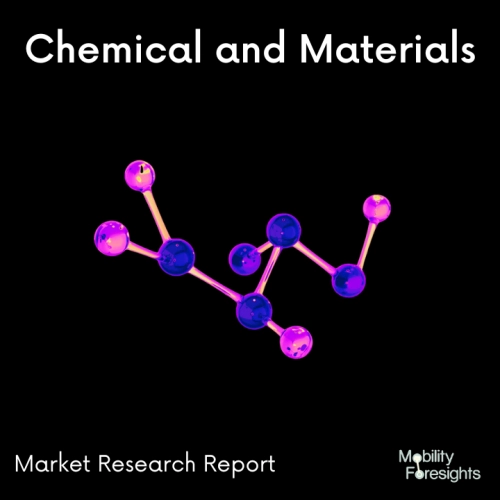
- Get in Touch with Us
Last Updated: Apr 25, 2025 | Study Period: 2024-2030
Copper tubing is commonly utilized in heating systems as well as as a refrigerant line in HVAC systems.
In hot and cold water applications, copper tubing is gradually being replaced with PEX tubing.
Copper tubing is classified into two types: soft copper and stiff copper.
A flare connection, compression connection, pushed connection, or solder is used to link copper tubing.
Copper has a good corrosion resistance but is getting highly expensive.
Copper tubing that is soft (or ductile) may be readily bent to avoid obstructions in its route.
While the work hardening of the drawing process used to size the tubing makes the copper hard or inflexible, it is carefully annealed to soften it again; as a result, it is more expensive to create.
It can be attached using any of the three rigid copper joining methods, and it is the only form of copper tubing that can be used for flare connections.
Soft copper is the most often used refrigerant line material in split-system air conditioners and heat pumps.
For water lines, rigid copper is a preferred material.
Pipe is the common term for rigid or hard copper tubing.
The nominal pipe size, or inner diameter, of copper piping is referred to.
A solder/sweat, roll grooved, compression, or crimped/pressed connection is used to attach it.
Rigid copper cannot be bent owing to the work hardening of the drawing process and must be used with elbow fittings to travel around corners or over obstructions.
When hard copper is heated and allowed to cool in a process known as annealing, it softens and may be bent/formed without cracking.
Solder fittings are smooth and easy to install on the end of a tube piece.
The solder is then melted into the connection after the junction is heated using a torch.
When the solder cools, it makes a very strong connection that may endure decades.
For water supply lines in modern buildings, solder-connected rigid copper is the most prevalent material.
Solder enables significantly faster and less expensive joinery than compression or flare fittings in instances where many connections must be made simultaneously (such as plumbing in a new building).
The phrase sweating is occasionally used to describe the soldering process.
The substance used to fill the joints has a melting point.
Brazing is a metal-joining method that involves melting and flowing a filler metal into the joint, with the filler metal having a lower melting temperature than the neighboring metal.
Brazing varies from welding in that the work components are not melted, and it differs from soldering in that it uses greater temperatures for a comparable procedure while also needing much more precisely fitting parts than soldering.
Capillary motion causes the filler metal to seep into the space between close-fitting pieces.
The filler metal is heated to just over its melting (liquidus) temperature while being shielded by an appropriate environment, generally a flux. It then flows over the base metal (in this case, copper).
Compression fittings employ a soft metal or thermoplastic ring that a compression nut squeezes onto the pipe and into the fitting.
The soft metal produces a seal by conforming to the surface of the tube and fitting.
Compression connections do not often have the same longevity as sweat connections, but they are useful in many circumstances since they are simple to establish using common equipment.
Compression connections have the drawback of taking longer to create than sweat and often requiring re-tightening over time to control leakage.
Flare connections need spreading the end of a tube piece outward in a bell form with a flare tool.
Flaring is only possible with soft copper. This is then compressed by a flare nut.
Flare connections are a labor-intensive way of creating connections, but they have shown to be fairly dependable over many years.
Crimped connections, also known as pressed fittings, are unique copper fittings that are permanently linked to rigid copper tubing using a crimper, either manually or electrically.
The fittings, which are pre-filled with sealant, glide over the tube to be joined.
Thousands of pounds of pressure per square inch are applied to the fitting to distort it and compress the sealant against the inner copper tube, resulting in a water-tight seal.
The benefits of this approach include the fact that it should last as long as the tube, that it takes less time to finish than other ways, that it is cleaner in both appearance and the materials used to construct the connection, and that there are no open joints.
The downsides are that the fittings used are more difficult to locate and substantially more expensive than sweat-type fittings.
Push-to-connect fittings, also known as push-to-lock or just push, are easily placed onto the end of a tube and held in place by teeth inside the fitting.
Other than equipment to cut and deburr the tube, no wrenches or other special tools are required for installation.
Unlike soldered fittings, they may be put on wet tubes at the time of installation.
The Global Copper Pipes And Tubes Market accounted for $XX Billion in 2022 and is anticipated to reach $XX Billion by 2030, registering a CAGR of XX% from 2024 to 2030.
The American Society for Testing and Materials Standards are followed by these copper pipes.
This indicates that it is both globally viable and fulfilling its responsibilities.
JIS H3300 C1220T copper tubes and ASTM B88 copper tubes are the two varieties of copper tubes available.
Copper pipes are used to move liquids.
It is extremely good and widely used in piping because of three characteristics: it is light, sturdy, and corrosion resistant.
It is used in various types of buildings, from little dwellings to massive industrial structures.
Copper pipe is commonly used in the construction sector for water supply lines and refrigerant lines in heating, ventilation, and air conditioning.
While this can refer to alternating current, many people are unaware that this copper tube system is what keeps refrigerators and freezers running.
While copper tubes are most commonly used in the residential sector to transport potable water in homes and offices, refrigeration businesses, firefighting systems and medical and residential gas providers are also catching up.
Sl no | Topic |
1 | Market Segmentation |
2 | Scope of the report |
3 | Abbreviations |
4 | Research Methodology |
5 | Executive Summary |
6 | Introduction |
7 | Insights from Industry stakeholders |
8 | Cost breakdown of Product by sub-components and average profit margin |
9 | Disruptive innovation in the Industry |
10 | Technology trends in the Industry |
11 | Consumer trends in the industry |
12 | Recent Production Milestones |
13 | Component Manufacturing in US, EU and China |
14 | COVID-19 impact on overall market |
15 | COVID-19 impact on Production of components |
16 | COVID-19 impact on Point of sale |
17 | Market Segmentation, Dynamics and Forecast by Geography, 2023-2030 |
18 | Market Segmentation, Dynamics and Forecast by Product Type, 2023-2030 |
19 | Market Segmentation, Dynamics and Forecast by Application, 2023-2030 |
20 | Market Segmentation, Dynamics and Forecast by End use, 2023-2030 |
21 | Product installation rate by OEM, 2023 |
22 | Incline/Decline in Average B-2-B selling price in past 5 years |
23 | Competition from substitute products |
24 | Gross margin and average profitability of suppliers |
25 | New product development in past 12 months |
26 | M&A in past 12 months |
27 | Growth strategy of leading players |
28 | Market share of vendors, 2023 |
29 | Company Profiles |
30 | Unmet needs and opportunity for new suppliers |
31 | Conclusion |
32 | Appendix |