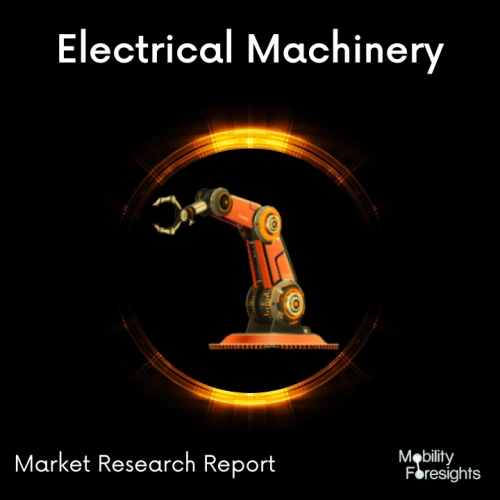
- Get in Touch with Us
Last Updated: Apr 25, 2025 | Study Period: 2024-2030
Crankshaft pin grinder that was designed locally, using an auto indexing fixture that was hydraulically clamped. By grinding every pin in a single configuration, the machine gives greater flexibility in the pin grinding operation for multi-cylinder crankshafts with variable indexing angles.
Without the use of a lay shaft, both heads are CNC-driven by Servo motors with extremely precise synchronization. Head indexing work is continuously clamped. High-production machine created for Journal Grinding application in the crankshaft industry.
The bed's unique design (Slant Table) gives it the industry's most sturdy structure to resist unbalanced dynamic weight and higher cutting forces needed for crankshafts.
The Global Crankshaft pin grinding machine Market accounted for $XX Billion in 2023 and is anticipated to reach $XX Billion by 2030, registering a CAGR of XX% from 2024 to 2030.
A specially designed grinding solution for crankshaft-type components has been developed by EMAG. The new PMD 2 machine has dual grinding heads that enable the simultaneous grinding of two pin or main bearings in a single setup utilizing two grinding wheels.
The equipment is intended for the machining of passenger automobile crankshafts. Up to 500 mm in length, minor components are covered by its capacity. They are completing the line of crankshaft grinders with this equipment by adding the ability to produce smaller parts.
They have not yet included a horizontal twin-head grinder for smaller crankshafts to our lineup of machines. The established "Series 2" from EMAG KOPP and NAXOS-UNION served as the foundation for the PMD 2.
With precision, outstanding efficiency, process integrity, and ease of use, these machines integrate cutting-edge grinding technology. This holds true for the PMD 2 as well, which produces crankshafts with the maximum level of precision using two CBN grinding wheels. In addition, two grinding wheels are used in the technology.
Depending on the component and machining needs, the customer has a variety of options available to them with the twin-tool technique. In order to speed up production, two pin bearings or main and pin bearings are produced simultaneously.
One example is the time needed to fabricate a four-cylinder crankshaft. In order to simultaneously mill adjacent pins and main bearings, the grinding wheels can, if necessary, be positioned very closely together.
Sl no | Topic |
1 | Market Segmentation |
2 | Scope of the report |
3 | Abbreviations |
4 | Research Methodology |
5 | Executive Summary |
6 | Introduction |
7 | Insights from Industry stakeholders |
8 | Cost breakdown of Product by sub-components and average profit margin |
9 | Disruptive innovation in the Industry |
10 | Technology trends in the Industry |
11 | Consumer trends in the industry |
12 | Recent Production Milestones |
13 | Component Manufacturing in US, EU and China |
14 | COVID-19 impact on overall market |
15 | COVID-19 impact on Production of components |
16 | COVID-19 impact on Point of sale |
17 | Market Segmentation, Dynamics and Forecast by Geography, 2024-2030 |
18 | Market Segmentation, Dynamics and Forecast by Product Type, 2024-2030 |
19 | Market Segmentation, Dynamics and Forecast by Application, 2024-2030 |
20 | Market Segmentation, Dynamics and Forecast by End use, 2024-2030 |
21 | Product installation rate by OEM, 2023 |
22 | Incline/Decline in Average B-2-B selling price in past 5 years |
23 | Competition from substitute products |
24 | Gross margin and average profitability of suppliers |
25 | New product development in past 12 months |
26 | M&A in past 12 months |
27 | Growth strategy of leading players |
28 | Market share of vendors, 2023 |
29 | Company Profiles |
30 | Unmet needs and opportunity for new suppliers |
31 | Conclusion |
32 | Appendix |