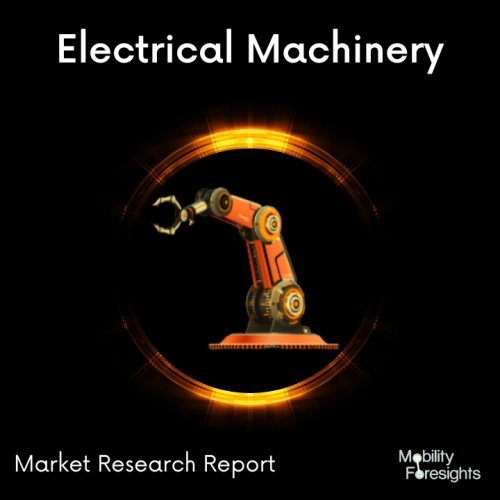
- Get in Touch with Us
Last Updated: Apr 25, 2025 | Study Period: 2023-2030
A crucial component of the vehicle's drivetrain, the differential housing's job is to contain differential gear assemblies and absorb torque generated by those gears.
The difficulty of interrupted cuts during roughing passes is a problem with differential housings, which are made of nodular cast iron and house the vehicle differential gear assemblies.
A differential's job is to transfer engine power to the axle that moves the wheels while allowing the wheels to move at various speeds.
The Global Differential Housing Machine market accounted for $XX Billion in 2022 and is anticipated to reach $XX Billion by 2030, registering a CAGR of XX% from 2023 to 2030.
Complex differential housing turning is becoming more difficult as production volumes increase; the part will continue to be essential for all propulsion systems in the future. EMAG creates production lines using extremely quick procedures.
Therefore, the manufacturing of differential housings must adhere to the strict standards typical of the automobile sector, which include high production volumes, error-free procedures, and quick cycle times. The differential's central linking member, however, also has a very complicated shape.
As a result, the turning operation is labor-intensive and composed of various subprocesses. Other variations of the component include closed full-sphere cases, half-sphere cases, and open cases with covers.
EMAG has long since become an expert in this component's machining. Based on its modular machine platform, its mechanical engineers create complete manufacturing lines.
These lines employ tried-and-true pick-up devices that are easily interconnected utilising EMAG's TrackMotion system. A very quick, trustworthy process with minimum idle time is the end result. Also, the line takes extremely minimal space because of its vertical turning machinery.
A closed half-sphere differential housing would have a different arrangement. This time, the procedure would start in OP10 with the turning of an EMAG VL 6's initial side.
On a second VL 6, the second side (OP20) is turned, and a drilling operation is performed. The two procedures are little different up to this point.
The interior machining of the half-final sphere's surface (OP30) is fascinating, though; EMAG's experts chose a VSC 250 DD and specially made tools for it. As a result, the machining process takes incredibly little timeâthis inside turning operation takes just 125 seconds to complete.
Sl no | Topic |
1 | Market Segmentation |
2 | Scope of the report |
3 | Abbreviations |
4 | Research Methodology |
5 | Executive Summary |
6 | Introduction |
7 | Insights from Industry stakeholders |
8 | Cost breakdown of Product by sub-components and average profit margin |
9 | Disruptive innovation in the Industry |
10 | Technology trends in the Industry |
11 | Consumer trends in the industry |
12 | Recent Production Milestones |
13 | Component Manufacturing in US, EU and China |
14 | COVID-19 impact on overall market |
15 | COVID-19 impact on Production of components |
16 | COVID-19 impact on Point of sale |
17 | Market Segmentation, Dynamics and Forecast by Geography, 2023-2030 |
18 | Market Segmentation, Dynamics and Forecast by Product Type, 2023-2030 |
19 | Market Segmentation, Dynamics and Forecast by Application, 2023-2030 |
20 | Market Segmentation, Dynamics and Forecast by End use, 2023-2030 |
21 | Product installation rate by OEM, 2023 |
22 | Incline/Decline in Average B-2-B selling price in past 5 years |
23 | Competition from substitute products |
24 | Gross margin and average profitability of suppliers |
25 | New product development in past 12 months |
26 | M&A in past 12 months |
27 | Growth strategy of leading players |
28 | Market share of vendors, 2023 |
29 | Company Profiles |
30 | Unmet needs and opportunity for new suppliers |
31 | Conclusion |
32 | Appendix |