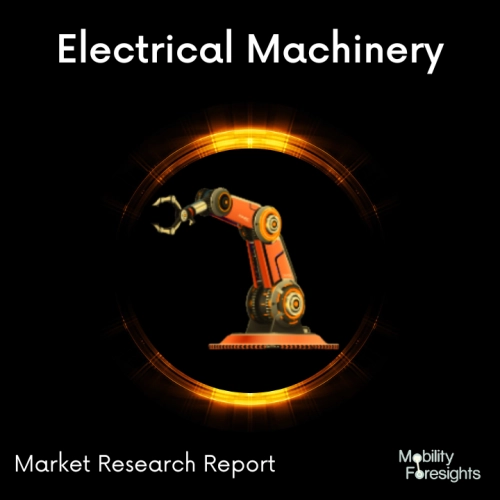
- Get in Touch with Us
Last Updated: Apr 25, 2025 | Study Period: 2024-2030
A specialized piece of equipment called a cryogenic grinder is used in the food processing sector to crush and grind materials at very low temperatures. With liquid nitrogen or other cryogenic gases, materials must be cooled down below their brittle point, which is typically approximately -196°C (-320°F).
The material is placed into the grinder after cooling, where it is ground into tiny pieces. Low temperatures limit heat buildup during grinding, which may otherwise result in the material melting, becoming too soft, or deforming.
Spices, plants, polymers, and medicines are just a few examples of heat-sensitive and soft materials that can be ground effectively using cryogenic grinding.
Cryogenic grinding has the ability to create smaller particle sizes than conventional methods of grinding, which is one of its advantages. Because of the low temperature, which prevents volatile substances from evaporating, it can also aid in the preservation of food goods' flavor and scent.
Cryogenic grinding can, however, be more expensive than conventional grinding techniques in terms of both equipment and running costs. However, some materials might not be appropriate for cryogenic grinding because of their characteristics, such as a high oil content that can result in grinder clogs.
Global cryogenic grinder market accounted for $XX Billion in 2023 and is anticipated to reach $XX Billion by 2030, registering a CAGR of XX% from 2024 to 2030.
Shri Krishna Pulverizes, one of the leaders in crushing and grinding plants, has introduced their brand-new, technologically sophisticated cryogenic grinding plants. This is a cutting-edge breakthrough in grinding processes.
The addition of liquid nitrogen to the system while grinding is one of the characteristics of cryogenic grinding. Grinding at low temperatures down to -196 degrees.
Minimal volatile oil loss. Ultimately, the flavor and aroma of spices and other items are preserved. Gives the material brittleness, which makes products that are hard to grind or even un grindable in conventional grinding become grindable and produce better results.
Because of the massive increase in production per kilowatt and the elimination of all grinding-related problems including non-grindability and choke, a cryogenic plant's initial cost and ongoing operating costs can be negotiated. The product's quality has been raised to an entirely new standard.
Applications a. Seasonings, sauces, and spices. Chemicals that are highly flammable or hygroscopic in nature. Food. Tire and rubber grinding. And there are countless others.
Sl no | Topic |
1 | Market Segmentation |
2 | Scope of the report |
3 | Abbreviations |
4 | Research Methodology |
5 | Executive Summary |
6 | Introduction |
7 | Insights from Industry stakeholders |
8 | Cost breakdown of Product by sub-components and average profit margin |
9 | Disruptive innovation in the Industry |
10 | Technology trends in the Industry |
11 | Consumer trends in the industry |
12 | Recent Production Milestones |
13 | Component Manufacturing in US, EU and China |
14 | COVID-19 impact on overall market |
15 | COVID-19 impact on Production of components |
16 | COVID-19 impact on Point of sale |
17 | Market Segmentation, Dynamics and Forecast by Geography, 2024-2030 |
18 | Market Segmentation, Dynamics and Forecast by Product Type, 2024-2030 |
19 | Market Segmentation, Dynamics and Forecast by Application, 2024-2030 |
20 | Market Segmentation, Dynamics and Forecast by End use, 2024-2030 |
21 | Product installation rate by OEM, 2023 |
22 | Incline/Decline in Average B-2-B selling price in past 5 years |
23 | Competition from substitute products |
24 | Gross margin and average profitability of suppliers |
25 | New product development in past 12 months |
26 | M&A in past 12 months |
27 | Growth strategy of leading players |
28 | Market share of vendors, 2023 |
29 | Company Profiles |
30 | Unmet needs and opportunity for new suppliers |
31 | Conclusion |
32 | Appendix |