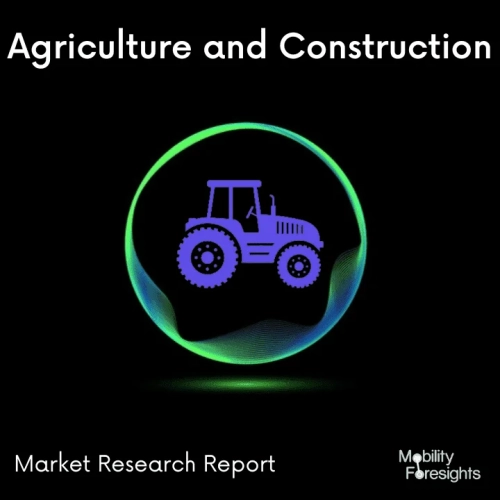
- Get in Touch with Us
Last Updated: Apr 25, 2025 | Study Period:
An exhaust system directs the exhaust gases produced by a combustion within an engine or stove. The whole system, which comprises one or maybe more exhaust pipes, transfers the engine's burnt gases.
An exhaust system directs the exhaust air produced by an ignition within an engine or stove. The whole system, which includes one or more exhaust pipes, transfers the engine's burnt gases.
A defective exhaust system causes lower fuel efficiency, rumbling noises from the exhaust pipe or muffler, hazardous gases, and may emit a rotten egg odour. This approach is used to keep harmful gases from entering the automobile and making passengers sick.
Although these gases were nevertheless harmful to the environment, they are less so than those produced by engines.
These components typically have a 100,000-mile lifespan before failing due to an exhaust leak, incomplete combustion fuel, engine misfire, or external damage.
The muffler muffles or dampens engine noise while improving exhaust gas flow. Improved flow rate equates to better performance in all parts of construction equipment systems.
S No | Overview of Development | Development Detailing | Region of Development | Possible Future Outcomes |
1 | Hyundai launches new A-series wheeled excavators | Hyundai Construction Equipment has unveiled a completely new line of A-Series wheeled excavators, powered by EU Stage V diesel engines. The four machines, with operating weights of 14-23 tonnes, feature low emission Cummins diesel engines with a combined after-treatment system and no requirement for EGR, offering customers increased productivity, with lower emissions. | Europe | This would enhance better Technologies and production |
SI no | Timeline | Company | Developments |
1 | August 2021 | SM Auto | SM Auto and Proventia have been partnered to design, validate and manufacture advanced Exhaust After-Treatment(EAT) emission control systems for Indian agricultural and commercial vehicles. |
2 | June 2021 | IP Rings Ltd | IP Rings and U.K based Eminox has signed an agreement to develop exhaust after-treatment systems for India. |
3 | March 2021 | Faurecia | Faurecia and Immersion have been partnered to introduce haptic automotive technologies. |
Aftermarket exhaust components can increase peak power by decreasing back pressure in the exhaust system.
Although the European Union Block Exemption Regulations 1400/2002 restrict manufacturers from rejecting warranty claims if the aftermarket parts are of equal quality and specifications to the original parts, these components may break factory warranties in some situations.
To keep toxic and/or unpleasant fumes away from the machine's users, an exhaust pipe must be correctly constructed.
Indoor generator systems, such as those used in construction equipment and furnaces, may quickly fill an enclosed area with harmful exhaust gases such as hydrocarbons, carbon monoxide, and nitrogen oxides.
Emission regulations are getting increasingly stringent across the world, and as a result, there is a rising demand for reductions in exhaust gas emission types and quantities.
The combination of after-treatment devices enables car makers and exhaust system manufacturers to regulate vehicle emissions while remaining below regulatory limits.
The most common after-treatment device combinations are SCR and DPF. More than 70% of all gaseous and particle pollution is eliminated by this combination.
The SCR converts NOx to N2 (nitrogen) and water in the presence of a reductant, while the DPF filters particulate particles. At the moment, clean cars have only a minimal impact on the exhaust system sector.
They are, nevertheless, expected to have a considerable impact in the near future. As a result, higher sales of clean cars are expected to limit the growth of the exhaust system market.
Vehicle weight reduction is becoming increasingly important in order to meet with stringent pollution and fuel efficiency regulations and avoid hefty penalties levied by government agencies.
Vehicle weight reduction decreases fuel consumption and CO2 emissions significantly because lightweight construction equipment takes less fuel to overcome less inertia, decreasing the power required to propel the vehicle.
The Global Construction Equipment Exhaust System Market can be segmented into following categories for further analysis.
Construction Equipment Exhaust System Market By Application
Construction Equipment Exhaust System Market By Usage Classification Type
Construction Equipment Exhaust System Market By Operational Technology Type
Construction Equipment Exhaust System Market By After Treatment Device Type
Construction Equipment Exhaust System Market By Regional Classification
SI no | Timeline | Company | Developments |
1 | September 2021 | Benteller | The EU-7 emission standard for Internal Combustion Engines is expected in 2025. It offers a solution to ensure that the exhaust gas treatment reaches the optimum operating temperatures faster. |
2 | June 2021 | Hyundai | Hyundai launches the new A-series wheeled excavators powered by EU stage V low emission Diesel Engines. This also has a Flex-Module two-can Exhaust system. |
3 | May 2021 | Finse | Finse has introduced a new thermal insulation product in order to maintain the functionality of SCR emission control systems and ensure a safe working environment. |
4 | February 2021 | JCB Power system | JCB Power system has revealed the new range of Stage V Engines in order to lower fuel consumption thereby reducing CO2 and other exhaust emissions. |
Construction is one of the world's fastest growing industries, and the usage of automation and machine control technologies is rapidly rising.
