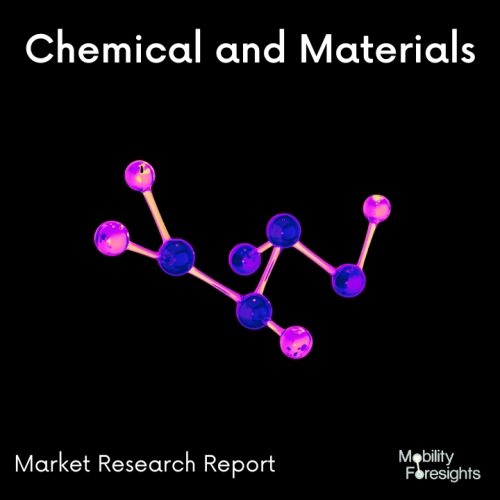
- Get in Touch with Us
Last Updated: Apr 25, 2025 | Study Period: 2024-2030
In general, Copper Zinc Tin Alloy are more robust than copper-silver, copper-iron, and electrolytic tough pitch copper alloys, but less robust than copper-magnesium and copper-nickel-silicon alloys.
As an illustration, Cu-ETP has a tensile strength of about 350 N/mm2, but Copper-Tin Wire may have >620 N/mm2. The extra benefit of a cross-section decrease of up to three gauge sizes, for instance from 0.35 mm2 to 0.13 mm2, is made possible by the higher tensile strength.
The amount of heating time needed to reduce the hardness of a cold-worked sample to half that of a fully annealed value is known as the half-softening time, which is measured in minutes to determine softening resistance. The following table compares copper-silver with copper-tin, and it is obvious from the comparison that copper-tin is superior to copper-silver.
The Global Copper Zinc Tin Alloy Market accounted for $XX Billion in 2022 and is anticipated to reach $XX Billion by 2030, registering a CAGR of XX% from 2024 to 2030.
Since many years ago, Copper Zinc Tin Alloy have been plated and are frequently employed for a wide range of purposes. The two most frequent procedures are the plating of Copper Zinc Tin Alloy deposits for electronic components and the plating of brass for ornamental purposes.
High performance and customized electrolytic deposited layers are now more in demand than ever. For instance, more stringent technical specifications for corrosion resistance, deposit hardness, and wear resistance are now required for ornamental layers and electronics applications.
Single-metal deposits have rather stable characteristics that can only be marginally improved. Improved brightener and leveling additives that increase metallurgical qualities including ductility, elongation, and overall process stability are the main focus of process enhancement. by concurrently depositing two or more metals to create an alloy.
Tri-metal is a great alternative to nickel and silver for high frequency RF connector and other electronic applications due to its aesthetic and chemical characteristics, which include being extremely resistant to corrosion and wear, solderable, non-magnetic, smooth, and non-porous.
Tri-metal plating's brilliant white finish can be applied as a topcoat or an undercoat for products with palladium, palladium-nickel, silver, or gold finishes.
A non-toxic, non-magnetic layer that is incredibly corrosion resistant is produced via tri-metal plating. This deposit and application for metal polishing has a low coefficient of friction and porosity. Tri-metal plating without lead is ideal for solder applications.
Sl no | Topic |
1 | Market Segmentation |
2 | Scope of the report |
3 | Abbreviations |
4 | Research Methodology |
5 | Executive Summary |
6 | Introduction |
7 | Insights from Industry stakeholders |
8 | Cost breakdown of Product by sub-components and average profit margin |
9 | Disruptive innovation in the Industry |
10 | Technology trends in the Industry |
11 | Consumer trends in the industry |
12 | Recent Production Milestones |
13 | Component Manufacturing in US, EU and China |
14 | COVID-19 impact on overall market |
15 | COVID-19 impact on Production of components |
16 | COVID-19 impact on Point of sale |
17 | Market Segmentation, Dynamics and Forecast by Geography, 2024-2030 |
18 | Market Segmentation, Dynamics and Forecast by Product Type, 2024-2030 |
19 | Market Segmentation, Dynamics and Forecast by Application, 2024-2030 |
20 | Market Segmentation, Dynamics and Forecast by End use, 2024-2030 |
21 | Product installation rate by OEM, 2023 |
22 | Incline/Decline in Average B-2-B selling price in past 5 years |
23 | Competition from substitute products |
24 | Gross margin and average profitability of suppliers |
25 | New product development in past 12 months |
26 | M&A in past 12 months |
27 | Growth strategy of leading players |
28 | Market share of vendors, 2023 |
29 | Company Profiles |
30 | Unmet needs and opportunity for new suppliers |
31 | Conclusion |
32 | Appendix |