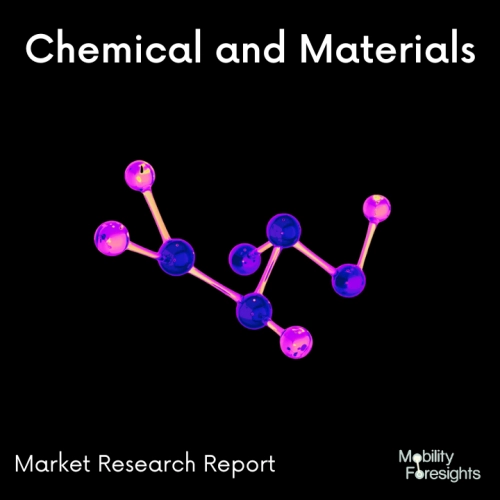
- Get in Touch with Us
Last Updated: Apr 25, 2025 | Study Period: 2024-2030
Copper etching is a chemical etching procedure used to produce intricate metal components from copper or copper alloys. The metal is dissolved using corrosive chemicals until just the required form is left.
Etchers have long known that a solution of ferric chloride crystals makes a very controlled etchant with the most precise bite for copper plates.
A 1:1 mixture of ferric chloride and water produces a hydrochloric acid solution. The acid that is most frequently used to etch copper is hydrochloric acid.
The Global Copper seed layer etching chemicals market accounted for $XX Billion in 2022 and is anticipated to reach $XX Billion by 2030, registering a CAGR of XX% from 2024 to 2030.
Recent Advances in Barrier Layer of Cu Interconnects.Cu cannot diffuse into the dielectric layer at high temperatures, thus the barrier layer in Cu technology is crucial; as a result, it must be highly stable and have excellent adhesion to both Cu and the dielectric layer.
The inter-layer made of tantalum/tantalum nitride (Ta/TaN) has frequently been employed to place between the Cu and the dielectric layer.
However, conventional materials and technological procedures are being put to the test in order to meet the requirement for ongoing downscaling of the Cu technology node. Due to Ta/TaN's high resistivity, direct electrochemical deposition of Cu on top of Ta/TaN is not practical.
Defect-free fill of current sub-20 or even sub-10 nm Cu technology nodes is severely hampered by the non-uniformity of the Cu seed layer, which must be pre-deposited by physical vapour deposition (PVD) or chemical vapour deposition (CVD).
For the successful super-fill of trenches at the nanoscale scale, new Cu diffusion barrier materials with ultra-thin size, high resistivity, and stability are required. Including metals, metal alloys, self-assembled molecular layers (SAMs), two-dimensional (2D) materials, and high-entropy alloys (HEAs), briefly examine current developments in the creation of Cu diffusion-proof materials .
Sl no | Topic |
1 | Market Segmentation |
2 | Scope of the report |
3 | Abbreviations |
4 | Research Methodology |
5 | Executive Summary |
6 | Introduction |
7 | Insights from Industry stakeholders |
8 | Cost breakdown of Product by sub-components and average profit margin |
9 | Disruptive innovation in the Industry |
10 | Technology trends in the Industry |
11 | Consumer trends in the industry |
12 | Recent Production Milestones |
13 | Component Manufacturing in US, EU and China |
14 | COVID-19 impact on overall market |
15 | COVID-19 impact on Production of components |
16 | COVID-19 impact on Point of sale |
17 | Market Segmentation, Dynamics and Forecast by Geography, 2024-2030 |
18 | Market Segmentation, Dynamics and Forecast by Product Type, 2024-2030 |
19 | Market Segmentation, Dynamics and Forecast by Application, 2024-2030 |
20 | Market Segmentation, Dynamics and Forecast by End use, 2024-2030 |
21 | Product installation rate by OEM, 2023 |
22 | Incline/Decline in Average B-2-B selling price in past 5 years |
23 | Competition from substitute products |
24 | Gross margin and average profitability of suppliers |
25 | New product development in past 12 months |
26 | M&A in past 12 months |
27 | Growth strategy of leading players |
28 | Market share of vendors, 2023 |
29 | Company Profiles |
30 | Unmet needs and opportunity for new suppliers |
31 | Conclusion |
32 | Appendix |