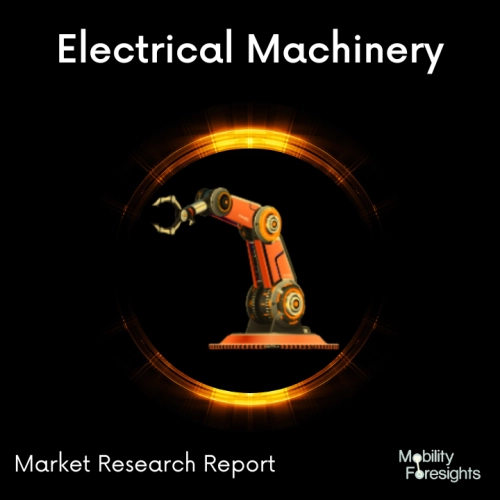
- Get in Touch with Us
Last Updated: Apr 25, 2025 | Study Period: 2024-2030
The process of vacuum forming involves heating a thermoplastic material until it reaches a predetermined melt flow index. At this stage, the material can be formed over a tool or mould using vacuum.
Vacuum Forming machines that are used for a range of applications use various plate sizes and are controlled by sophisticated CNC software to precisely tune the individual heaters, the time, the vacuum pressure, and ensure that the formed item is consistent each and every time.
The Global CNC vacuum forming machine market accounted for $XX Billion in 2023 and is anticipated to reach $XX Billion by 2030, registering a CAGR of XX% from 2024 to 2030.
For the development of 3D printed moulds for vacuum forming, FDM is a commonly used 3D print method. As a result, a consistent vacuum may be drawn throughout the entire tool since it permits printing in a wide variety of densities.
Additionally, FDM 3D print systems are capable of producing moulds from a variety of heat-resistant and long-lasting plastics, which increases the mould's longevity and durability. The use of 3D printing in the manufacture of industry tools like moulds has had a significant impact on the plastic thermoforming sector.
3D printing is a time and money-saving technique because it uses automated manufacturing, easily available supplies, quick design iterations, and market deployment.
Utilising wood moulds and a CNC-machined master template, their clients used thermoforming. The use of 3D printing and thermoforming technologies by Divide by Zero Technologies has simplified the entire process.
With little room for mistakes or manufacturing adjustments, 3D printing makes it possible for manufacturers to quickly translate ideas from a drawing board to actual products, reducing the amount of time needed for prototyping.
Additionally, with the advent of 3D printing, businesses now have the option of lowering their expenses for the quantity of storage space they require.
Divide by Zero Technologies is focused on introducing higher quality 3D Printing and other CNC technology as well as ongoing R&D to create new designs and concepts in existing products and their functionality.
Sl no | Topic |
1 | Market Segmentation |
2 | Scope of the report |
3 | Abbreviations |
4 | Research Methodology |
5 | Executive Summary |
6 | Introduction |
7 | Insights from Industry stakeholders |
8 | Cost breakdown of Product by sub-components and average profit margin |
9 | Disruptive innovation in the Industry |
10 | Technology trends in the Industry |
11 | Consumer trends in the industry |
12 | Recent Production Milestones |
13 | Component Manufacturing in US, EU and China |
14 | COVID-19 impact on overall market |
15 | COVID-19 impact on Production of components |
16 | COVID-19 impact on Point of sale |
17 | Market Segmentation, Dynamics and Forecast by Geography, 2024-2030 |
18 | Market Segmentation, Dynamics and Forecast by Product Type, 2024-2030 |
19 | Market Segmentation, Dynamics and Forecast by Application, 2024-2030 |
20 | Market Segmentation, Dynamics and Forecast by End use, 2024-2030 |
21 | Product installation rate by OEM, 2023 |
22 | Incline/Decline in Average B-2-B selling price in past 5 years |
23 | Competition from substitute products |
24 | Gross margin and average profitability of suppliers |
25 | New product development in past 12 months |
26 | M&A in past 12 months |
27 | Growth strategy of leading players |
28 | Market share of vendors, 2023 |
29 | Company Profiles |
30 | Unmet needs and opportunity for new suppliers |
31 | Conclusion |
32 | Appendix |