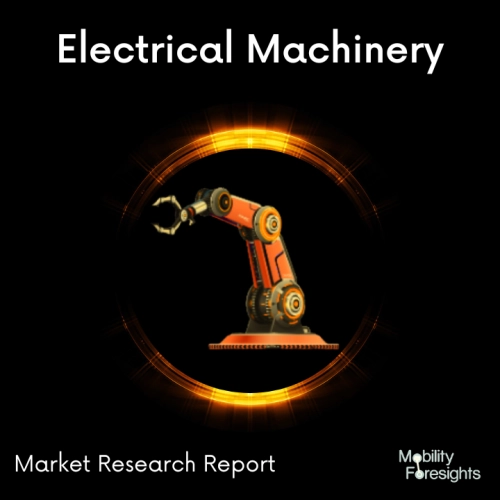
- Get in Touch with Us
Last Updated: Apr 25, 2025 | Study Period: 2024-2030
In the orbital welding process, CNC orbital welding machines use a static workpiece that is rotated 360 degrees (or 180 degrees in double up welding).
A homogeneous weld around pipes and tubes, which can be challenging to achieve with manual welding procedures, is made possible by this technology, which was initially designed to address the issue of operator error in Tungsten Inert Gas (TIG) welding (also known as Gas Tungsten Arc Welding, or GTAW).
With the use of a computer and the orbital welding technique, high-quality repeatable welds may be produced with little interference from a welding operator. Tube-to-tube and pipe-to-pipe joining as well as tube-to-tubesheet connecting are the two main applications for the method.
Over other welding methods, orbital welding has a number of benefits, such as: Productivity Gains: Because orbital welding equipment is automated, it is more productive than hand TIG welding because weld sequences can be reliably and quickly repeated.
Consistent Weld Quality: The weld cycle can be repeated with a high degree of accuracy and consistency once the weld parameters have been specified and entered.
The majority of orbital welding equipment enables real-time monitoring, allowing for the creation and storage of full weld protocols. Levels of Operator Skill: After receiving the necessary training, qualified mechanics can use orbital welding equipment.
Since the required skill levels are lower than those for manual welding, personnel expenses ought to be cheaper as well. Environment: Even in adverse conditions, orbital welding can be done.
The Global CNC orbital welding machine market accounted for $XX Billion in 2023 and is anticipated to reach $XX Billion by 2030, registering a CAGR of XX% from 2024 to 2030.
Compact power supplies for mechanized CNC orbital welding machines with a plethora of other unique technological features and a currently unique operating approach. The customer is provided with an incredibly cutting-edge and cost-effective welding system in conjunction with an ORBITALUM orbital weld head.
All ORBIMAT CA models include a FLO W FORCE function to shorten the pre-flow gas time when the weld heads are closed in the standard model and a BUP control function with controllable, position-dependent tube internal pressure control as an optional extra.
These functions are in addition to the dependable automatic programming, which generates welding parameters by entering the tube diameter, wall thickness, material, and welding gas.
Sl no | Topic |
1 | Market Segmentation |
2 | Scope of the report |
3 | Abbreviations |
4 | Research Methodology |
5 | Executive Summary |
6 | Introduction |
7 | Insights from Industry stakeholders |
8 | Cost breakdown of Product by sub-components and average profit margin |
9 | Disruptive innovation in the Industry |
10 | Technology trends in the Industry |
11 | Consumer trends in the industry |
12 | Recent Production Milestones |
13 | Component Manufacturing in US, EU and China |
14 | COVID-19 impact on overall market |
15 | COVID-19 impact on Production of components |
16 | COVID-19 impact on Point of sale |
17 | Market Segmentation, Dynamics and Forecast by Geography, 2024-2030 |
18 | Market Segmentation, Dynamics and Forecast by Product Type, 2024-2030 |
19 | Market Segmentation, Dynamics and Forecast by Application, 2024-2030 |
20 | Market Segmentation, Dynamics and Forecast by End use, 2024-2030 |
21 | Product installation rate by OEM, 2023 |
22 | Incline/Decline in Average B-2-B selling price in past 5 years |
23 | Competition from substitute products |
24 | Gross margin and average profitability of suppliers |
25 | New product development in past 12 months |
26 | M&A in past 12 months |
27 | Growth strategy of leading players |
28 | Market share of vendors, 2023 |
29 | Company Profiles |
30 | Unmet needs and opportunity for new suppliers |
31 | Conclusion |
32 | Appendix |