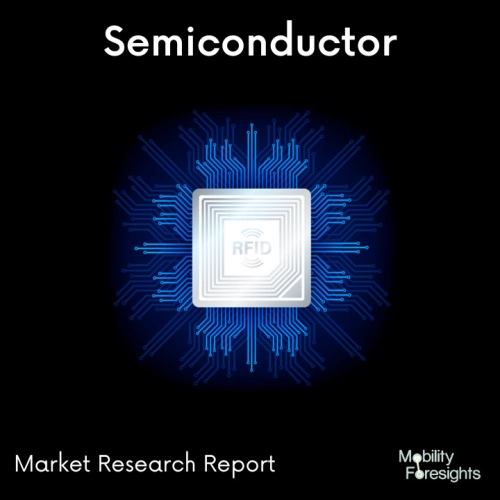
- Get in Touch with Us
Last Updated: Apr 25, 2025 | Study Period: 2023-2030
Calculating the size and distribution of the particles that make up a material requires the use of particle analyzers. For research and development, manufacturing, quality control, and product testing, particle size analyzers are utilised in a variety of industries.
Everywhere that powders and bulk materials flow, a direct imaging particle analyzer can be utilised. It was designed to meet the criteria of the pharmaceutical business.
The angular fluctuation in light intensity that occurs as a laser beam travels through a dispersed particulate sample allows laser diffraction to determine the particle size distributions. When compared to the laser beam, microscopic particles scatter light at large angles while large particles do so at small angles.
The Global Direct Imaging Particle Analyzer Market accounted for $XX Billion in 2022 and is anticipated to reach $XX Billion by 2030, registering a CAGR of XX% from 2023 to 2030.
The Eyecon 2TM is a real-time, direct imaging particle analyzer that can be used everywhere powders and bulk solids flow. It was designed to meet the criteria of the pharmaceutical sector.
With real-time particle size distribution and shape data updated every 5 sec, it offers quicker comprehension of particle size, shape, and variation. The Eyecon2 is well suited for usage in the culinary, chemical, agricultural, cosmetic, and veterinary industries and has a measurement range of 50 to 5500 m.
The Eyecon2 aids customers in comprehending particle size and shape variation, which in turn enables them to ascertain why a process is failing, why yield is decreasing, what the cause of product variation is, and whether or how a method can be scaled up to commercial manufacture.
D-values, despite being simplistic, are a good fit for this requirement because they provide a particle size quantification approach that is better adapted to the unique needs of the pharmaceutical business.
installations on fluidized bed coating (such as the Wurster), fluidized bed granulation/drying, twin screw granulation, dry granulation/roller compaction, extrusion spheronization, milling, blending, and product transfer process equipment have all been tried and tested.
uses direct imaging that is real-time processed, with ellipses fitting to each particle's border and the shape and size of the particle being sent back to highlight differences.
The development of a data-driven control plan requires continuous monitoring of the processes' critical quality attributes (CQAs). enables real-time measurement of manufacturing processes both in-line and at-line/benchtop. Non-product contact to guarantee accurate measurements each and every time.Direct Imaging Particle Analyzer Market
Sl no | Topic |
1 | Market Segmentation |
2 | Scope of the report |
3 | Abbreviations |
4 | Research Methodology |
5 | Executive Summary |
6 | Introduction |
7 | Insights from Industry stakeholders |
8 | Cost breakdown of Product by sub-components and average profit margin |
9 | Disruptive innovation in the Industry |
10 | Technology trends in the Industry |
11 | Consumer trends in the industry |
12 | Recent Production Milestones |
13 | Component Manufacturing in US, EU and China |
14 | COVID-19 impact on overall market |
15 | COVID-19 impact on Production of components |
16 | COVID-19 impact on Point of sale |
17 | Market Segmentation, Dynamics and Forecast by Geography, 2023-2030 |
18 | Market Segmentation, Dynamics and Forecast by Product Type, 2023-2030 |
19 | Market Segmentation, Dynamics and Forecast by Application, 2023-2030 |
20 | Market Segmentation, Dynamics and Forecast by End use, 2023-2030 |
21 | Product installation rate by OEM, 2023 |
22 | Incline/Decline in Average B-2-B selling price in past 5 years |
23 | Competition from substitute products |
24 | Gross margin and average profitability of suppliers |
25 | New product development in past 12 months |
26 | M&A in past 12 months |
27 | Growth strategy of leading players |
28 | Market share of vendors, 2023 |
29 | Company Profiles |
30 | Unmet needs and opportunity for new suppliers |
31 | Conclusion |
32 | Appendix |