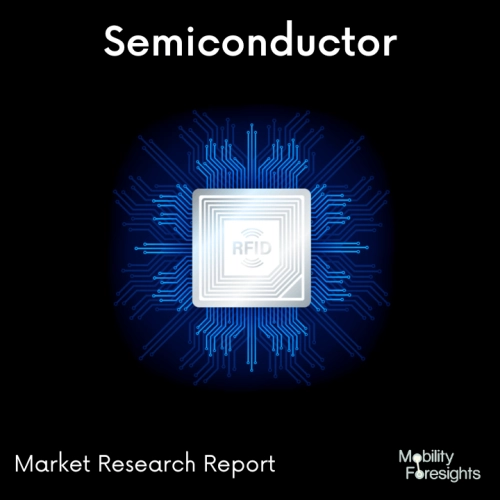
- Get in Touch with Us
Last Updated: Apr 25, 2025 | Study Period:
The Global Cylindrical Grinders Market is expected to experience steady growth throughout 2024-2030, driven by the increasing demand for high-precision components in various industries.This growth is fueled by the automotive, aerospace, and machine tool sectors, where tight tolerances and surface finishes are crucial.
CNC (Computer Numerical Control) cylindrical grinders are leading the market due to their automation capabilities and ability to produce complex parts efficiently.The market is segmented by type, with plunge-grinding and infeed-grinding being the dominant categories. Applications include machining crankshafts, gears, and bearings.
Geographically, Asia Pacific is anticipated to hold the largest market share due to the booming manufacturing sector in China and India.North America and Europe are established markets with a strong presence of leading manufacturers, but growth is expected to be slower.
The growing adoption of automation and Industry 4.0 technologies is influencing the market, with increasing demand for smart grinders with features like real-time monitoring and process control.Sustainability concerns are also playing a role, with manufacturers focusing on energy-efficient grinders and environmentally friendly coolants.
Despite the positive outlook, challenges like skilled labour shortage and fluctuating raw material prices could hinder market growth.Overall, the global cylindrical grinders market presents promising opportunities for manufacturers and suppliers who can cater to the evolving needs of precision machining industries.
Cylindrical Grinders are Precision Machining Tools used to shape the exterior surface of a workpiece with a rotating abrasive wheel. They are commonly employed in industries such as automotive, aerospace, and tool manufacturing to produce cylindrical components with high precision and surface finish. There are two main types of cylindrical grinders: centre-type cylindrical grinders, where the workpiece is held between centres and rotates, and centerless cylindrical grinders, where the workpiece is supported by a work rest blade and rotated by a regulating wheel.
The benefits of cylindrical grinders include their ability to achieve tight tolerances and high surface quality, making them essential for producing components with precise dimensions and smooth finishes. Additionally, cylindrical grinders can handle a wide range of materials, from metals to plastics, making them versatile in various manufacturing applications.
However, these machines also come with certain risks and challenges. One risk is the potential for injury due to the high-speed rotating abrasive wheel, requiring operators to follow strict safety protocols. Another challenge is the complexity of setup and operation, which demands skilled personnel and careful adjustment to achieve desired results consistently.
Furthermore, cylindrical grinders face challenges related to maintenance and downtime, as any mechanical issues or abrasive wheel wear can affect productivity and quality. Additionally, the initial investment cost for cylindrical grinders can be significant, especially for high-precision models with advanced features. Despite these challenges, the benefits of cylindrical grinders in terms of precision machining capabilities and versatility continue to drive their widespread adoption in manufacturing industries worldwide.
The Global Cylindrical Grinders Market accounted for $XX Billion in 2023 and is anticipated to reach $XX Billion by 2030, registering a CAGR of XX% from 2024 to 2030.
Integration of IoT and Automation: The global cylindrical grinders market is witnessing a trend towards the integration of Internet of Things (IoT) and automation technologies into grinding machines. This enables real-time monitoring of machine performance, predictive maintenance, and remote diagnostics, leading to improved efficiency and reduced downtime.
