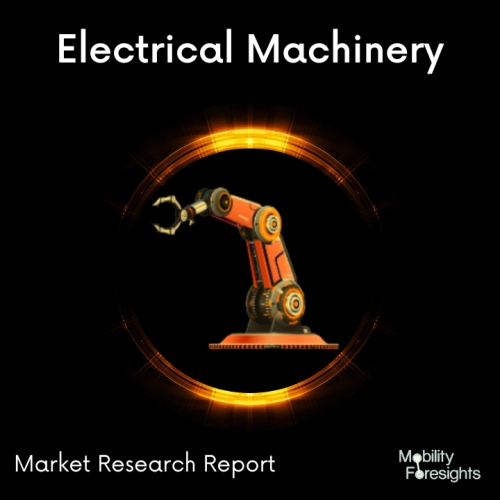
- Get in Touch with Us
Last Updated: Apr 25, 2025 | Study Period: 2023-2030
Casting has been practised for more than 6,000 years and is still commonly used. In this procedure, molten metal is poured into a mould. Similar to CNC machining, a more recent and widely used production technique, advancements in casting technology enable the casting of high quality products with precise tolerances.
Two sides of the sand mould will be constructed, and a pattern must be manufactured to generate each half. The geometry is represented by one half in each of the two designs. (positive shape). This "parting surface" at both patterns must be an exact match in order for the two mould halves to fit when there is no geometry.
The Global CNC sand casting machine market accounted for $XX Billion in 2022 and is anticipated to reach $XX Billion by 2030, registering a CAGR of XX% from 2023 to 2030.
Development and engineering quality ITAR-registered permanent mould tooling and sand-casting tooling for both low- and high-volume casting manufacturing are their specialties at Pentz Cast Solutions.
In order to provide CNC machined sand casting tools and CAD developed part models that meet specific needs, they work closely with customers to develop them from scratch.
They are able to create sand casting tooling for any equipment thanks to the internal CNC machine capabilities and wide range of casting tooling mediums and materials.
To ensure that the casting tooling is of the highest quality and meets the specifications of the application in question, new casting tooling is immediately inspected.
Large prototyping and production castings can have elaborate, complex geometries thanks to highly developed hybrid systems for casting tooling.
For its automated sand cast aluminium production and customer foundries, Pentz designs and fabricates precision CNC machined sand casting tooling for the pouring of grey iron, ductile iron, and bronze alloys.
Depending on a number of variables, including geometry, size, and quantity, coring may be carried out using aluminium shell core box equipment, dry sand core boxes, or 3D printed sand cores.
For automated high production runs, core boxes are made of CNC-machined aluminium or iron. They can develop new casting tooling with their internal resources and casting tooling know-how for just about any purpose.
Sl no | Topic |
1 | Market Segmentation |
2 | Scope of the report |
3 | Abbreviations |
4 | Research Methodology |
5 | Executive Summary |
6 | Introduction |
7 | Insights from Industry stakeholders |
8 | Cost breakdown of Product by sub-components and average profit margin |
9 | Disruptive innovation in the Industry |
10 | Technology trends in the Industry |
11 | Consumer trends in the industry |
12 | Recent Production Milestones |
13 | Component Manufacturing in US, EU and China |
14 | COVID-19 impact on overall market |
15 | COVID-19 impact on Production of components |
16 | COVID-19 impact on Point of sale |
17 | Market Segmentation, Dynamics and Forecast by Geography, 2023-2030 |
18 | Market Segmentation, Dynamics and Forecast by Product Type, 2023-2030 |
19 | Market Segmentation, Dynamics and Forecast by Application, 2023-2030 |
20 | Market Segmentation, Dynamics and Forecast by End use, 2023-2030 |
21 | Product installation rate by OEM, 2023 |
22 | Incline/Decline in Average B-2-B selling price in past 5 years |
23 | Competition from substitute products |
24 | Gross margin and average profitability of suppliers |
25 | New product development in past 12 months |
26 | M&A in past 12 months |
27 | Growth strategy of leading players |
28 | Market share of vendors, 2023 |
29 | Company Profiles |
30 | Unmet needs and opportunity for new suppliers |
31 | Conclusion |
32 | Appendix |