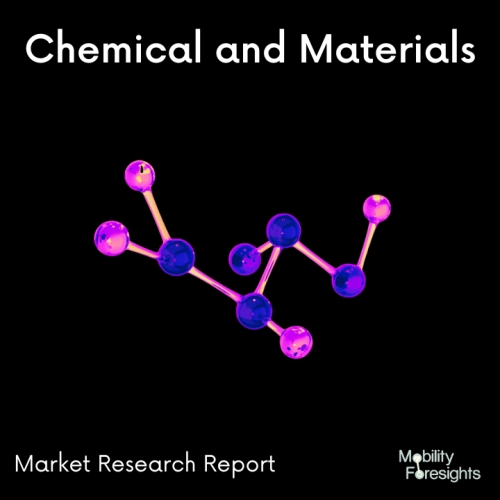
- Get in Touch with Us
Last Updated: Apr 25, 2025 | Study Period: 2024-2030
Adhesives for die attach are used to secure semiconductor chips to the surfaces of packaging. They can aid in establishing the attachment and reducing tension and warpage while the device is in operation. Some die attach adhesives have been designed to be both electrically insulating and thermally conducting.
The process of connecting a semiconductor die to a packaging, a substrate like a PCB board, or another die is known as die attach or die bonding. The die attach procedure is crucial to many different kinds of packaging.
The Global Die attached adhesives market accounted for $XX Billion in 2023 and is anticipated to reach $XX Billion by 2030, registering a CAGR of XX% from 2024 to 2030.
Henkel introduces a die-attach adhesive with ultra-high heat conductivity.Loctite Ablestik ABP 8068TI has been added by Henkel to its expanding line of high-thermal die-attach adhesives.
The new pressure-free sintering die-attach paste has the highest thermal capability in the company's range of semiconductor packaging, boasting 165 W/m-K thermal conductivity. It meets the performance criteria for highly reliable automotive and industrial power-discrete semiconductor devices.
For better efficiency, power semiconductors like MOSFETs are increasingly combining silicon carbide (SiC) and gallium nitride (GaN) materials as alternatives to silicon (Si), and Henkel's newest pressureless sintering die-attach formulation satisfies these requirements.
Other power-discrete devices, such as modern wide-bandgap semiconductors, are compatible with Loctite Ablestik ABP 8068TI.
The 165 W/m-K ultra-high thermal conductivity die-attach adhesive has shown excellent sintering characteristics with good adhesion on copper (Cu), pre-plated frames (PPF), silver (Ag), and gold (Au), robust electrical conductivity and stable RDS(on) after 1,000 hours of thermal cycling, and MSL 3 reliability.
Loctite Ablestik ABP 8068TI completely cures at 175° C or above to generate a hard sintered Ag network in the bulk epoxy and at the interface. It is advised for dies measuring 3.0 x 3.0 mm or less.
High pressure is not necessary to generate this strong structure since pressureless sintering may be used as a drop-in substitute for conventional die attach, which reduces stress on thin die. The material's workability is noteworthy at three hours of void-free open time and 24 hours of staging without a loss in shear strength.
Sl no | Topic |
1 | Market Segmentation |
2 | Scope of the report |
3 | Abbreviations |
4 | Research Methodology |
5 | Executive Summary |
6 | Introdauction |
7 | Insights from Industry stakeholders |
8 | Cost breakdown of Product by sub-components and average profit margin |
9 | Disruptive innovation in theIndustry |
10 | Technology trends in the Industry |
11 | Consumer trends in the industry |
12 | Recent Production Milestones |
13 | Component Manufacturing in US, EU and China |
14 | COVID-19 impact on overall market |
15 | COVID-19 impact on Production of components |
16 | COVID-19 impact on Point of sale |
17 | Market Segmentation, Dynamics and Forecast by Geography, 2024-2030 |
18 | Market Segmentation, Dynamics and Forecast by Product Type, 2024-2030 |
19 | Market Segmentation, Dynamics and Forecast by Application, 2024-2030 |
20 | Market Segmentation, Dynamics and Forecast by End use, 2024-2030 |
21 | Product installation rate by OEM, 2023 |
22 | Incline/Decline in Average B-2-B selling price in past 5 years |
23 | Competition from substitute products |
24 | Gross margin and average profitability of suppliers |
25 | New product development in past 12 months |
26 | M&A in past 12 months |
27 | Growth strategy of leading players |
28 | Market share of vendors, 2023 |
29 | Company Profiles |
30 | Unmet needs and opportunity for new suppliers |
31 | Conclusion |
32 | Appendix |