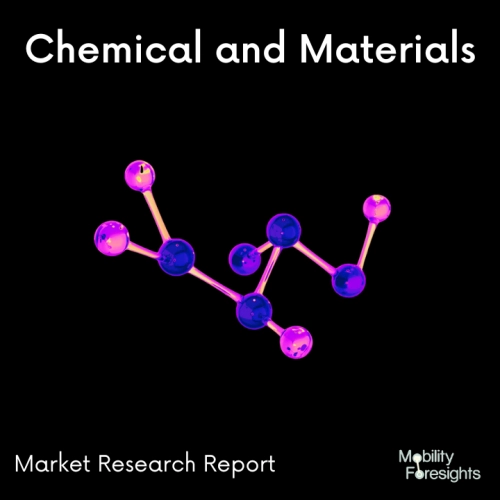
- Get in Touch with Us
Last Updated: Apr 25, 2025 | Study Period: 2024-2030
Conductive coating is an extrinsic modification to fabric substrates that may be accomplished with conductive inks. The conductive inks must comprise a suitable highly conductive metal precursor such as Ag (silver), Cu (copper), or AL (aluminum) nanoparticles (NPs), alloys or the listed metals, core/shell systems, and a carrier vehicle.
The majority of them are water-based. To generate electrically active designs, these specialty inks may be printed onto a variety of substrates, including fabrics.
Sheet-based inkjet and screen-printing technologies are ideal for low-volume, high-precision work and allow conductive inks to be produced on both natural and synthetic material substrates (ibid). Conductive polymers can also be used as conducting inks without the addition of any other materials.
Conductive polymers may also be used as conducting inks without the addition of any metals in a variety of printing methods such as screen printing, gravure printing, roll-to-roll printing, and inkjet printing. One of the issues with printing conductive polymers is the resolution of the paste, whose thickness varies depending on the procedure used (Ibid).
Smart or functional nonwoven materials may include smart coatings or inner layers that offer functionality like conductivity, sensor capabilities, or antibacterial properties. providing a functional coating to a nonwoven material preserves some or all of the nonwoven's original performance properties while providing additional functionality.
Resins, polymers, and high-tech materials such as carbon nanotubes can be used to produce smart coatings with unique functionality. Coated nonwoven textiles will have combination qualities that neither component alone can provide.
Intelligent fabrics with many different combinations of performance characteristics such as conductivity, bacterial resistance, or sensing capabilities can be produced by selecting the combination of base fabric and functional coating, as well as heated nonwoven materials for medical, marine, and military applications.
Traditional neural interfaces use metallic electrodes, which have achieved a plateau in terms of providing safe stimulation at high resolution, or rather with high density of microelectrodes with enhanced spatial selectivity, in recent years.
It has become obvious that lowering the size of electrodes is essential to permit larger electrode counts from the implant device in order to obtain higher resolution.
Organic electrode coatings, which typically provide a softer, more roughened surface to enable both improved charge transfer and lower mechanical mismatch with neural tissue, can address the limitations of interfacing electrodes such as low charge injection limits, mechanical mismatch, and foreign body response.
Coating electrodes with conductive polymers or carbon nanotubes increases charge transfer area significantly.. These organic conductors safely stimulate tissue while avoiding unwanted chemical reactions and cell harm.
However, conductive polymers have poor mechanical characteristics because they are brittle. Because they may be chemically changed to form a flexible and conductive scaffold, hydrogel polymers are a versatile coating choice for electrodes.
The in vivo chronic inflammatory response of these conductive hydrogels, on the other hand, is unclear. A more recent strategy proposes using encapsulated neurons inside hydrogel coverings to tissue design the electrode contact.
This strategy may give a mechanism for activating tissue at the cellular level; however, various technological hurdles must be overcome before this new notion can be demonstrated to be feasible. The review focuses on the several organic coatings that have been studied.
The Global Conductive Electrode Coatings Market accounted for $XX Billion in 2023 and is anticipated to reach $XX Billion by 2030, registering a CAGR of XX% from 2024 to 2030.
Hioki is happy to announce the release of the RM2610 Electrode Resistance Measurement System.
The RM2610 separates and quantifies the resistance properties of electrode sheets, which are a significant component of lithium-ion batteries (LIBs), as two components: composite layer resistance and interface resistance between the composite layer and collector.
The technology enables users to visualize these two characteristics by measuring the surface of the electrode sheet with a test fixture consisting of an array of test probes and then quantifying them using proprietary analytical procedures.
The RM2610 checks electrode sheet properties and quality trends, as well as helping LIB developers visualize how resistance characteristics alter in response to changes in composite, by quantifying resistance characteristics that were previously hard to visualize.
Electrode sheets are created by coating a collector (the part that attracts electricity; typically with an aluminum positive electrode and a copper negative electrode) with a liquid (the composite) containing ingredients such as an active substance (which captures and releases lithium ions) and a conductive auxiliary agent (which facilitates electron conductivity).
The sheets are utilized in lithium-ion batteries as electrodes. Because lower internal resistance equals better output and service life, it is critical to monitor the resistance properties of electrode sheets, which are a significant component of lithium-ion batteries.
However, it has hitherto been difficult to assess electrode sheets until the lithium-ion battery in which they are employed was entirely built.