines used 4, 5, 6, and even 12 axes, each of which was individually controlled by a lever resting on a cam plate. The tooling device, the table where the part is fastened, and other variables could be controlled by the cam plates. in addition to rotating any tools or components inside the machine. Setting up the machines for production took a long time because of their size and complexity.
As computer numerically controlled machining was developed, complicated items could be machined more quickly and effectively. Standard CNC tools can translate in three axes,Multi-tasking Turning and machines can also rotate around one or more axes. Industry frequently employs 5-axis machines where the workpiece is linearly translated along three axes and the tooling spindle is capable of rotating about two additional axes.
The Global CNC Multi-tasking Turning Center market accounted for $XX Billion in 2023 and is anticipated to reach $XX Billion by 2030, registering a CAGR of XX% from 2024 to 2030.
launchingthe "SC-200II," a brand-new precision CNC multifunctional lathe from Nakamura-Tome Precision Industries Co., Ltd. The new machine has grown from the traditional SC-200 machine in all ways with the idea of "Next level machining.
" The Qualities are A single-turret multitasking lathe with high rigidity that can handle powerful and stable machining is called the SC-200 II. Although being an 8" class machine, it has a maximum turning diameter of 390mm and a diameter for the swing over cover of 700mm, ensuring a sizable machining area.
It permits a 10" chuck to be installed on the machine. The spindle motor's output has increased to 15/11kW Op. 18.5/15kW, outperforming the previous generation. The ability to attain a one-rank greater machining capacity is made possible by improvements to the spindle motor power, bar capacity, and Y-axis side travel.
Sl no | Topic |
1 | Market Segmentation |
2 | Scope of the report |
3 | Abbreviations |
4 | Research Methodology |
5 | Executive Summary |
6 | Introduction |
7 | Insights from Industry stakeholders |
8 | Cost breakdown of Product by sub-components and average profit margin |
9 | Disruptive innovation in the Industry |
10 | Technology trends in the Industry |
11 | Consumer trends in the industry |
12 | Recent Production Milestones |
13 | Component Manufacturing in US, EU and China |
14 | COVID-19 impact on overall market |
15 | COVID-19 impact on Production of components |
16 | COVID-19 impact on Point of sale |
17 | Market Segmentation, Dynamics and Forecast by Geography, 2024-2030 |
18 | Market Segmentation, Dynamics and Forecast by Product Type, 2024-2030 |
19 | Market Segmentation, Dynamics and Forecast by Application, 2024-2030 |
20 | Market Segmentation, Dynamics and Forecast by End use, 2024-2030 |
21 | Product installation rate by OEM, 2023 |
22 | Incline/Decline in Average B-2-B selling price in past 5 years |
23 | Competition from substitute products |
24 | Gross margin and average profitability of suppliers |
25 | New product development in past 12 months |
26 | M&A in past 12 months |
27 | Growth strategy of leading players |
28 | Market share of vendors, 2023 |
29 | Company Profiles |
30 | Unmet needs and opportunity for new suppliers |
31 | Conclusion |
32 | Appendix |