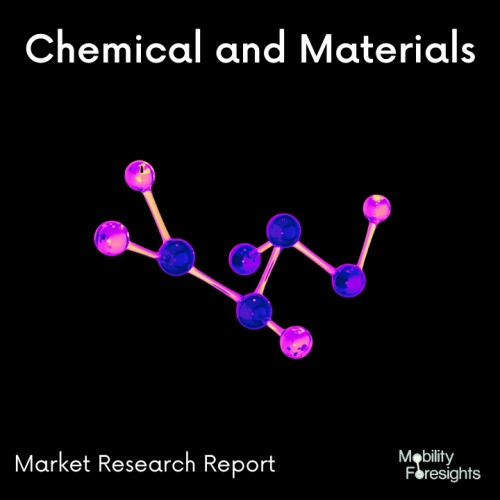
- Get in Touch with Us
Last Updated: Apr 25, 2025 | Study Period: 2024-2030
A focused beam of energy is used in the direct energy deposition additive manufacturing technology, a type of 3D printing, to melt and fuse metal particles into three-dimensional objects.
Complex parts and components made of metal alloys including titanium, aluminium, stainless steel, and cobalt chrome are produced using this method of additive manufacturing. In order to create parts rapidly and precisely, direct energy deposition is required.
In the direct energy deposition technique, metal powder particles are heated and melted onto the surface of a base plate using a focussed energy beam (usually a laser or electron beam). The desired shape is subsequently formed by fusing the powder together. The ultimate product is created by cooling and hardening the powder.
Direct energy deposition additive manufacturing has many benefits. It is frequently used to build parts and components that are impossible to fabricate using conventional manufacturing techniques.
It can be utilised to accurately create complex geometries. Direct energy deposition is additionally quicker than conventional techniques, enabling quicker manufacturing schedules and cost reductions.
Limited material options and high production costs are two drawbacks of direct energy deposition additive manufacturing. The equipment required for direct energy deposition is relatively expensive, and the method is most cost-effective when utilised to create large quantities of parts.
Additionally, not all materials can be used with the process, and certain materials might not be able to tolerate the high temperatures involved.
Direct energy deposition is a practical and effective method for creating intricate parts and components. It is frequently employed in settings where conventional manufacturing techniques are impractical since it can swiftly and accurately produce parts. The procedure is less appealing for various applications due to the expensive equipment and the limited material options.
The Global Direct Energy Deposition Additive Manufacturing System Market accounted for $XX Billion in 2023 and is anticipated to reach $XX Billion by 2030, registering a CAGR of XX% from 2024 to 2030.
Metal X by Markforged, Inc. is the world's first desktop metal 3D printer. The Metal X is the most recent advancement in additive manufacturing. This robust system allows for industrial-grade metal 3D printing at a fraction of the cost of traditional metal printing processes.
The Metal X uses Direct Energy Deposition (DED) technology to build metal parts from powdered metals quickly and accurately. The Metal X is a cost-effective, reliable, and high-performance metal part production system with a simple user interface, an integrated powder handling system, and minimal post-processing.
Mitsubishi Electric's Direct Energy Deposition (DED) Additive Manufacturing System is a quick and dependable solution for custom part production. It employs direct energy deposition in conjunction with Mitsubishi Electric's advanced powder delivery system to produce parts with improved accuracy, repeatability, and process stability.
The system can deposit multiple materials at high deposition rates, making it an ideal solution for manufacturing complex and customised parts. With its simple control interface, the system provides an easy-to-use platform for users to quickly and easily create custom parts.
Sl no | Topic |
1 | Market Segmentation |
2 | Scope of the report |
3 | Abbreviations |
4 | Research Methodology |
5 | Executive Summary |
6 | Introduction |
7 | Insights from Industry stakeholders |
8 | Cost breakdown of Product by sub-components and average profit margin |
9 | Disruptive innovation in the Industry |
10 | Technology trends in the Industry |
11 | Consumer trends in the industry |
12 | Recent Production Milestones |
13 | Component Manufacturing in US, EU and China |
14 | COVID-19 impact on overall market |
15 | COVID-19 impact on Production of components |
16 | COVID-19 impact on Point of sale |
17 | Market Segmentation, Dynamics and Forecast by Geography, 2024-2030 |
18 | Market Segmentation, Dynamics and Forecast by Product Type, 2024-2030 |
19 | Market Segmentation, Dynamics and Forecast by Application, 2024-2030 |
20 | Market Segmentation, Dynamics and Forecast by End use, 2024-2030 |
21 | Product installation rate by OEM, 2023 |
22 | Incline/Decline in Average B-2-B selling price in past 5 years |
23 | Competition from substitute products |
24 | Gross margin and average profitability of suppliers |
25 | New product development in past 12 months |
26 | M&A in past 12 months |
27 | Growth strategy of leading players |
28 | Market share of vendors, 2023 |
29 | Company Profiles |
30 | Unmet needs and opportunity for new suppliers |
31 | Conclusion |
32 | Appendix |