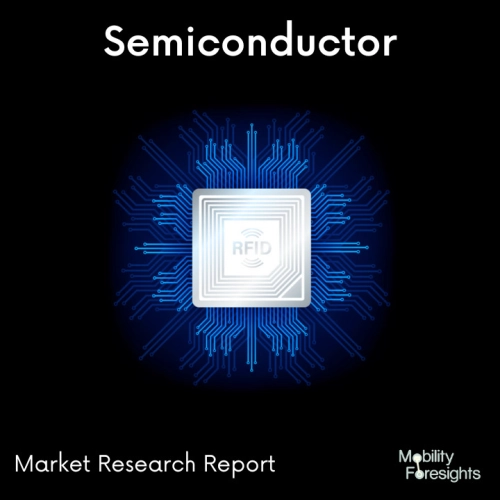
- Get in Touch with Us
Last Updated: Apr 25, 2025 | Study Period: 2023-2030
Chemical vapor deposition (CVD) is a vacuum deposition method used to produce high quality, and high-performance, solid materials.
The process is often used in the semiconductor industry to produce thin films CVD is a technique where a solid material is deposited from a vapor by some chemical reaction occurring on or in the vicinity of a normally heated substrate surface.
CVD is an example of vapor-solid reaction. The process is often used in the semiconductor industry to produce thin films. Chemical vapour deposition (CVD) is a technique that relies on the formation of a gaseous species containing the coating element within a coating retort or chamber.
Alternatively, the gaseous species may be generated external to the coating retort and introduced via a delivery system. Generally, nano-sized transition metal particles, e.gnickel, iron, cobalt, molybdenum and copper have been successfully used in CCVD either in oxide or metallic forms or as mixtures.
Common materials prepared by CVD are silicon oxide, silicon oxide is deposited by CVD by several processes. The sources of gases used in the deposition process are silane and oxygen, dichlorosilane, and nitrous oxide.
The main disadvantage for thermal atmospheric CVD is the lack of precursors that are highly volatile, nontoxic and nonpyrophoric. The main factors that determine the film's deposition rate and properties are the delivery rate of the precursor and the temperatures of both the vaporizer and the substrate.
Global cobalt CVD system market accounted for $XX Billion in 2022 and is anticipated to reach $XX Billion by 2030, registering a CAGR of XX% from 2023 to 2030.
The Volta CVD Cobalt system introduces a new materials era for extending copper interconnect technology. It promotes copper seed layer coverage by improving copper wetting, resulting in a thin, continuous, conformal layer that facilitates repair of discontinuities and formation of a robust seed layer. This high-quality layer in turn promotes void-free copper gap fill at the most advanced nodes.
Shrinking geometries also result in higher resistance as well as greater susceptibility to EM failures in the copper lines. A high-quality bond at the interface between the copper and dielectric barrier layer is vital for avoiding EM failures.
The Volta systemâs best-in-class (>100:1) selective metal capping process strengthens adhesion at the copper-dielectric interface to improve EM performance by an order of magnitude without increasing line resistance or degrading time-dependent dielectric breakdown.
The combined use of Volta CVD Cobalt as both liner and selective metal cap enables complete encapsulation of copper lines and ensures the most robust interconnect reliability for the 2Xnm node and beyond.
Sl no | Topic |
1 | Market Segmentation |
2 | Scope of the report |
3 | Abbreviations |
4 | Research Methodology |
5 | Executive Summary |
6 | Introduction |
7 | Insights from Industry stakeholders |
8 | Cost breakdown of Product by sub-components and average profit margin |
9 | Disruptive innovation in the Industry |
10 | Technology trends in the Industry |
11 | Consumer trends in the industry |
12 | Recent Production Milestones |
13 | Component Manufacturing in US, EU and China |
14 | COVID-19 impact on overall market |
15 | COVID-19 impact on Production of components |
16 | COVID-19 impact on Point of sale |
17 | Market Segmentation, Dynamics and Forecast by Geography, 2023-2030 |
18 | Market Segmentation, Dynamics and Forecast by Product Type, 2023-2030 |
19 | Market Segmentation, Dynamics and Forecast by Application, 2023-2030 |
20 | Market Segmentation, Dynamics and Forecast by End use, 2023-2030 |
21 | Product installation rate by OEM, 2023 |
22 | Incline/Decline in Average B-2-B selling price in past 5 years |
23 | Competition from substitute products |
24 | Gross margin and average profitability of suppliers |
25 | New product development in past 12 months |
26 | M&A in past 12 months |
27 | Growth strategy of leading players |
28 | Market share of vendors, 2023 |
29 | Company Profiles |
30 | Unmet needs and opportunity for new suppliers |
31 | Conclusion |
32 | Appendix |