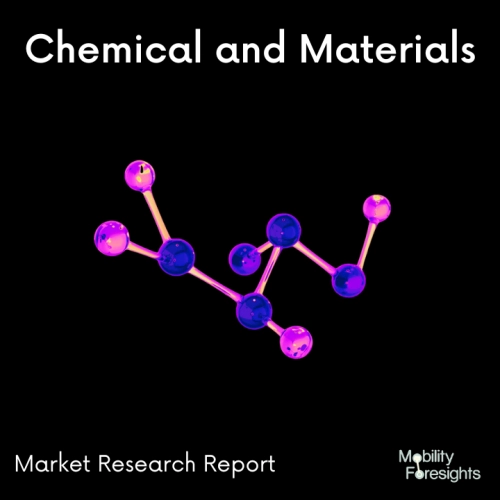
- Get in Touch with Us
Last Updated: Apr 25, 2025 | Study Period: 2023-2030
The majority of conductive fibres are made of stainless steel, graphite, or carbon. Carbon is applied to the outside of the fibre in static-sensitive commercial areas to make conductive and static-dissipative carpets.
Static charges can safely discharge through the carpet layers and into a ground source, like an electrical conduit, thanks to external conductivity, which enables them to establish touch with the conductive element in the fibres.
Conductivity is a permanent feature because conductive components are introduced into the material during the production process.
For a manufacturing environment, conductive flooring systems offer the lowest charge generation and quickest charge dissipation. A copper strip connecting the flooring to a grounded connection, such as a wall outlet, grounds the flooring.
A non-conductive or less conductive substrate serves as the foundation for conductive fibres, which are subsequently coated or implanted with electrically conductive materials, most frequently PEDOT, carbon, nickel, copper, gold, or silver. A tiny powdered glass fiber called milled fibers (1/32") is used as reinforcement to boost the mechanical strengths of resins.
The Global conductive flooring milled fibres market accounted for $XX Billion in 2022 and is anticipated to reach $XX Billion by 2030, registering a CAGR of XX% from 2023 to 2030.
To lessen electrical conductivity, floor coverings and coatings are mixed with chopped and milled fibres from SGL Carbon. As a result of the flooring's dispersion, a continuous network of conductive fibres is formed. SGL Carbon provides options for both water- and resin-based systems.
There are 60 and 100 micron lengths of Tenax milled fibres available. Individual fibres' aspect ratios are adequate to give polymer complexes both mechanical reinforcement and electrical conductivity. Dimensionally stable and distortion-free components are those reinforced with milled carbon fibres.
Applications for conductive flooring, computer parts, quick prototyping, sealing, and electrical device parts are typical examples. All resins, including powders, dry mixes, adhesives, aqueous dispersion systems, and injection moulding compounds, use Tenax milled fibres.
Sl no | Topic |
1 | Market Segmentation |
2 | Scope of the report |
3 | Abbreviations |
4 | Research Methodology |
5 | Executive Summary |
6 | Introduction |
7 | Insights from Industry stakeholders |
8 | Cost breakdown of Product by sub-components and average profit margin |
9 | Disruptive innovation in the Industry |
10 | Technology trends in the Industry |
11 | Consumer trends in the industry |
12 | Recent Production Milestones |
13 | Component Manufacturing in US, EU and China |
14 | COVID-19 impact on overall market |
15 | COVID-19 impact on Production of components |
16 | COVID-19 impact on Point of sale |
17 | Market Segmentation, Dynamics and Forecast by Geography, 2023-2030 |
18 | Market Segmentation, Dynamics and Forecast by Product Type, 2023-2030 |
19 | Market Segmentation, Dynamics and Forecast by Application, 2023-2030 |
20 | Market Segmentation, Dynamics and Forecast by End use, 2023-2030 |
21 | Product installation rate by OEM, 2023 |
22 | Incline/Decline in Average B-2-B selling price in past 5 years |
23 | Competition from substitute products |
24 | Gross margin and average profitability of suppliers |
25 | New product development in past 12 months |
26 | M&A in past 12 months |
27 | Growth strategy of leading players |
28 | Market share of vendors, 2023 |
29 | Company Profiles |
30 | Unmet needs and opportunity for new suppliers |
31 | Conclusion |
32 | Appendix |