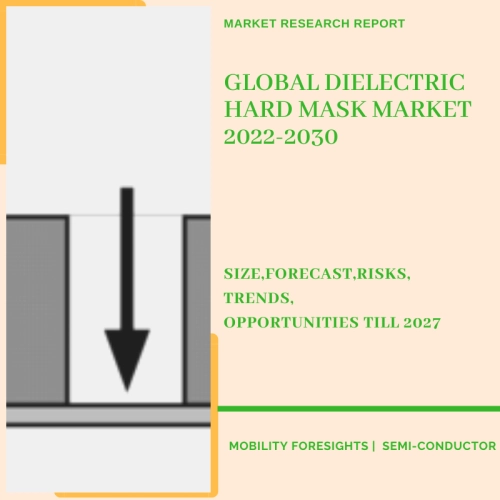
- Get in Touch with Us
Last Updated: Apr 26, 2025 | Study Period: 2022-2030
In semiconductor fabrication, a hardmask is used as an etch mask in place of a polymer or other organic "soft" resist material.When the substance being etched is an organic polymer, hardmasks are required.
Since the photoresist being utilised to define its patterning is likewise an organic polymer, anything used to etch this material will also etch the photoresist.
This occurs, for instance, when low-dielectric insulating layers used in VLSI production are patterned. Oxygen, fluorine, chlorine, and other reactive gases employed in plasma etching have a tendency to easily etch polymers.
Using a hardmask necessitates an additional deposition procedure, which raises the cost. First, a typical photoresist method is used to deposit and etch the hardmask material into the desired design. The underlying material can then be etched through the hardmask after that. Finally, a second etching procedure is used to remove the hard mask.
Metal or dielectric can be used as hardmask materials. Low-dielectric materials are often etched using silicon-based masks made of silicon dioxide or silicon carbide.However, an etchant that destroys silicon compounds is necessary for SiOCH (carbon doped hydrogenated silicon oxide), a material used to insulate copper interconnects.
Hardmasks made of metal or amorphous carbon are utilised with this material. Tantalum nitride has also been utilised, but titanium nitride is the material most frequently used for hardmasks.
The first two of the three materials utilised in microelectronicsâsemiconductors, metals, and dielectricsâoften receive the greatest focus. To meet the performance, power, and reliability requirements of current microelectronic products, a diverse array of dielectric materials are urgently needed for device fabrication and interconnect isolation.
Indeed, the continuing scaling attained in advanced nodes has been largely attributed to advancements in dielectrics. (Take, for instance, high-k gate dielectrics.) Additionally, the chemical characteristics of dielectric materials are crucial in many process phases, from their usage as a sidewall spacer to permit selective epitaxial growth on exposed silicon to their employment as a patterned hard mask to act as a protective etch barrier.
The Global dielectric hard mask market accounted for $XX Billion in 2021 and is anticipated to reach $XX Billion by 2030, registering a CAGR of XX% from 2022 to 2030.
Etching characteristics of a TiN dielectric hard mask when utilising a dielectric etch process, including etch rate and faceting.The etching tests were carried out in an inductively coupled plasma with a typical CF4/Ar based plasma on blanket wafers and patterned structures.
The plasma parameters (bias power and pressure) as well as the plasma chemistries have been measured in relation to the etch rate and faceting of TiN. (Ar dilution and CH2F2 addition). Using the baseline process conditions, the TiN etch rate is approximately 30 nm min-1 (70 SCCMCF4, source power of 500 W, bias power of 100 W, and pressure of 4 mTorr).
Dielectric materials must be compatible with a wide range of deposition methods, including spin-on dielectric coatings for trench filling and chemical vapour deposition for isotropic addition to the surface topography.
To achieve ambitious power, performance, yield, and reliability requirements, research into novel dielectric materials is essential. Intel presented two presentations at the recent IEDM conference that detailed some of their research (as well as other contributions) into the introduction of novel dielectrics and an intriguing method for fabricating the matching metal interconnects.
In order to permit an aggressive pitch of etched layers for advanced process nodes, a self-aligned, dual patterning (SADP) phase is pursued as an affordable alternative to multi patterning lithography/etch process sequences. It is obvious that a lengthy process is needed to apply for SADP. Implementing selective deposition of the dielectric material would be a desirable substitute.
Sl no | Topic |
1 | Market Segmentation |
2 | Scope of the report |
3 | Abbreviations |
4 | Research Methodology |
5 | Executive Summary |
6 | Introduction |
7 | Insights from Industry stakeholders |
8 | Cost breakdown of Product by sub-components and average profit margin |
9 | Disruptive innovation in the Industry |
10 | Technology trends in the Industry |
11 | Consumer trends in the industry |
12 | Recent Production Milestones |
13 | Component Manufacturing in US, EU and China |
14 | COVID-19 impact on overall market |
15 | COVID-19 impact on Production of components |
16 | COVID-19 impact on Point of sale |
17 | Market Segmentation, Dynamics and Forecast by Geography, 2022-2030 |
18 | Market Segmentation, Dynamics and Forecast by Product Type, 2022-2030 |
19 | Market Segmentation, Dynamics and Forecast by Application, 2022-2030 |
20 | Market Segmentation, Dynamics and Forecast by End use, 2022-2030 |
21 | Product installation rate by OEM, 2022 |
22 | Incline/Decline in Average B-2-B selling price in past 5 years |
23 | Competition from substitute products |
24 | Gross margin and average profitability of suppliers |
25 | New product development in past 12 months |
26 | M&A in past 12 months |
27 | Growth strategy of leading players |
28 | Market share of vendors, 2022 |
29 | Company Profiles |
30 | Unmet needs and opportunity for new suppliers |
31 | Conclusion |
32 | Appendix |