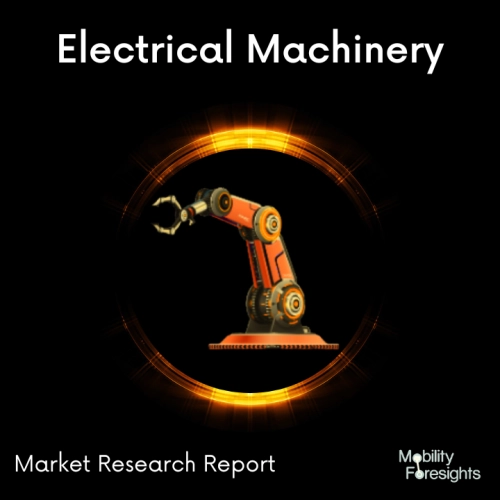
- Get in Touch with Us
Last Updated: Apr 25, 2025 | Study Period: 2024-2030
INTRODUCTION
A corrosion test chamber is a custom-built laboratory testing chamber designed to simulate the conditions that corrosion-sensitive components will be exposed to during real-world use. By using these chambers, manufacturers and testing labs can better predict the lifespan of their parts.
Corrosion test chambers are designed to create a range of environmental conditions that can cause the accelerated breakdown of materials. These conditions can include high temperatures, humidity, salt spray, and UV light, depending on the application.
By exposing the components to these conditions, the effects of oxidation, corrosion, and other degradation can be studied. This allows manufacturers to identify weak spots and improve the longevity of their components. It also allows them to test for compatibility with different materials and coatings, which can be used to protect components from the elements.
Corrosion test chambers also allow for the testing of components in a controlled environment, which can give more accurate results than testing in the field. This can be especially important when testing components that are sensitive to changes in temperature and humidity, as these conditions can affect the performance of the components.
Overall, corrosion test chambers provide a valuable tool for manufacturers and testing labs. They allow for the study of the effects of corrosion on components, allowing them to make informed decisions about their products and to test for compatibility with different materials and coatings. This helps to ensure the longevity of components and the safety of the end user.
CORROSION TEST CHAMBER MARKET SIZE AND FORECAST
The Global Corrosion test chamber market accounted for $XX Billion in 2022 and is anticipated to reach $XX Billion by 2030, registering a CAGR of XX% from 2024 to 2030.
The new Q-FOG CRH corrosion test chamber, which has the ability to function as a rapid ramp heater, has been launched by Q-Lab Corporation, a leading manufacturer of corrosion test equipment worldwide. Conventional salt spray, Prohesion, and the majority of cyclic automotive testing can be carried out in Q-FOG CRH cyclic corrosion chambers.
They have exact control over ramp durations and a fully adjustable relative humidity level. Currently equipped with the new Rapid Ramp Heater feature, the Q-FOG CRH tester can fulfil specific test conditions requiring very quick temperature ramping.
Including JASO M609, CCT-I, and CCT-IV tests, it can pass them all from reputable worldwide standards organisations and OEMs, even when the chamber is fully loaded. Enhanced control over corrosion test process variables is also made possible by the new Rapid Ramp Heater.
The Salt Spray Chamber, an advanced corrosion testing technology, was introduced by PACORR. In the coating, painting, and plating industries, corrosion testing is a long-standing practice.
Coating producers and consumers who need to select an effective coating product have been conducting tests in their community to determine whether the coating that will be applied to the product is effective or meets the required criteria.
But many people choose not to invest in testing equipment because of its high cost, instead depending on their intuition, perception, or sense of touch. Even tech-inclined product engineers have a limited comprehension of the features and ultimately buy any device that meets their requirements. To guarantee general quality, this procedure needs to be modified.
With time, corrosion testing equipment has changed. It is now much more than just a chamber that simulates the conditions that lead to corrosion reactions. Reputable for its research and capacity to introduce the newest technology to the market, PACORR is one of the top brands in the quality testing instrument industry. The business has introduced its most recent model, a luxurious salt spray chamber composed of premium fibre-reinforced plastic.
In order to prove the efficacy of the FRP Material, PACORR has invested in cutting edge technology, a highly qualified team of product engineers, and extensive research to bring such a material to market.
Sl no | Topic |
1 | Market Segmentation |
2 | Scope of the report |
3 | Abbreviations |
4 | Research Methodology |
5 | Executive Summary |
6 | Introduction |
7 | Insights from Industry stakeholders |
8 | Cost breakdown of Product by sub-components and average profit margin |
9 | Disruptive innovation in the Industry |
10 | Technology trends in the Industry |
11 | Consumer trends in the industry |
12 | Recent Production Milestones |
13 | Component Manufacturing in US, EU and China |
14 | COVID-19 impact on overall market |
15 | COVID-19 impact on Production of components |
16 | COVID-19 impact on Point of sale |
17 | Market Segmentation, Dynamics and Forecast by Geography, 2024-2030 |
18 | Market Segmentation, Dynamics and Forecast by Product Type, 2024-2030 |
19 | Market Segmentation, Dynamics and Forecast by Application, 2024-2030 |
20 | Market Segmentation, Dynamics and Forecast by End use, 2024-2030 |
21 | Product installation rate by OEM, 2023 |
22 | Incline/Decline in Average B-2-B selling price in past 5 years |
23 | Competition from substitute products |
24 | Gross margin and average profitability of suppliers |
25 | New product development in past 12 months |
26 | M&A in past 12 months |
27 | Growth strategy of leading players |
28 | Market share of vendors, 2023 |
29 | Company Profiles |
30 | Unmet needs and opportunity for new suppliers |
31 | Conclusion |
32 | Appendix |