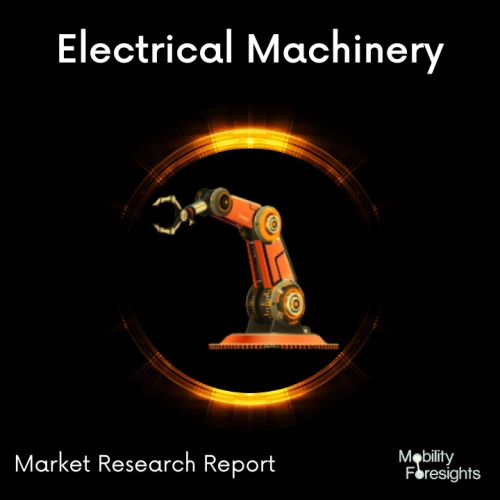
- Get in Touch with Us
Last Updated: Apr 25, 2025 | Study Period: 2024-2030
Single-flank testing, mating gears roll together at their proper centre distance with backlash and with only one flank in contact. Testing gears in this manner more closely simulates operation of the gears in their application than any other means of evaluation.
Gears can be tested by pairs, or with master gears. Rolling tests are functional tests where the quality grade of a gear unit is determined by rolling it against a higher quality (precision) master gear. They are also used to check complete transmissions and even to match gears in their optimal position.
The left and right flanks of the gear are tested independently, the mounting distance is fixed during measurement, both spindles are fitted with highly accurate rotary encoders, and the transmission error is measured.
Global CNC single flank gear rolling tester market accounted for $XX Billion in 2023 and is anticipated to reach $XX Billion by 2030, registering a CAGR of XX% from 2024 to 2030.
For five roll testing techniques, Klingelnberg offers high-precision testing technology. The technical firm Klingelnberg's most recent machine creation in the field of cylindrical gear technology is the Höfler cylindrical gear roll testing machine R 300.
The numerous quality control criteria for gears can only be addressed with a versatile test apparatus. The R 300 offers the option of applying all five roll testing techniques, depending on configuration. These include the helix roll test, the single flank test, the structure-borne noise test, the torsional acceleration test, and the double flank test.
In order to produce cylindrical gears, the R 300 may be utilised at every stage of the process chain, from monitoring the soft cutting to verifying distortions during hardening to assessing the noise characteristics of the installation-ready gear.
Sl no | Topic |
1 | Market Segmentation |
2 | Scope of the report |
3 | Abbreviations |
4 | Research Methodology |
5 | Executive Summary |
6 | Introduction |
7 | Insights from Industry stakeholders |
8 | Cost breakdown of Product by sub-components and average profit margin |
9 | Disruptive innovation in the Industry |
10 | Technology trends in the Industry |
11 | Consumer trends in the industry |
12 | Recent Production Milestones |
13 | Component Manufacturing in US, EU and China |
14 | COVID-19 impact on overall market |
15 | COVID-19 impact on Production of components |
16 | COVID-19 impact on Point of sale |
17 | Market Segmentation, Dynamics and Forecast by Geography, 2024-2030 |
18 | Market Segmentation, Dynamics and Forecast by Product Type, 2024-2030 |
19 | Market Segmentation, Dynamics and Forecast by Application, 2024-2030 |
20 | Market Segmentation, Dynamics and Forecast by End use, 2024-2030 |
21 | Product installation rate by OEM, 2023 |
22 | Incline/Decline in Average B-2-B selling price in past 5 years |
23 | Competition from substitute products |
24 | Gross margin and average profitability of suppliers |
25 | New product development in past 12 months |
26 | M&A in past 12 months |
27 | Growth strategy of leading players |
28 | Market share of vendors, 2023 |
29 | Company Profiles |
30 | Unmet needs and opportunity for new suppliers |
31 | Conclusion |
32 | Appendix |