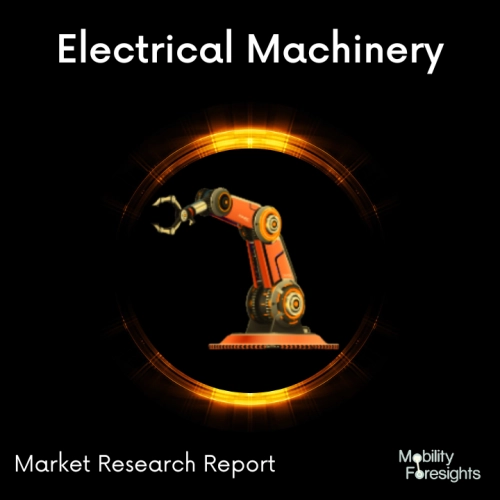
- Get in Touch with Us
Last Updated: Apr 25, 2025 | Study Period: 2024-2030
Spline rolling, also known as spline rollers, is a high-yield, low-cost cold forming technique that can be used to create a variety of shapes, including splines, threads, helixes, snap rings, and more. In the spline rolling process, two opposing forming racks move over a cylindrical object while exerting extremely strong forces.
Rolling equipment's main function is to compress raw materials into a thinner, more uniform shape that is necessary for making sheet metal. The raw material is compressed as it is fed through them using at least one set of rollers. The metal has a thinner, more standardized shape when it exits the rollers.
The Global CNC spline rolling machine market accounted for $XX Billion in 2023 and is anticipated to reach $XX Billion by 2030, registering a CAGR of XX% from 2024 to 2030.
In the area of spline rolling, Profadol's ROLEX is more than just an invention. Splines can be rolled onto a wide variety of shaft types using this adaptable machine type. Splines can be manufactured to the highest quality standards thanks to the CNC control and symmetric circular dies.
Because of its dependable Profile Rolling technique, the ROLEX is also able to cold-formed profiles, threads, and perform finishing rolling.
specialized driving chain for controlled workpiece acceleration during spline rolling 2-Rolling Multi Axis CNC Slides Graphical user interface Visualization of the process handling of data machine size recommendations for different applications version with servo mechanical drives in HP (High Precision)
The workpieces must be clamped between centers and positioned inside the work area. As the circular dies on the slides pierce the workpiece and cold form the desired spline profile, the rolling slide infeed begins. The workpiece is retracted from the work area once all profiles have been formed so that the operator can replace it.
Lowest changeover times are a result of circular dies for kinematic rolling with symmetric geometry, which correlates to a rolling rack of indefinite length and a workpiece-specific calibration phase that achieves the least tolerances. Up to five sets of dies can be mounted in one tooling setup.
Sl no | Topic |
1 | Market Segmentation |
2 | Scope of the report |
3 | Abbreviations |
4 | Research Methodology |
5 | Executive Summary |
6 | Introdauction |
7 | Insights from Industry stakeholders |
8 | Cost breakdown of Product by sub-components and average profit margin |
9 | Disruptive innovation in theIndustry |
10 | Technology trends in the Industry |
11 | Consumer trends in the industry |
12 | Recent Production Milestones |
13 | Component Manufacturing in US, EU and China |
14 | COVID-19 impact on overall market |
15 | COVID-19 impact on Production of components |
16 | COVID-19 impact on Point of sale |
17 | Market Segmentation, Dynamics and Forecast by Geography, 2024-2030 |
18 | Market Segmentation, Dynamics and Forecast by Product Type, 2024-2030 |
19 | Market Segmentation, Dynamics and Forecast by Application, 2024-2030 |
20 | Market Segmentation, Dynamics and Forecast by End use, 2024-2030 |
21 | Product installation rate by OEM, 2023 |
22 | Incline/Decline in Average B-2-B selling price in past 5 years |
23 | Competition from substitute products |
24 | Gross margin and average profitability of suppliers |
25 | New product development in past 12 months |
26 | M&A in past 12 months |
27 | Growth strategy of leading players |
28 | Market share of vendors, 2023 |
29 | Company Profiles |
30 | Unmet needs and opportunity for new suppliers |
31 | Conclusion |
32 | Appendix |