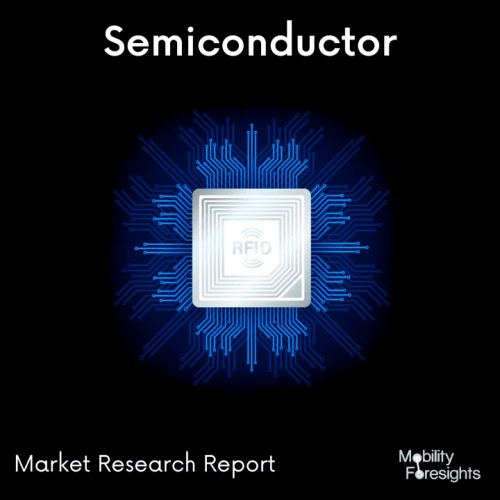
- Get in Touch with Us
Last Updated: Apr 25, 2025 | Study Period:
By combining machine sensor data that detects vibration and other characteristics (in real-time) with cutting-edge machine monitoring software, condition monitoring (CM), a maintenance strategy, anticipates machine health and safety.
State monitoring (CM) is the act of keeping an eye on a certain machine condition (such as temperature, vibration, etc.) in order to spot any changes that could be signs of an impending failure.
Vibration analysis and vibration monitoring, oil analysis, and temperature tracking are typical examples of condition-based monitoring. Sensors collect real-time data, giving a continuous way to test and monitor asset health.
By using condition monitoring, it is possible to plan maintenance or take other steps to reduce the likelihood of subsequent damage and its effects.
The particular advantage of condition monitoring is that problems that might reduce a normal lifespan may be fixed before they become significant failures.
On a variety of equipment, including rotating machinery, auxiliary systems, and parts like compressors, pumps, motors, and presses, condition monitoring techniques are utilised.
Implementing condition monitoring is a key component of predictive maintenance since it enables the scheduling of maintenance and the implementation of preventative measures to stop additional failure and ensuing unexpected downtime.
The Global Condition Monitoring sensors market accounted for $XX Billion in 2023 and is anticipated to reach $XX Billion by 2030, registering a CAGR of XX% from 2024 to 2030.
New sensor for ongoing condition monitoring is announced by SICK.
SICK has announced the release of its MPB10 Multi-Physics Box condition monitoring sensor, a ground-breaking and tough bolt-on gadget created to deliver continuous, real-time service data from industrial machines, such as electric motors, pumps, fans, and conveyor systems, even in the harshest industry environments.
The MPB10 is an all-in-one device designed to make it simple to monitor and understand vibration, shock, and temperature measurement data given directly from the heart of machines.
It is SICK's first dedicated condition monitoring sensor. The MPB10 offers service data to facilitate more economical predictive maintenance procedures that can increase plant availability, maximise operational life, and safeguard product and process quality.
The SICK MPB10 detects temperature, vibration, and shocks, which may be early warning indicators of impending equipment failure.
Users are given pre-processed information that is clear, short, and simple to understand and may be customised for the machine and process.
Through the use of the sensor's MEMS parts, the SICK MPB10 can detect vibrations ( 8 g) and shocks up to 200 g in all three axes.
According to DIN ISO 10816-3 specifications, vibration thresholds in rotating machinery including electric motors, fans, turbines, and generators can be monitored using multi-stage warnings.
The availability of the machine may be enhanced, product and process quality can be safeguarded, and operators have a greater chance of extending the life of their equipment by avoiding harmful temperatures, shocks, or vibrations.
Reactive interventions can be avoided, and time-consuming routine preventative inspections can be less frequently performed, which reduces maintenance effort and costs.
Sl no | Topic |
1 | Market Segmentation |
2 | Scope of the report |
3 | Abbreviations |
4 | Research Methodology |
5 | Executive Summary |
6 | Introduction |
7 | Insights from Industry stakeholders |
8 | Cost breakdown of Product by sub-components and average profit margin |
9 | Disruptive innovation in the Industry |
10 | Technology trends in the Industry |
11 | Consumer trends in the industry |
12 | Recent Production Milestones |
13 | Component Manufacturing in US, EU and China |
14 | COVID-19 impact on overall market |
15 | COVID-19 impact on Production of components |
16 | COVID-19 impact on Point of sale |
17 | Market Segmentation, Dynamics and Forecast by Geography, 2024-2030 |
18 | Market Segmentation, Dynamics and Forecast by Product Type, 2024-2030 |
19 | Market Segmentation, Dynamics and Forecast by Application, 2024-2030 |
20 | Market Segmentation, Dynamics and Forecast by End use, 2024-2030 |
21 | Product installation rate by OEM, 2023 |
22 | Incline/Decline in Average B-2-B selling price in past 5 years |
23 | Competition from substitute products |
24 | Gross margin and average profitability of suppliers |
25 | New product development in past 12 months |
26 | M&A in past 12 months |
27 | Growth strategy of leading players |
28 | Market share of vendors, 2023 |
29 | Company Profiles |
30 | Unmet needs and opportunity for new suppliers |
31 | Conclusion |
32 | Appendix |