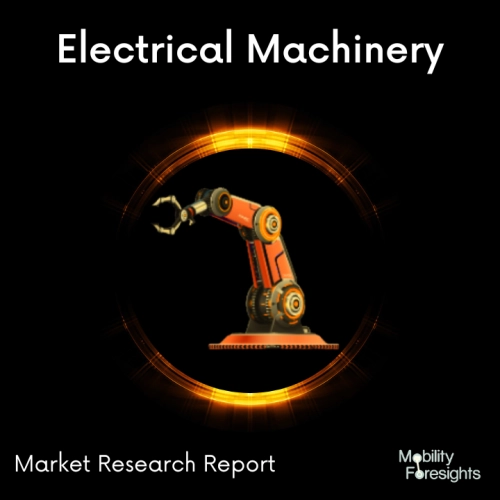
- Get in Touch with Us
Last Updated: Apr 25, 2025 | Study Period: 2024-2030
In a variety of situations, conformal coatings can be used to shield printed circuit boards from moisture, salt spray, chemicals, and temperature extremes, preventing things like corrosion, mould growth, and electrical malfunctions.
Circuit boards, components, and other electronic equipment are shielded from damaging environmental factors such dampness, thermal shock, static electricity, vibration, and contamination via conformal coating, a specially designed polymeric film-forming substance.
Circuit boards can be coated with conformal coating, a protective chemical covering that is non-conductive. Its function is to shield electronic circuitry from harm brought on by contamination, salt spray, moisture, fungus, dust, and corrosion brought on by severe or extreme environments.
The Global Conformal Coating Dispensing Equipment Market accounted for $XX Billion in 2022 and is anticipated to reach $XX Billion by 2030, registering a CAGR of XX% from 2024 to 2030.
More Reliable, Effective Conformal Coating and Dispensing Technologies are Introduced by Nordson ASYMTEK The new PanoramaTM S-overlapping Lines line operations reduce the amount of manufacturing floor area while providing conformal coating process control in a compact footprint.
By utilising the lower compartment in each piece of equipment for the hot return or flash-off operation, this creative, patent-pending line architecture reduces the length of the line by 50%. The well-known Select Coat® SL-940 coater, an automated coating inspection system, and a curing module are all part of this range.
Inter-machine connection (Industry 4.0) provides for the provision of real-time Cpk so that coating productivity can be easily monitored, and an integrated coating thickness sensor enables the user to change the coating programme speed depending on a thickness trend fluctuation.
In order to further improve UPH and quality outcomes, the new precision dispenser, ForteTM Series, features a dual-simultaneous dispense head with two high-frequency IntelliJet® Jetting Systems that dispense simultaneously.
This reduces dispense time by 50% and automatically corrects for workpiece and individual component rotational skew. In order to provide precise dispensing performance for a variety of fluid volumes, from large to micro-levels, a new series of progressive cavity pumps will be created. For dispensing narrow lines of two-component fluids at low flow rates, a single pump type is optimal.
Sl no | Topic |
1 | Market Segmentation |
2 | Scope of the report |
3 | Abbreviations |
4 | Research Methodology |
5 | Executive Summary |
6 | Introduction |
7 | Insights from Industry stakeholders |
8 | Cost breakdown of Product by sub-components and average profit margin |
9 | Disruptive innovation in the Industry |
10 | Technology trends in the Industry |
11 | Consumer trends in the industry |
12 | Recent Production Milestones |
13 | Component Manufacturing in US, EU and China |
14 | COVID-19 impact on overall market |
15 | COVID-19 impact on Production of components |
16 | COVID-19 impact on Point of sale |
17 | Market Segmentation, Dynamics and Forecast by Geography, 2024-2030 |
18 | Market Segmentation, Dynamics and Forecast by Product Type, 2024-2030 |
19 | Market Segmentation, Dynamics and Forecast by Application, 2024-2030 |
20 | Market Segmentation, Dynamics and Forecast by End use, 2024-2030 |
21 | Product installation rate by OEM, 2023 |
22 | Incline/Decline in Average B-2-B selling price in past 5 years |
23 | Competition from substitute products |
24 | Gross margin and average profitability of suppliers |
25 | New product development in past 12 months |
26 | M&A in past 12 months |
27 | Growth strategy of leading players |
28 | Market share of vendors, 2023 |
29 | Company Profiles |
30 | Unmet needs and opportunity for new suppliers |
31 | Conclusion |
32 | Appendix |