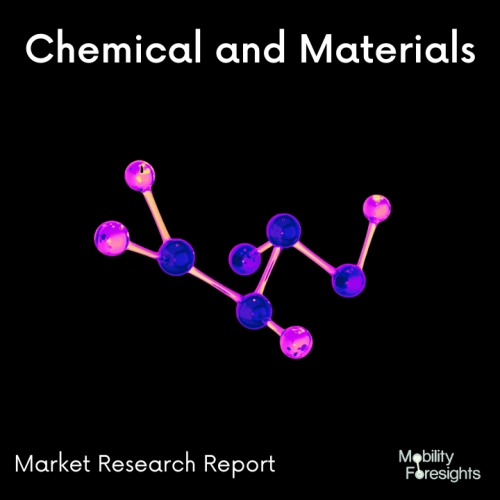
- Get in Touch with Us
Last Updated: Apr 25, 2025 | Study Period: 2023-2030
Injection molded plastic is used to make cuvettes. There will always be some variation, no matter how exact the mold tolerances are. During the production process, cuvettes are sorted to ensure that each package only contains cuvettes produced using the same mold, hence reducing variation from cuvette to cuvette.
To guarantee the lowest fluctuation in extinction coefficient, all cuvettes are produced using materials that are resistant to scratches and are organized by the number of manufacturing mold cavities.
The Global Cuvette Injection Moulding Machine market accounted for $XX Billion in 2022 and is anticipated to reach $XX Billion by 2030, registering a CAGR of XX% from 2023 to 2030.
The invention relates to a method of making a cuvette or receptacle for liquid or gaseous media for spectroscopic, qualitative, and/or quantitative analysis or measurement with a radiolabelled measuring range of measuring gap made of plastic by injection molding, wherein a multi-part injection mold, which inside the Contour of the cuvette or the receptacle having the opening and measuring gap is filled in an injection molding machine with the initially liquid plastic, is used to produce the cuvette.
These cuvettes, which can be made of plastic or quartz glass, come in a variety of sizes and shapes, especially when it comes to the layer thickness, which is another name for the thickness of the measuring gap. A plastic cuvette special training with two Pair opposed plane-parallel windows, for instance, is known from DE 198 26 470 A1 and can be used to achieve various layer thicknesses.
A jaw tool with an injection point 16 opposite the tip of the contour core is used to create this well-known injection-molded plastic cuvette, which forms the interior cavity and measurement gap.
The contour of the core is held by the support at its smallest dimension end, and the opening of the vessel or cuvette facing away from the end of the measuring gap is formed by the support is withdrawn from the contour core during the injection molding process, the support forming, together with the end of the measuring gap, according to the invention.
Sl no | Topic |
1 | Market Segmentation |
2 | Scope of the report |
3 | Abbreviations |
4 | Research Methodology |
5 | Executive Summary |
6 | Introduction |
7 | Insights from Industry stakeholders |
8 | Cost breakdown of Product by sub-components and average profit margin |
9 | Disruptive innovation in the Industry |
10 | Technology trends in the Industry |
11 | Consumer trends in the industry |
12 | Recent Production Milestones |
13 | Component Manufacturing in US, EU and China |
14 | COVID-19 impact on overall market |
15 | COVID-19 impact on Production of components |
16 | COVID-19 impact on Point of sale |
17 | Market Segmentation, Dynamics and Forecast by Geography, 2023-2030 |
18 | Market Segmentation, Dynamics and Forecast by Product Type, 2023-2030 |
19 | Market Segmentation, Dynamics and Forecast by Application, 2023-2030 |
20 | Market Segmentation, Dynamics and Forecast by End use, 2023-2030 |
21 | Product installation rate by OEM, 2023 |
22 | Incline/Decline in Average B-2-B selling price in past 5 years |
23 | Competition from substitute products |
24 | Gross margin and average profitability of suppliers |
25 | New product development in past 12 months |
26 | M&A in past 12 months |
27 | Growth strategy of leading players |
28 | Market share of vendors, 2023 |
29 | Company Profiles |
30 | Unmet needs and opportunity for new suppliers |
31 | Conclusion |
32 | Appendix |