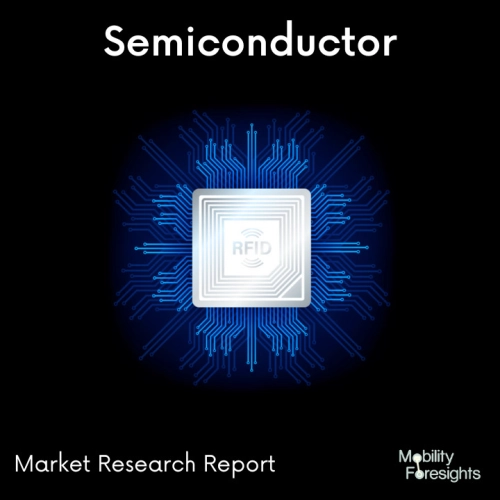
- Get in Touch with Us
Last Updated: Apr 26, 2025 | Study Period: 2024-2030
By applying a collimated monochrome light beam at an incident angle to the surface of the wafer between 8° and a maximum angle determined by the imaging system's numerical aperture and collecting the light that is scattered at angles roughly normal to the wafer's surface and within the imaging system's numerical aperture, an optical inspection system for patterned semiconductor wafers can create a dark field image of the wafer.
Also, the rectangular lines that dominate the pattern are at a 45° angle to the incident light in the wafer's surface plane. The gathered light is sent through a Fourier transform filter, which significantly attenuates the pattern-corresponding spatial frequency components, before being used to create the dark field image.
The faults in the pattern and the contaminating particles are highlighted in comparison to the pattern features in the resulting dark field image. The semiconductor industry faces a serious challenge with the detection of particles and flaws on designed wafers.
Contaminating particles on a semiconductor wafer's surface have the potential to create unexpected conduction channels in the integrated circuits that are built there. Devices that don't work or are of poor quality can result from flaws in one or more of the photolithographic patterns used to make integrated circuits.
Identifying the type and characteristics of any flaws in integrated circuits at different processing stages is crucial so that the defect's root cause can be fixed before it negatively impacts yield.
The Global Dark Field Wafer Defect Inspection System market accounted for $XX Billion in 2023 and is anticipated to reach $XX Billion by 2030, registering a CAGR of XX% from 2024 to 2030.
The Hitachi Dark Field Wafer Defect Inspection System DI2800, an essential part of every semiconductor manufacturer's metrology capabilities, was introduced by Hitachi High-Tech Company. A high-speed metrology device called the DI2800 is intended to find imperfections and foreign objects on patterned wafers up to 8 inches in diameter.
The DI2800 can help assure device dependability and safety because to its high throughput and performance, especially in highly sensitive applications like the Internet of Things and automotive areas where inspection is necessary. To meet these market demands, Hitachi High-Tech created the Dark Field Wafer Defect Inspection System DI2800.
The lighting and detection optics of this product are optimized using scattering-intensity simulation technology, allowing for highly sensitive inspection of patterned-wafer flaws. On mirrored wafers, it can detect particles as small as 0.1 micrometers.
Due to sensitivity and data processing constraints, this performance is even attainable on devices as small as 0.3 mm square, which has previously proven difficult. The DI2800 can inspect approximately 40 200-mm wafers per hour with a highly tuned inspection process.
Sl no | Topic |
1 | Market Segmentation |
2 | Scope of the report |
3 | Abbreviations |
4 | Research Methodology |
5 | Executive Summary |
6 | Introduction |
7 | Insights from Industry stakeholders |
8 | Cost breakdown of Product by sub-components and average profit margin |
9 | Disruptive innovation in the Industry |
10 | Technology trends in the Industry |
11 | Consumer trends in the industry |
12 | Recent Production Milestones |
13 | Component Manufacturing in US, EU and China |
14 | COVID-19 impact on overall market |
15 | COVID-19 impact on Production of components |
16 | COVID-19 impact on Point of sale |
17 | Market Segmentation, Dynamics and Forecast by Geography, 2024-2030 |
18 | Market Segmentation, Dynamics and Forecast by Product Type, 2024-2030 |
19 | Market Segmentation, Dynamics and Forecast by Application, 2024-2030 |
20 | Market Segmentation, Dynamics and Forecast by End use, 2024-2030 |
21 | Product installation rate by OEM, 2023 |
22 | Incline/Decline in Average B-2-B selling price in past 5 years |
23 | Competition from substitute products |
24 | Gross margin and average profitability of suppliers |
25 | New product development in past 12 months |
26 | M&A in past 12 months |
27 | Growth strategy of leading players |
28 | Market share of vendors, 2023 |
29 | Company Profiles |
30 | Unmet needs and opportunity for new suppliers |
31 | Conclusion |
32 | Appendix |