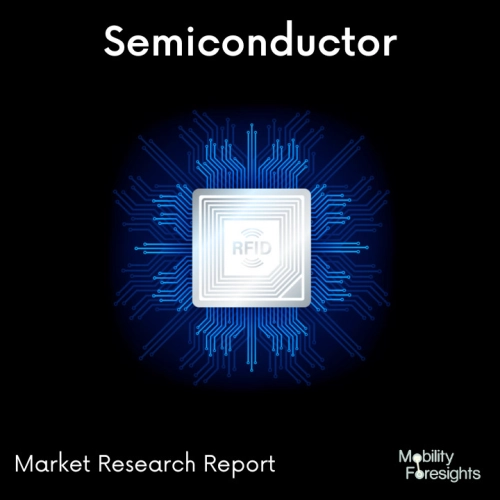
- Get in Touch with Us
Last Updated: Apr 25, 2025 | Study Period: 2023-2030
Die sorting is a technique used to divide the die on a wafer into groups according to their quality or other factors. Even when every die on a wafer is supposed to be the same, this seldom ever happens.
In order to produce device packaging that is both affordable and high-yield, it becomes important to sort the die according to their properties.
Processes for Die Sorting AutomationUsing an eject head and pick-up tip mechanism, a die sorting system is created to extract die from tape and transfer them to output carriers.
Through the use of process recipes, semi- and fully-automatic die sorters give the operator total control over the precise die eject parameters, including eject needle height, eject speed, and placement pattern on the die sorting, die eject, flip chip, output.
This enables the same product to be processed again from one die to the next and allows for the use of various settings for various goods.
It's crucial to think about whether a semi-automated or completely automatic system is needed when assessing a die sorter option.
A semi-automatic die sorter is the best option for applications with a wide range of different products because it provides a repeatable process at a lesser cost than a fully automatic system.
For the operator to ensure that the product coming out of the die is of high quality, a semi-automatic solution can also be equipped with topside, underneath, and edge inspection options.
Global die sorting and inspection systems market accounted for $XX Billion in 2022 and is anticipated to reach $XX Billion by 2030, registering a CAGR of XX% from 2023 to 2030.
Engineers can rapidly spot any problems during the dicing process of wafer-level packages and bare dies with the use of KLA's die sorting and inspection system, which offers inspection prior to die assembly.
Low k materials in fan-in wafer-level packages, for example, have been added to the process as a result of advancements in wafer-level packaging technology, making them potentially vulnerable to cracking during dicing.
Their method helps chip makers reduce production risk by immediately spotting flaws during die sorting to ensure greater outgoing quality for the following stage of assembly for increasingly complex packages, extensively used in applications including communications, consumer, automotive, and more.
The ICOSTM F260 die sorting and inspection system offers integrated, completely automated inspection of diced wafer-level packages together with high performance die sorting.
The ICOS F260 system has a brand-new, cutting-edge short wave IR inspection module that, at high throughput and with almost no overkill or underkill, reliably detects hairline and sidewall fractures.
A specialist laser groove inspection module with sensitivity to undetectable laser groove cracks, which are fatal flaws for sophisticated fan-in wafer-level packages, memory, and bare dies, can be be added to the system.
In order to maximise tool use in high volume manufacturing environments, the ICOS F260 system supports a wide range of workflows, including wafer-to-tape and tape-to-tape, with a minimal amount of changeover time.
Sl no | Topic |
1 | Market Segmentation |
2 | Scope of the report |
3 | Abbreviations |
4 | Research Methodology |
5 | Executive Summary |
6 | Introduction |
7 | Insights from Industry stakeholders |
8 | Cost breakdown of Product by sub-components and average profit margin |
9 | Disruptive innovation in the Industry |
10 | Technology trends in the Industry |
11 | Consumer trends in the industry |
12 | Recent Production Milestones |
13 | Component Manufacturing in US, EU and China |
14 | COVID-19 impact on overall market |
15 | COVID-19 impact on Production of components |
16 | COVID-19 impact on Point of sale |
17 | Market Segmentation, Dynamics and Forecast by Geography, 2023-2030 |
18 | Market Segmentation, Dynamics and Forecast by Product Type, 2023-2030 |
19 | Market Segmentation, Dynamics and Forecast by Application, 2023-2030 |
20 | Market Segmentation, Dynamics and Forecast by End use, 2023-2030 |
21 | Product installation rate by OEM, 2023 |
22 | Incline/Decline in Average B-2-B selling price in past 5 years |
23 | Competition from substitute products |
24 | Gross margin and average profitability of suppliers |
25 | New product development in past 12 months |
26 | M&A in past 12 months |
27 | Growth strategy of leading players |
28 | Market share of vendors, 2023 |
29 | Company Profiles |
30 | Unmet needs and opportunity for new suppliers |
31 | Conclusion |
32 | Appendix |