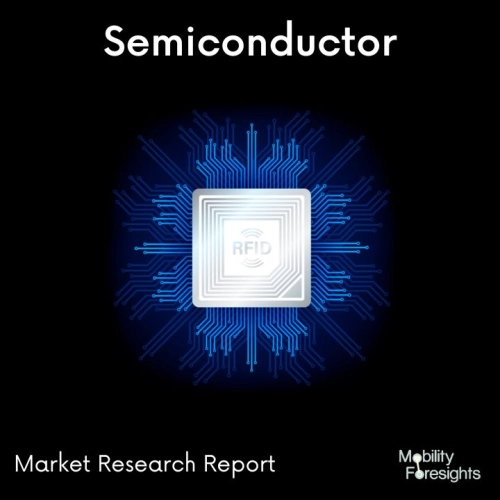
- Get in Touch with Us
Last Updated: Apr 25, 2025 | Study Period: 2024-2030
To ensure the safety of the numerous electrical circuits that develop on a semiconductor wafer, the wafer must be free of severe defects. When ingots develop on the space station, silicon will eventually be forgotten, and the major silicon producers will once more produce amazing silicon discs, although nobody has yet created a flawless one.
The majority of the flaws in silicon wafers can be detected at the silicon producer. The existence of most crystalline defects is undesirable, especially in high-performance electronics and other electronic devices, such as the electronic components of computers and televisions, even though some types of errors are essential in the semiconductor manufacturing process.
The majority of the defects in silicon waves have been discovered in silicon manufacturing facilities and even in silicon chips. However, these faults are typically only discovered in a small subset of silicon chip makers.
The Global defect-free SiC wafers market accounted for $XX Billion in 2023 and is anticipated to reach $XX Billion by 2030, registering a CAGR of XX% from 2024 to 2030.
SiC-based devices are in high demand as an essential part of energy-efficient solutions. However, according to SEI, material advancements are required to meet this demand and compete with the yields and dependability of silicon-based devices.
EpiEra was created by Sumitomo Electric using its multi-parameter and zone (MPZ)-controlled SiC growth technology, which modifies a number of factors (such as temperature, pressure, gas reactions, etc.) based on the location and time zone by employing modelling and monitoring techniques.
According to the company, EpiEra has achieved a purportedly industry-leading 99% defect-free area (DFA), removing surface flaws and basal plane dislocations (BPD) and so enhancing quality stability and dependability.
The global silicon carbide device market is expanding at a compound annual growth rate of 34%, driven mostly by the electric vehicle market. The poor quality of the underlying wafer materials continues to restrict SiC application possibilities.
The practically defect-free growing of SiC wafers is made possible by the ground-breaking growth method developed by Kiselkarbid I Stockholm AB (KISAB) at Linköping Technical University. This technology has the potential to completely transform the SiC device market. The most reputable market research company in the sector, Yole Développement, evaluates the SiC device market and has named KISAB as the "innovative SiC growth technology."
Power component producers will have a significantly enhanced approach to raise yield and build bigger components at higher voltages because of KISAB's capacity to cost-effectively generate defect-free SiC wafers. Additionally, KISAB will soon be able to supply 8-inch SiC wafers free of flaws, which will further boost its competitiveness.
They are thrilled to be joining the business as it moves towards the highly anticipated commercialization phase. Having made an investment in KISAB because of the excellent research that underpins the technology. They join Fairpoint on this journey and look forward to continuing to support KISAB in the upcoming phase.
The ability to ramp up production and assist with clients in producing higher-quality goods at higher yields is possible as a result of their recent start to sample their wafers to customers.
A greater power density packaging for SiC devices with superior heat dissipation is made possible by SiC's excellent thermal conductivity (approximately three times that of Si). Compared to Si-based power devices, it can operate at higher frequencies with fewer switching losses thanks to its improved saturation electron velocity.
Due to SiC's exceptional physical characteristics, a wide range of electronic devices are expected to be developed, including Schottky barrier diodes (SBD), which can withstand high breakdown fields with low reverse leakage currents, and power MOSFETs with high blocking voltage and low on-resistance.
Sl no | Topic |
1 | Market Segmentation |
2 | Scope of the report |
3 | Abbreviations |
4 | Research Methodology |
5 | Executive Summary |
6 | Introduction |
7 | Insights from Industry stakeholders |
8 | Cost breakdown of Product by sub-components and average profit margin |
9 | Disruptive innovation in the Industry |
10 | Technology trends in the Industry |
11 | Consumer trends in the industry |
12 | Recent Production Milestones |
13 | Component Manufacturing in US, EU and China |
14 | COVID-19 impact on overall market |
15 | COVID-19 impact on Production of components |
16 | COVID-19 impact on Point of sale |
17 | Market Segmentation, Dynamics and Forecast by Geography, 2024-2030 |
18 | Market Segmentation, Dynamics and Forecast by Product Type, 2024-2030 |
19 | Market Segmentation, Dynamics and Forecast by Application, 2024-2030 |
20 | Market Segmentation, Dynamics and Forecast by End use, 2024-2030 |
21 | Product installation rate by OEM, 2024 |
22 | Incline/Decline in Average B-2-B selling price in past 5 years |
23 | Competition from substitute products |
24 | Gross margin and average profitability of suppliers |
25 | New product development in past 12 months |
26 | M&A in past 12 months |
27 | Growth strategy of leading players |
28 | Market share of vendors, 2024 |
29 | Company Profiles |
30 | Unmet needs and opportunity for new suppliers |
31 | Conclusion |
32 | Appendix |