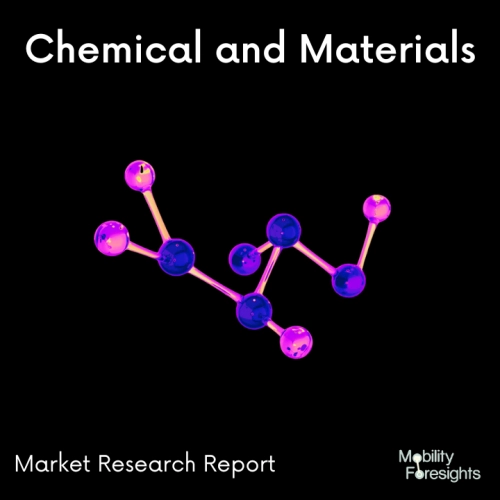
- Get in Touch with Us
Last Updated: Apr 25, 2025 | Study Period: 2024-2030
Cooling Water Chemicals are specifically processed for the purification of lake water, river water and sea water by removing salt and other unwanted substances from it. These chemicals are formulated as per the industrial quality norms by utilizing the exact quantity of components which have precise pH value. Sodium hypochlorite and sodium bromide solutions are frequently dosed together to create bromine-based oxidising biocides for cooling water treatment.
Values in cooling towers are kept in the 650â750 mV range, which is thought to be ideal for limiting corrosion and regulating microbial growth. The ideal ORP range, however, may differ based on elements including water chemistry, temperature, and cooling water system type.
The required TDS should be between 1000 and 1200 ppm, and the desired pH should be between 6.5 and 7.5. Cooling water quality is a highly significant characteristic. To prevent the circulating water's TDS content from increasing and fouling the equipment more frequently, blowdown is necessary.
The Global Cooling-water Treatment Chemicals market accounted for $XX Billion in 2023 and is anticipated to reach $XX Billion by 2030, registering a CAGR of XX% from 2024 to 2030.
Corte Releases New Molybdate-Free Version of Revolutionary Cooling Water Treatment. By offering efficient, simple-to-use treatments to stop corrosion during boiler, cooling tower, and closed loop system construction, Corte Corporation has revolutionized the water treatment business.
Water treatment specialists have fewer options due to restrictions on the use and disposal of some chemicals, such as molybdate, but Corte has risen to the challenge by creating a molybdate-free variant of Cooling Loop Gator, a ground-breaking corrosion inhibitor to protect idle cooling loop systems.
For cooling water systems during seasonal, temporary, or protracted layup, Cooling Loop Gator MF provides quick, safe, and efficient corrosion prevention. This is a crucial moment since idle equipment is more susceptible to corrosion, which might reduce asset life and make starting challenging.
While the norm in the industry has been to simply turn off a system and drain the water, this leaves the internals of the cooling system open to a problem that might be easily avoided by the straightforward use of Cooling Loop Gator.
Cooling Loop Gator MF is non-irritating, non-hazardous, and safe to use. Nitrites, phosphates, and chromates are absent from it. To get a good protective layer before shutdown, workers can drop these water-soluble bags straight into the cooling water and circulate the water for around 12 to 24 hours.
The Vapor phase Corrosion Inhibitors adsorb on all metal surfaces once the bag and powder have disintegrated, reaching recessed regions and inner cavities to produce a sturdy molecular coating that shields metals above and below the surface of the water.
The water can either be flushed after application (flushing application) or kept in (wet layup). To retain the protective vapors inside the system, all valves should be covered, closed, and turned off.
1 | Market Segmentation |
2 | Scope of the report |
3 | Abbreviations |
4 | Research Methodology |
5 | Executive Summary |
6 | Introduction |
7 | Insights from Industry stakeholders |
8 | Cost breakdown of Product by sub-components and average profit margin |
9 | Disruptive innovation in the Industry |
10 | Technology trends in the Industry |
11 | Consumer trends in the industry |
12 | Recent Production Milestones |
13 | Component Manufacturing in US, EU and China |
14 | COVID-19 impact on overall market |
15 | COVID-19 impact on Production of components |
16 | COVID-19 impact on Point of sale |
17 | Market Segmentation, Dynamics and Forecast by Geography, 2024-2030 |
18 | Market Segmentation, Dynamics and Forecast by Product Type, 2024-2030 |
19 | Market Segmentation, Dynamics and Forecast by Application, 2024-2030 |
20 | Market Segmentation, Dynamics and Forecast by End use, 2024-2030 |
21 | Product installation rate by OEM, 2023 |
22 | Incline/Decline in Average B-2-B selling price in past 5 years |
23 | Competition from substitute products |
24 | Gross margin and average profitability of suppliers |
25 | New product development in past 12 months |
26 | M&A in past 12 months |
27 | Growth strategy of leading players |
28 | Market share of vendors, 2023 |
29 | Company Profiles |
30 | Unmet needs and opportunity for new suppliers |
31 | Conclusion |
32 | Appendix |