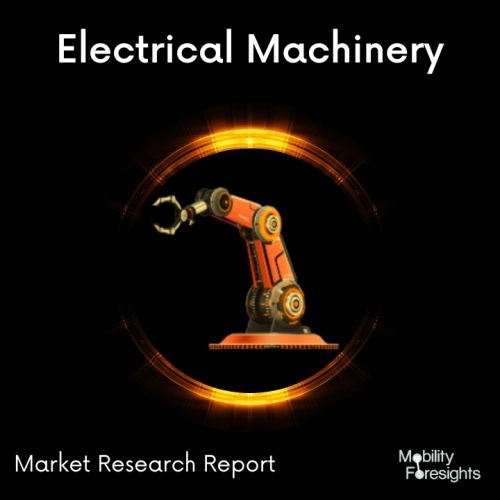
- Get in Touch with Us
Last Updated: Apr 26, 2025 | Study Period: 2024-2030
The crankshaft is made up of crankpins, crank webs, crank arms or cheek, balancing weight, and main journals. The connecting rods' big end is fastened to the crankshafts' crankpin. Half of the piston displacements are covered by the center-to-center distance between the crankpin and the crankshaft during a stroke.
Modern machining centers, where cranks can be made on lathes with milling attachments or on milling machines equipped with a fourth axis, have substantially improved the machining of crankpins. In these instances, the crankshaft blank is gently spun while a milling cutter follows the motion of the pin to generate the pins.
The Global Crankshaft Milling machine market accounted for $XX Billion in 2023 and is anticipated to reach $XX Billion by 2030, registering a CAGR of XX% from 2024 to 2030.
The crankshaft miller for engine machining was developed by Komatsu Machinery Corporation. As a very precise and productive piece of machinery, crankshafts have received great praise.
The Komatsu crankshaft miller secures the work and uses a rest to clamp the area close to the milling portion. This guarantees that the job will be highly supported rigidly. A large-diameter cutter bearing and Komatsu's distinctive swing arm arrangement further contribute to the high stiffness of the cutter support. As a result, even during intense cutting, high-precision machining is possible.
The prior model's configuration, which boasts exceptional reliability, is kept.The crankshaft miller, which produces the most noise in the line, is a milling machine for heavy cutting.
It is constantly urged that the noise level be reduced. This time, prior to the model modification, "Noise analysis by the Campbell diagram" and "Modal analysis" were carried out in the development process using a traditional machine. The Corporate Research Division supported this study with its assistance.
Simultaneously, optimization of the machine cover shapes was investigated. 3dB (A) was ultimately lowered. The achievement of cutting the noise energy in half is impressive.
The front shaft of the crankshaft has a recess through which the miller's chuck passes. To keep metal chips from getting inside this part while it is being machined, air is forced upon it. If this air blowing could be stopped, the amount of air used would be drastically reduced.
Sl no | Topic |
1 | Market Segmentation |
2 | Scope of the report |
3 | Abbreviations |
4 | Research Methodology |
5 | Executive Summary |
6 | Introduction |
7 | Insights from Industry stakeholders |
8 | Cost breakdown of Product by sub-components and average profit margin |
9 | Disruptive innovation in the Industry |
10 | Technology trends in the Industry |
11 | Consumer trends in the industry |
12 | Recent Production Milestones |
13 | Component Manufacturing in US, EU and China |
14 | COVID-19 impact on overall market |
15 | COVID-19 impact on Production of components |
16 | COVID-19 impact on Point of sale |
17 | Market Segmentation, Dynamics and Forecast by Geography, 2024-2030 |
18 | Market Segmentation, Dynamics and Forecast by Product Type, 2024-2030 |
19 | Market Segmentation, Dynamics and Forecast by Application, 2024-2030 |
20 | Market Segmentation, Dynamics and Forecast by End use, 2024-2030 |
21 | Product installation rate by OEM, 2023 |
22 | Incline/Decline in Average B-2-B selling price in past 5 years |
23 | Competition from substitute products |
24 | Gross margin and average profitability of suppliers |
25 | New product development in past 12 months |
26 | M&A in past 12 months |
27 | Growth strategy of leading players |
28 | Market share of vendors, 2023 |
29 | Company Profiles |
30 | Unmet needs and opportunity for new suppliers |
31 | Conclusion |
32 | Appendix |