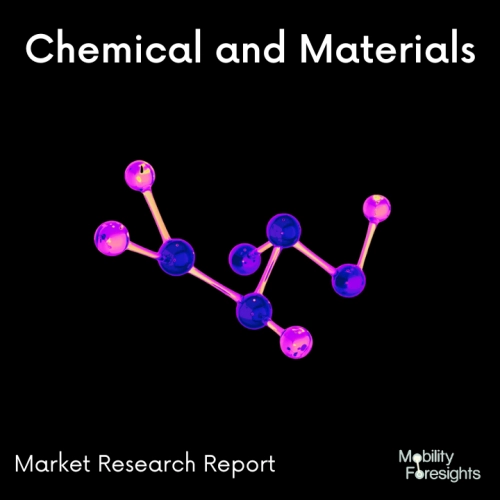
- Get in Touch with Us
Last Updated: Apr 25, 2025 | Study Period: 2024-2030
Chemical vapor deposition (CVD) is a deposition process used to deposit thin, solid films on a variety of substrates. CVD coating is a type of CVD process that is used to deposit coatings on substrates, creating a protective layer. It is commonly used in the aerospace, automotive, electronics, and medical industries
CVD coating is a very precise process that involves the introduction of gas precursors into a hot environment that then chemically reacts to form a solid film on the surface of the substrate.
The type of coating that is deposited depends on the gasses used, the temperature of the environment, and the pressure. The main benefit of CVD coating is that it can be used to deposit very thin, uniform coatings that have excellent adhesion and corrosion resistance.
The process of CVD coating typically starts with the substrate being placed in a vacuum chamber. The chamber is then heated to the desired temperature and the gas precursors are introduced.
After the gasses react, a coating is deposited on the substrate. The thickness of the coating can be controlled by changing the temperature and pressure of the environment. After the coating has been deposited, the substrate is then removed from the chamber and cooled.
CVD coating is a very versatile process that can be used to deposit a variety of coatings. Common coatings include diamond-like carbon (DLC), silicon nitride, and aluminum oxide.
These coatings are used to enhance the wear resistance, corrosion resistance, and electrical insulation of components. CVD coating can also be used to create decorative and functional coatings for decorative and industrial applications.
The Global CVD coating market accounted for $XX Billion in 2023 and is anticipated to reach $XX Billion by 2030, registering a CAGR of XX% from 2024 to 2030.
CVD coating is an emerging technology that has revolutionized the way products are manufactured. CVD (chemical vapor deposition) is a process that deposits a thin layer of material on the surface of a substrate using a chemical reaction. The material is deposited in the form of a thin film, which is then used to provide protection and improve the appearance of the product.
The technology has been used to coat a wide range of products, including medical implants, aerospace components, semiconductor chips, and automotive parts. CVD coating is becoming increasingly popular due to its ability to create durable, corrosion-resistant surfaces. In addition, it can be used to deposit a variety of materials, such as aluminum, titanium, and diamond-like carbon.
In recent years, several companies have launched new products that utilize CVD coating. For example, Hexagon Manufacturing Intelligence recently launched a line of CVD coated tools, which are designed to improve surface finish and wear resistance. Similarly, GKN Aerospace has launched a line of CVD coated aerospace components, which are designed to reduce friction and improve durability.
Overall, CVD coating is an innovative technology that is becoming increasingly popular in a variety of industries. It provides an effective way to improve the performance and durability of products, while also improving the appearance. As a result, many companies are launching new products that utilize CVD coating, and the technology is likely to become even more widespread in the coming years.
Sl no | Topic |
1 | Market Segmentation |
2 | Scope of the report |
3 | Abbreviations |
4 | Research Methodology |
5 | Executive Summary |
6 | Introduction |
7 | Insights from Industry stakeholders |
8 | Cost breakdown of Product by sub-components and average profit margin |
9 | Disruptive innovation in the Industry |
10 | Technology trends in the Industry |
11 | Consumer trends in the industry |
12 | Recent Production Milestones |
13 | Component Manufacturing in US, EU and China |
14 | COVID-19 impact on overall market |
15 | COVID-19 impact on Production of components |
16 | COVID-19 impact on Point of sale |
17 | Market Segmentation, Dynamics and Forecast by Geography, 2024-2030 |
18 | Market Segmentation, Dynamics and Forecast by Product Type, 2024-2030 |
19 | Market Segmentation, Dynamics and Forecast by Application, 2024-2030 |
20 | Market Segmentation, Dynamics and Forecast by End use, 2024-2030 |
21 | Product installation rate by OEM, 2023 |
22 | Incline/Decline in Average B-2-B selling price in past 5 years |
23 | Competition from substitute products |
24 | Gross margin and average profitability of suppliers |
25 | New product development in past 12 months |
26 | M&A in past 12 months |
27 | Growth strategy of leading players |
28 | Market share of vendors, 2023 |
29 | Company Profiles |
30 | Unmet needs and opportunity for new suppliers |
31 | Conclusion |
32 | Appendix |