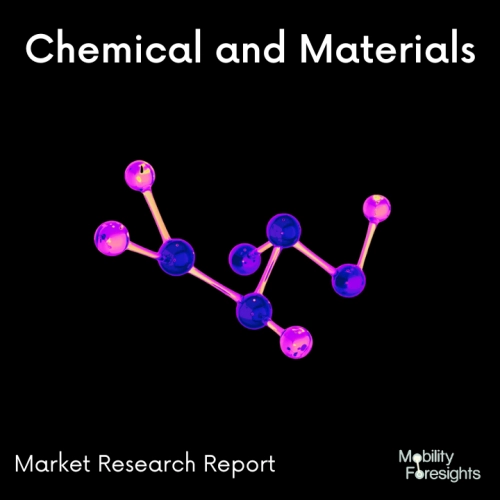
- Get in Touch with Us
Last Updated: Apr 25, 2025 | Study Period: 2024-2030
Ceramic fiber is an inorganic fiber composed of refractory ceramic fibers. It is produced from several raw materials including aluminum oxide, aluminum silicate, silicon carbide, and zirconium oxide. It is used for a variety of high temperature applications including high temperature insulation, refractory linings, and rigidizing materials.
The ceramic fiber is formed into wool, loose bulk, or board form, and is available in several densities and thicknesses for its variety of uses.Ceramic fiber insulation is typically used in many industrial applications such as furnaces and kilns, as well as automotive and electrical systems.
It is able to withstand very high temperatures without thermal shock, providing superior heat insulation. The fibers form a blanket or covering between the heated and cooler areas, creating an insulation barrier. The ceramic insulation also has a high resistance to thermal conductivity, meaning that heat will be transferred slowly from hot areas to cooler ones. This helps reduce energy costs.
Ceramic fiber is a very good choice for industrial and commercial applications due to its lightweight and easy installation. It can be cut to size and shape for exact application needs, which helps reduce costs.
It also has good thermal stability, which allows it to be used in a variety of applications with different heat levels. Ceramic fiber insulation is often used as a replacement for asbestos and other materials when insulation is needed.
Ceramic fiber is safe, non-combustible, and highly durable. It also doesnât contain harmful materials, so it's safe to use in most environments. The fibers can be used for both indoor and outdoor applications, making it a versatile and cost-effective insulation option. Ceramic fiber will remain stable even in extreme temperatures, and it is resistant to corrosion and chemical attack.
The Global continuous ceramic fiber market accounted for $XX Billion in 2022 and is anticipated to reach $XX Billion by 2030, registering a CAGR of XX% from 2024 to 2030.
RATH is developing continuous oxide ceramic fibers to provide composite manufacturers with alumina and mullite fiber solutions that satisfy the strictest mechanical requirements for tensile strength and modulus and maintain their strength in corrosive environments and extremely high temperatures. RATH is working to increase its capacity to manufacture more continuous fibers in greater quantities. Continuous oxide ceramic fibers are produced through some steps. Among them are thermal, spinning, and chemical processes.
They all work together to produce the best oxide ceramic fibers within extremely constrained processing windows. Using a similarly complex process, RATH is effectively manufacturing polycrystalline oxide ceramic staple fibers (Altra). The steady flow of fibers is essential to the advancement of O-CMC development.
High-quality continuous oxide ceramic fibers from multiple international sources will allow O-CMC manufacturers to increase their investment in this technology and offer solutions for a range of industries, including the chemical and aerospace industries. An oxide ceramic fiber with a higher creep resistance than those on the market now, resulting in a higher application temperature, would be another significant innovation.
Saint-Gobain is getting ready to start producing continuous ceramic fibers on an industrial scale in collaboration with a prestigious German institute. Ceramic materials have the potential to be extremely important in the ecological transition by providing new applications. They are the subject of high expectations even though they are not precisely a household name. It is possible to create multifunctional ceramic materials with ceramic oxide fibers.
These materials are incredibly light, yet possess a high degree of thermo-mechanical resistance as well as other qualities like corrosion resistance, electrical and thermal insulation, and more thanks to the fiber and matrix combination. We refer to these substances as Ceramic Matrix Composites (CMC). They are meant for use in applications where very strict thermo-mechanical limitations apply, such as high-efficiency gas turbines in industrial furnaces, aeronautics, space objects, or advanced technologies.
Sl no | Topic |
1 | Market Segmentation |
2 | Scope of the report |
3 | Abbreviations |
4 | Research Methodology |
5 | Executive Summary |
6 | Introduction |
7 | Insights from Industry stakeholders |
8 | Cost breakdown of Product by sub-components and average profit margin |
9 | Disruptive innovation in the Industry |
10 | Technology trends in the Industry |
11 | Consumer trends in the industry |
12 | Recent Production Milestones |
13 | Component Manufacturing in US, EU and China |
14 | COVID-19 impact on overall market |
15 | COVID-19 impact on Production of components |
16 | COVID-19 impact on Point of sale |
17 | Market Segmentation, Dynamics and Forecast by Geography, 2024-2030 |
18 | Market Segmentation, Dynamics and Forecast by Product Type, 2024-2030 |
19 | Market Segmentation, Dynamics and Forecast by Application, 2024-2030 |
20 | Market Segmentation, Dynamics and Forecast by End use, 2024-2030 |
21 | Product installation rate by OEM, 2023 |
22 | Incline/Decline in Average B-2-B selling price in past 5 years |
23 | Competition from substitute products |
24 | Gross margin and average profitability of suppliers |
25 | New product development in past 12 months |
26 | M&A in past 12 months |
27 | Growth strategy of leading players |
28 | Market share of vendors, 2023 |
29 | Company Profiles |
30 | Unmet needs and opportunity for new suppliers |
31 | Conclusion |
32 | Appendix |