Modern control technologies and advanced automation are already providing benefits to developed nations, such as improved productivity, cheaper costs, perfect predictability, efficiency, quality, and safety, among many other things.
Equipment manufacturers have created novel and intelligent road construction technologies to increase the pace of higher-quality road construction. It is long past time for project management businesses to use such technologies.
Common rail fuel injection, four-valve technology, turbochargers, charge air cooling, viscous fans, and electronic engine management are engine technology mainstays for balancing power production, consumption, and emissions standards. In terms of exhaust emission technology, well-known technologies are also in use.
Diesel oxidation catalytic converter (DOC), diesel particulate filter (DPF), and selective catalytic reduction (SCR) exhaust gas emissions control systems are always managed to install in vehicle emissions Stage V engines on Construction vehicles, with differences in exhaust gas recirculation (EGR) now found only in internal engine technology.
Among all emission reduction measures, enhancing equipment maintenance and operations might be viable, appealing, and cost-effective approaches for implementation.
Diesel particulate filters for construction equipment keep unwanted soot from exiting diesel engines through the exhaust pipe. This looks to be a simple process, however the architecture of DPF is intended to assure safe usage and maximum effect.
Depending on the circumstances, a variety of filter techniques may be used to reduce particle emissions, depending on engine technology and application characteristics. As a result, the exhaust gas is forced to travel through the channels' walls.
SI no | Timeline | Company | Sales |
1 | Q3-2021 | Faurecia | At the end of third quarter, the group sales of faurecia was â¬3.42 billion and in 2020 the group sales was â¬3.82 billion. |
Global construction equipment sales have fallen. Infrastructure investments, residential, commercial, and industrial construction, mining and well construction, and institutional spending are all elements impacting construction equipment manufacturers.
Countries such as the United States are among the worst hit. Hospitals and other medical facilities, labs, and shipping and transportation infrastructure, on the other hand, are in great demand.
Furthermore, numerous countries have begun to gradually resume activity in a range of industries, including the construction business.
FHC - Sustainion Group is a part of the most recent development in the industry of construction equipment exhaust systems by using the most modern filtrate protection system technology.
Ceramic wall-flow filters will virtually entirely remove carbon particulates, including small particulates with a diameter of less than 100 nanometres (nm), with an efficiency of >95 percent in mass and >99 percent in particle number, from construction equipment exhaust systems.
Because a steady flow of soot into the filter would eventually choke it. The soot particulate burn off will mostly create water and a trace quantity of CO2 (less than 0.05 percent of the CO2 emitted by the engine).
Thunder Creek Equipment is a market contributor to the manufacturing line of construction equipment-based exhaust systems. Thunder Creek Equipment offers a pickup-truck-mounted DEF-dispensing system as well as a 50-gallon tote-style DEF-dispensing system.
Larger DEF-handling equipment from the company includes lube/service trailers that can incorporate a DEF tank into their multi-tank/multi-fluid design, fueling trailers that can encompass DEF volumes ranging from 40 to 330 gallons and fuel volumes ranging from 500 to 990 gallons, and DEF-specific trailers that can handle 500 or 990 gallons.
They might be utilised in wet hose fueling operations. All Thunder Creek systems include the company's patent-pending "Two-in-One" pumping technology.
which enables a single piece of hardware to flow DEF into a vehicle's tank from a bulk container on a pickup truck or trailerâas well as replenish the bulk container. During both operations, Micro Matic closed-system components are employed to protect DEF purity.
Sl no | Topic |
1 | Market Segmentation |
2 | Scope of the report |
3 | Abbreviations |
4 | Research Methodology |
5 | Executive Summary |
6 | Introduction |
7 | Insights from Industry stakeholders |
8 | Cost breakdown of Product by sub-components and average profit margin |
9 | Disruptive innovation in the Industry |
10 | Technology trends in the Industry |
11 | Consumer trends in the industry |
12 | Recent Production Milestones |
13 | Component Manufacturing in US, EU and China |
14 | COVID-19 impact on overall market |
15 | COVID-19 impact on Production of components |
16 | COVID-19 impact on Point of sale |
17 | Market Segmentation, Dynamics and Forecast by Geography |
18 | Market Segmentation, Dynamics and Forecast by Product Type |
19 | Market Segmentation, Dynamics and Forecast by Application |
20 | Market Segmentation, Dynamics and Forecast by End use |
21 | Product installation rate by OEM, 2024 |
22 | Incline/Decline in Average B-2-B selling price in past 5 years |
23 | Competition from substitute products |
24 | Gross margin and average profitability of suppliers |
25 | New product development in past 12 months |
26 | M&A in past 12 months |
27 | Growth strategy of leading players |
28 | Market share of vendors, 2024 |
29 | Company Profiles |
30 | Unmet needs and opportunity for new suppliers |
31 | Conclusion |
32 | Appendix |