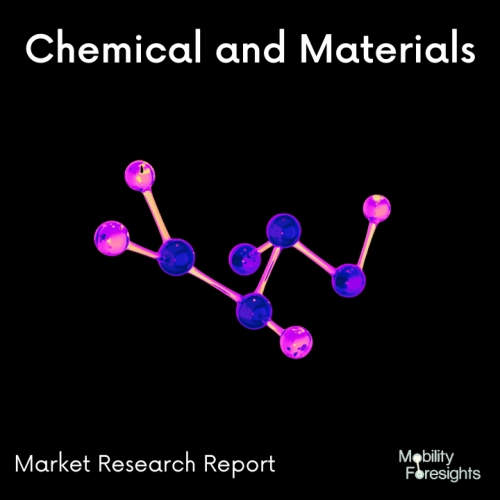
- Get in Touch with Us
Last Updated: Apr 25, 2025 | Study Period: 2024-2030
Composite board resins are a type of adhesive that is used to bond together two or more pieces of wood or other materials. They are typically made from a mixture of resin and hardener, and they are available in a variety of forms, including liquid, paste, and film. Composite board resins are used in a variety of applications, including the construction of furniture, boats, and other structures.
They are also used in the manufacture of composite materials, such as fiberglass and carbon fiber.They are strong and durable.They are resistant to water and other chemicals.They are easy to use and apply.
They are available in a variety of colors and finishes.Here are some of the things to consider when choosing a composite board resin:The type of material one is bonding together.The strength and durability one need.The weather conditions one will be using the product in.The color and finish one want.
When choosing a composite board resin, it is important to consider the type of material one is bonding together, the strength and durability one needs, the weather conditions one will be using the product in, and the color and finish one wants. It is also important to read the instructions carefully and follow them closely to ensure proper application.
Composite board resins can be a great way to bond together two or more pieces of wood or other materials. They are strong, durable, and easy to use. However, it is important to choose the right resin for needs and to follow the instructions carefully to ensure proper application.
The Global Composite Board Resins Market accounted for $XX Billion in 2023 and is anticipated to reach $XX Billion by 2030, registering a CAGR of XX% from 2024 to 2030.
For particle board (PB), dry processed fiber board (MDF, HDF, THDF), oriented strand board (OSB), and plywood (PWL), Metadynea offers a variety of formaldehyde-based resins. This includes resins for special uses like water resistant boards, HDF flooring, etc. as well as emission classes like natural wood (AsWood) and emissions like E1, CARB II. .
For CARB II, various urea formaldehyde (UF) and melamine-modified urea formaldehyde (mUF) resins are used in single resin and twin resin systems. Melamine-urea formaldehyde resins (MUF) are used in P3 and P5 boards.
A set of formaldehyde-based resins known as AsWood was created in Krems and emits formaldehyde like untreated, real wood.There are numerous melamine-urea formaldehyde resins, melamine-urea formaldehyde resins, and melamine-phenol-urea formaldehyde resins (MUPF) resins for improved water resistance qualities (P3, P5, P7, etc.).
What they refer to as polymer materials are mostly made up of two types of resins: thermosets and thermoplastics. Polymersâlarge molecules made up of lengthy chains of smaller molecules or monomersâare the building blocks of these resins.
The majority of composites are created using thermoset resins. They undergo a process known as polymerization, also known as cross-linking, which turns them from a liquid to a solid. Thermosetting resins are cured before being utilized to create completed objects by using heat, a catalyst, or a combination of the two. Thermoset resins are solid after curing and cannot be changed back to their liquid state.
ResinDek is not the same flooring panel as moisture-resistant composite resin board, which is utilized for mezzanine decking surfaces. ResinDek flooring panels outperform resin boards by a wide margin, and they come with a product warranty that includes pallet jack loads.
When built in accordance with the IAPMO Uniform Evaluation Service Report, ResinDek panels have been independently assessed and authorized for use in Types I through V construction and as a component of a fire-rated assembly.
High-performing, low-emitting, and customized to the demands and operations of the customer are Arclin's resins, catalysts, and scavengers for particleboard, MDF, and hardboard. Additionally, they may collaborate with mid- and downstream customers to create new products and market prospects thanks to their application experience.
Sl no | Topic |
1 | Market Segmentation |
2 | Scope of the report |
3 | Abbreviations |
4 | Research Methodology |
5 | Executive Summary |
6 | Introduction |
7 | Insights from Industry stakeholders |
8 | Cost breakdown of Product by sub-components and average profit margin |
9 | Disruptive innovation in the Industry |
10 | Technology trends in the Industry |
11 | Consumer trends in the industry |
12 | Recent Production Milestones |
13 | Component Manufacturing in US, EU and China |
14 | COVID-19 impact on overall market |
15 | COVID-19 impact on Production of components |
16 | COVID-19 impact on Point of sale |
17 | Market Segmentation, Dynamics and Forecast by Geography, 2024-2030 |
18 | Market Segmentation, Dynamics and Forecast by Product Type, 2024-2030 |
19 | Market Segmentation, Dynamics and Forecast by Application, 2024-2030 |
20 | Market Segmentation, Dynamics and Forecast by End use, 2024-2030 |
21 | Product installation rate by OEM, 2023 |
22 | Incline/Decline in Average B-2-B selling price in past 5 years |
23 | Competition from substitute products |
24 | Gross margin and average profitability of suppliers |
25 | New product development in past 12 months |
26 | M&A in past 12 months |
27 | Growth strategy of leading players |
28 | Market share of vendors, 2023 |
29 | Company Profiles |
30 | Unmet needs and opportunity for new suppliers |
31 | Conclusion |
32 | Appendix |