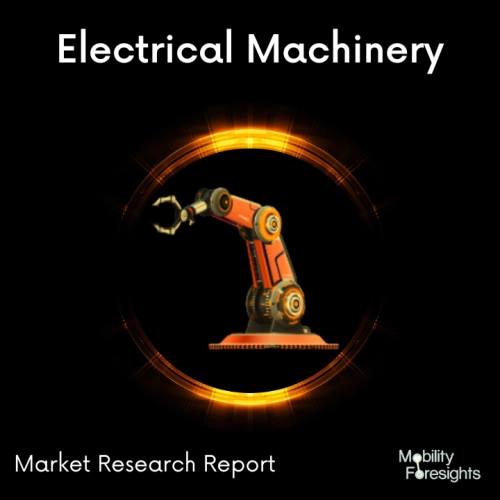
- Get in Touch with Us
Last Updated: Apr 25, 2025 | Study Period: 2024-2030
The table that the CNC surfboard shaping machine normally has several cutting tools fixed to it serves as its main component. These tools can be modified to carve the foam into various shapes, depending on the desired effect. They revolve quickly thanks to an electric motor that powers them.
The shaper may oversee the robot's performance and manage the cutting tools with computer controls as they sculpt the foam into the desired shape.
The machine may employ several separate saws to produce different elements of the surfboard, including the rails, the contour, and the rocker (the curve of the board from nose to tail). (the edges of the board).
The Global CNC Surfboard Shaping Machine market accounted for $XX Billion in 2023 and is anticipated to reach $XX Billion by 2030, registering a CAGR of XX% from 2024 to 2030.
The AkuShaper is the only CNC machine developed specifically for shaping surfboards with high-quality components built in-house; there is no outsourcing or piecemeal assembly.
Every step of the design and construction process is intended to create a surfboard shaping machine that is durable, simple to maintain, and reduces human mistakes.
The end result is a pedigree that no other system on the market can match. With more than 100 computers in use worldwide, it undergoes battle testing every day.
The most efficient method for cutting boards is the one developed by AkuShaper. The cutter, invented by AkuShaper, enables it to reach 140 around the blank, cutting flawless rails.
Unlike any other CNC system, our cutter reverses direction to produce a flawlessly symmetrical cut.Additionally, this method reduces the risk of board burn and improves cutting precision. We don't leave scorched ridges on the boards, which expanded polystyrene frequently does. (EPS).
The hot melt on the EPS is buzzed away as a result of our direction change. When it comes to precise and quick alignment of infamously flawed blanks, AkuShaper leads the industry.
No matter how long the boards are, a multitude of characteristics combine to make sure that there are just a few seconds between them.
Depending on how many boards are being cut each day, manually oiled machines might take anywhere from 30 minutes to an hour to grease. This is a requirement that is regularly disregarded and a common cause of failure in other systems.
Sl no | Topic |
1 | Market Segmentation |
2 | Scope of the report |
3 | Abbreviations |
4 | Research Methodology |
5 | Executive Summary |
6 | Introduction |
7 | Insights from Industry stakeholders |
8 | Cost breakdown of Product by sub-components and average profit margin |
9 | Disruptive innovation in the Industry |
10 | Technology trends in the Industry |
11 | Consumer trends in the industry |
12 | Recent Production Milestones |
13 | Component Manufacturing in US, EU and China |
14 | COVID-19 impact on overall market |
15 | COVID-19 impact on Production of components |
16 | COVID-19 impact on Point of sale |
17 | Market Segmentation, Dynamics and Forecast by Geography, 2024-2030 |
18 | Market Segmentation, Dynamics and Forecast by Product Type, 2024-2030 |
19 | Market Segmentation, Dynamics and Forecast by Application, 2024-2030 |
20 | Market Segmentation, Dynamics and Forecast by End use, 2024-2030 |
21 | Product installation rate by OEM, 2023 |
22 | Incline/Decline in Average B-2-B selling price in past 5 years |
23 | Competition from substitute products |
24 | Gross margin and average profitability of suppliers |
25 | New product development in past 12 months |
26 | M&A in past 12 months |
27 | Growth strategy of leading players |
28 | Market share of vendors, 2023 |
29 | Company Profiles |
30 | Unmet needs and opportunity for new suppliers |
31 | Conclusion |
32 | Appendix |