Sustainability Initiatives: Environmental concerns are driving the adoption of sustainable practices in the cylindrical grinders market. Manufacturers are focusing on developing energy-efficient machines, reducing emissions, and implementing eco-friendly processes to align with stringent regulations and meet the growing demand for sustainable manufacturing solutions.
Advanced Materials and Coatings: With the increasing demand for high-performance components, there's a growing trend towards the use of advanced materials such as composites, ceramics, and superalloys in cylindrical grinding applications. Manufacturers are also developing specialized coatings for grinding wheels to enhance durability and performance when working with these materials.
Customization and Flexibility: Market players are offering more customizable and flexible cylindrical grinding solutions to meet diverse customer requirements. This includes modular machine designs, versatile tooling options, and software solutions that allow for easy programming and setup changes, enabling manufacturers to adapt quickly to changing production needs.
Focus on User Experience: There's a growing emphasis on improving the user experience of cylindrical grinding machines through ergonomic design, intuitive interfaces, and enhanced safety features. Manufacturers are investing in human-machine interface (HMI) technologies and operator training programs to ensure safe and efficient operation while optimizing the overall user experience.
DANOBATGROUPintroduced theDANOBAT CG External Cylindrical Grinding Machine, which boasts cutting-edge features designed to meet the evolving demands of precision manufacturing. With a swing diameter of up to 650 mm and a distance between centres of 3,000 mm, this machine offers ample capacity to accommodate a wide range of workpieces. Its robust construction and advanced control system ensure high accuracy and repeatability, making it ideal for applications requiring tight tolerances.
Okuma Corporationintroduced theGENOS M560-VB Vertical Machining Centre. This innovative machine is designed to deliver high-speed, high-precision grinding for a variety of cylindrical components. With its powerful spindle and rigid construction, the GENOS M560-VB offers exceptional stability and accuracy, ensuring consistent performance even in the most demanding applications.
Toyoda Machinery Europe GmbHintroduced theGS300H Horizontal Machining Center. This versatile machine combines high-speed machining capabilities with precision grinding functionalities, making it suitable for a wide range of cylindrical component manufacturing applications. With a compact footprint and ergonomic design, the GS300H offers efficient use of floor space while ensuring ease of operation and maintenance.
Sl no | Topic |
1 | Market Segmentation |
2 | Scope of the Report |
3 | Research Methodology |
4 | Executive Summary |
5 | Introduction |
6 | Average B-2-B Selling Price in Past 5 Years |
7 | Insights from Industry Stakeholders |
8 | Cost Breakdown of Product Components and Average Profit Margin |
9 | Disruptive Innovation in the Industry |
10 | Technological Innovations in Global Cylindrical Grinders Market 2024-2030 |
11 | Integration of IoT and Automation |
12 | Advanced Control Systems and Software |
13 | Sustainable Manufacturing Practices |
14 | Precision Grinding Technologies |
15 | Digital Twin and Virtual Simulation |
16 | Predictive Maintenance Solutions |
17 | Robotics and Cobots Integration |
18 | Real-time Monitoring and Data Analytics |
19 | Additive Manufacturing Integration |
20 | Human-Machine Interface (HMI) Innovations |
21 | New Product Development in the Past 12 Months |
22 | Market Size, Dynamics, and Forecast by Geography (2024-2030) |
23 | Market Size, Dynamics, and Forecast by Type (2024-2030) |
24 | Market Size, Dynamics, and Forecast by Application (2024-2030) |
25 | Market Size, Dynamics, and Forecast by Control (2024-2030) |
26 | Competitive Landscape and Market Share Analysis |
27 | Growth Strategy of Leading Players |
28 | Market Share of Vendors (2024) |
29 | Company Profiles |
30 | Unmet Needs and Opportunities for New Suppliers |
31 | Conclusion |