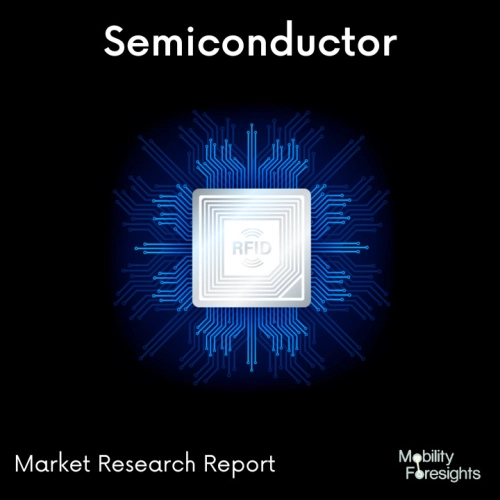
- Get in Touch with Us
Last Updated: Apr 25, 2025 | Study Period:
Determining the angles, radii, distances, and coordination as well as computer-controlled nominal-actual comparison with measured or CAD-based profile data are the main components of contour measurement.
For contour measurement, reputable manufacturers offer specialized equipment. It not only has an advantage and exceptional measurement capability when measuring the roughness of the inclined surface and arc, but also when measuring the surface As a result, the inspection procedure takes less time.
The main drawback is that because CMMs are situated remote from the manufacturing machinery, it also results in the loss of time spent on the transportation of components for inspection. Roughness of the part in its absolute position.
When tracing map coordinates, a CMM functions much like your finger; the machine's coordinate system is made up of its three axes. The CMM employs a probe rather than a finger to measure points on a workpiece.
The coordinate system of the machine makes each point on the workpiece distinct.Automobile, machine tool, electronics, space, and many other major industries use contour measurement equipment. The testing and inspection of test instruments, gauges, and tools is ideally suited for these machines.
The ambient thermal environment in which it functions determines how accurate it is. The scales, machine structure, and objects being measured expand, contract, and occasionally distort nonlinearly in response to temperature changes.
CMMs are used to check parts and components for end users in the shipbuilding, aerospace, and automotive industries, among other sectors.
The Global Contour Measuring Machine market accounted for $XX Billion in 2023 and is anticipated to reach $XX Billion by 2030, registering a CAGR of XX% from 2024 to 2030.
By developing SURFCOM CREST, ZEISS is establishing new benchmarks for accuracy and speed. With a 42,000,000:1 ratio between measurement range and resolution, the equipment measures surface parameters and contours in a single measuring cycle.
This makes it possible for SURFCOM CREST to measure even the smallest surface irregularities and contours across a very wide range in just one measuring run. With a laser interferometer as its measuring mechanism, SURFCOM CREST operates in the Z axis and is therefore incredibly accurate.
In comparison to measuring equipment with conventional spindle drives, the measuring station has a linear drive, making it substantially faster and less vibrational. Greater versatility with sloping workpieces is also made possible by the swivelling linear X tracing driver.
Sl no | Topic |
1 | Market Segmentation |
2 | Scope of the report |
3 | Abbreviations |
4 | Research Methodology |
5 | Executive Summary |
6 | Introduction |
7 | Insights from Industry stakeholders |
8 | Cost breakdown of Product by sub-components and average profit margin |
9 | Disruptive innovation in the Industry |
10 | Technology trends in the Industry |
11 | Consumer trends in the industry |
12 | Recent Production Milestones |
13 | Component Manufacturing in US, EU and China |
14 | COVID-19 impact on overall market |
15 | COVID-19 impact on Production of components |
16 | COVID-19 impact on Point of sale |
17 | Market Segmentation, Dynamics and Forecast by Geography, 2024-2030 |
18 | Market Segmentation, Dynamics and Forecast by Product Type, 2024-2030 |
19 | Market Segmentation, Dynamics and Forecast by Application, 2024-2030 |
20 | Market Segmentation, Dynamics and Forecast by End use, 2024-2030 |
21 | Product installation rate by OEM, 2023 |
22 | Incline/Decline in Average B-2-B selling price in past 5 years |
23 | Competition from substitute products |
24 | Gross margin and average profitability of suppliers |
25 | New product development in past 12 months |
26 | M&A in past 12 months |
27 | Growth strategy of leading players |
28 | Market share of vendors, 2023 |
29 | Company Profiles |
30 | Unmet needs and opportunity for new suppliers |
31 | Conclusion |
32 | Appendix |