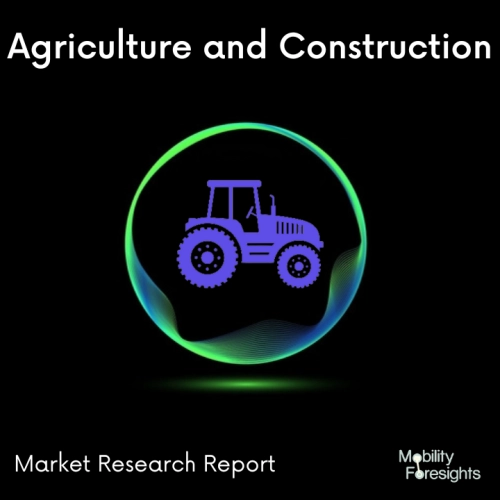
- Get in Touch with Us
Last Updated: Apr 25, 2025 | Study Period: 2024-2030
Construction equipment drivetrain systems have evolved to meet the needs of todayâs customers. OEMs continue to develop systems that deliver better efficiency, higher performance, higher durability,ty, and improved operator comfort.
As a result, new technologies such as diesel-electric hybrids, continuously variable transmissions, high-efficiency hydrostatics, and electronically controlled powershift transmissions have been developed. However, the type of transmission varies due to the wide disparity in construction equipment machine forms.
Each system involves a combination of axles and a hydrostatic or Synchromesh transmission with a torque converter, with semi-automatic or fully automatic operation via the electronic control unit that manages the entire system.
Powershift transmissions utilize friction clutches to change the power flow from one ratio to another within the transmission. Friction modifiers are added to provide smooth clutch operation in powershift transmissions and reduce chatter in braking systems.
But in construction applications, with lots of starts and stops in muddy terrain with high rolling resistance, or having smooth, controllable startup power in front of a paver, an automatic transmission is the better choice. Nothing can beat a torque converter in those applications when it comes to maintaining 100-percent boost engine power up and down through the g.ears
Transmissions with h dry clutch to be abused or overheat because an automatic is 100-percent fluid drive power. However, in a steady-state cruise application in pure highway mode, automated manual transmission is helpful.
The appeal of AT (Automatic transmission) can go far beyond work-site preferences, regardless of safety and fuel economy. âAT allows less-skilled drivers to be productive and to be moconcentratedate on On-site work. It also helps with drivers do not get as fatigued.
At the same time the concept of âdown speedingâ â or operating a diesel at lower rpms while at cruise speeds â is being driven by the push for better fuel economy. Automatic transmission can do these things better. When designing both the engine and the transmission it should be integrated to share critical information via ECU.
The transmission can manage all this information and deliver the best performance possible given all those criterA. As manual transmission canât do this consistently.
Considering a scenario, Wheel loader operators have one of the most common shortcuts is high-speed shifting when operators fail to make a complete stop when shifting between forward and reverse.
The average loader operator can make close to 600 such shifts a day, totaling over 200,000 high-speed shifts per year. There will be no time to slow down, production numbers will outweigh damage to the machine. The combined weight of the machine with payload and related force and strain gets directed into the drivetrain and torque converter, possibly shortening the life of these components.
Designers of multi-stage gearboxes have the tasks of ensuring the general requirements for any new vehicle units, namely improved reliability and rigidity, as well as modularity of the structure with smaller dimensions and weight; - implementation of special requirements for gearboxes, namely, improving speed, providing the required number of stages and the required range of gear ratios, ensuring smooth gearshift without breaking the power flow, providing the ability to test individual modules of the gearbox, the transmission of full power when reversing, etc.
In addition to pursuing improvements in conventional automatic transmissions, which dominate Heavy-duty vehicles in the United States, a variety of alternative transmission designs are being developed and introduced into production.
Volvo, Mack, Daim,ler, and Eaton (with a partnership with Cummins) have developed highly integrated powertrains that share unprecedented levels of proprietary information between the engine and transmission to deliver optimal fuel economy at all times.
The global construction equipment transmission market is estimated at $XX Billion currently, growing at XX% CAGR till 2025.
Volvo machines feature second-generation OptiShift technology that allows operators to customize the lock-up engagement of their machines. The improved OptiShift also integrates the Volvo-patented Reverse-By-Braking (RBB) function and the new torque converter with lock-up, creating a direct drive between the engine and transmission. Volvo has also developed Powertronic's fully automatic planetary transmission, with a lockup function, which provides accurate and smooth gear shifting for productive operation.
John Deereâs wheel loader has a Hybrid-electric drive that smoothly and efficiently recaptures energy to slow the loader when the operator lets off the accelerator. This lessens the load on the engine and reduces fuel consumption. For OEM applications ranging from variable speed power generation to fully electric vehicle transmissions, their modular electric drivetrain component designs offer power generation and traction drive solutions up to 200 kW per unit.
Hollandâsndâs hydraulic Powershuttle ensures silky smooth direction changes which are perfect for precision loader work. They have ergonomically plaleversever that can be operated while holding the steering wheel for even greater safeproductivity-enhancingcfeaturesture will reduce fatigue and improve safetyKomatsuuâs unveilicenseic mechanical transmission in their wheel loader, it doesnât have a torque converter. The Transmission combines Komatsuâs hydrostatic transmission technology with that of a planetary transmission and uses a new travel speed control dial to allow operators to set speed.
SL No | Transmission Systems | OEM |
1 | Hydrostatic | Caterpillar, JCB, John Deere, Hitachi, Komatsu, Volvo |
2 | Powershift | Caterpillar, Terex, JCB, John Deere, Hitachi, Komatsu |
3 | Synchromesh | Caterpillar, JCB |
4 | Auto shift | Caterpillar, Terex, JCB, John Deere, Hitachi, Komatsu, Volvo |
SL No | Transmission Systems | OEM |
1 | Hydrostatic | Volvo, JCB, New Holland, Liebherr |
2 | Powershift | JCB, New Holland, Case Construction, Liebherr |
3 | Synchromesh | Case Construction |
4 | Auto shift | Volvo, Liebherr, Wirtgen Group |
SL No | Transmission Systems | OEM |
1 | Hydrostatic | JCB |
2 | Powershift | JCB, Mahindra, ACE, Hitachi, BEML |
3 | Synchromesh | JCB, Komatsu, L&T, Mahindra, Escorts, ACE, Tata Hitachi |
4 | Auto shift | JCB, Komatsu, L&T, Escorts, Hyundai, ACE, Tata Hitachi |
Sl no | Topic |
1 | Market Segmentation |
2 | Scope of the report |
3 | Abbreviations |
4 | Research Methodology |
5 | Executive Summary |
6 | Introduction |
7 | Insights from Industry stakeholders |
8 | Cost breakdown of Product by sub-components and average profit margin |
9 | Disruptive Innovation in the Industry |
10 | Technology Trends in the Industry |
11 | Consumer trends in the industry |
12 | Recent Production Milestones |
13 | Component Manufacturing in the US, EU, and China |
14 | Market Segmentation, Dynamics, and Forecast by Geography, 2024-2030 |
15 | Market Segmentation, Dynamics, and Forecast by Product Type, 2024-2030 |
16 | Market Segmentation, Dynamics, and Forecast by Application, 2024-2030 |
17 | Market Segmentation, Dynamics, and Forecast by End-use, 2024-2030 |
18 | Product installation rate by OEM, 2023 |
19 | Incline/Decline in Average B-2-B selling price in the past 5 years |
20 | Competition from substitute products |
21 | Gross margin and average profitability of suppliers |
22 | New product development in the past 12 months |
23 | M&A in the past 12 months |
24 | Growth strategy of leading players |
25 | Market share of vendors, 2023 |
26 | Company Profiles |
27 | Unmet needs and opportunities for new suppliers |
28 | Conclusion |
29 | Appendix |