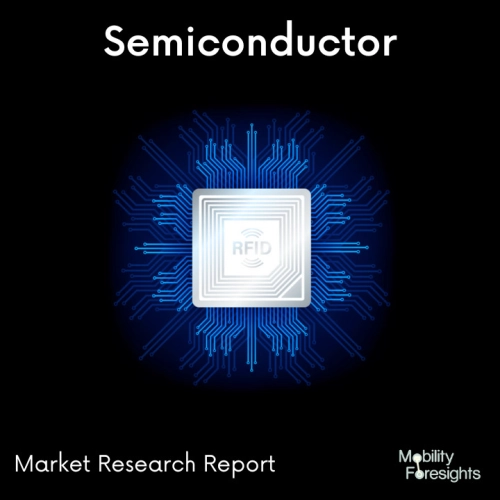
- Get in Touch with Us
Last Updated: Apr 25, 2025 | Study Period:
Direct Liquid Injection is referred to as DLI. This technology for vaporising substances was initially created to evaporate chemical precursors with low vapour pressure.
Reactors that use liquid delivery units to supply reactants into the deposition zone are referred to as "direct liquid injection (DLI)-CVD" systems. A liquid's flow rate can be controlled much more precisely than a powder's.
A chamber outside the intake manifold houses a pre-mix of gasoline and air in the conventional (indirect) fuel injection system. The fuel and air in the direct injection system are not pre-mixed. While the air is drawn in through the intake manifold, the gasoline is injected straight into the cylinder.
The Global Direct Liquid Injection System Market accounted for $XX Billion in 2024 and is anticipated to reach $XX Billion by 2030, registering a CAGR of XX% from 2024 to 2030.
A direct liquid injection technique for chemical vapour deposition of nanoparticles employing nanoparticle solutions is being developed. There are currently numerous applications for nanoparticles made of various materials.
These nanoparticles need to be placed on a substrate quickly and consistently in particular applications. They have created a brand-new direct liquid injection technique for chemical vapour deposition of nanoparticles employing a liquid nanoparticle precursor.
Two direct liquid injectors were used to deliver nanoparticles to the system, which was created to deposit them in a regulated and repeatable manner. Following the evaporation of the nanoparticle solution, the particles flow onto a substrate inside the vacuum chamber.
A direct liquid injection and vaporisation system is positioned on top of the process chamber to enable the liquid's injection and evaporation. The temperature of the deposition, the partial pressure of the gases, and the flow rate of the suspension of nanoparticles are some of the factors that affect the deposition of nanoparticles.
Just altering the flow rate and deposition time will change the concentration of the nanoparticles that are deposited. They use gold nanoparticles to show the system's capabilities.
The chosen suspension flow rates were adjusted to range from 0.25 to 1 g/min. The deposited samples' AFM examination revealed that the flow and deposition parameters effectively regulate the agglomeration of gold nanoparticles.
THIS REPORT WILL ANSWER FOLLOWING QUESTIONS
Sl no | Topic |
1 | Market Segmentation |
2 | Scope of the report |
3 | Abbreviations |
4 | Research Methodology |
5 | Executive Summary |
6 | Introduction |
7 | Insights from Industry stakeholders |
8 | Cost breakdown of Product by sub-components and average profit margin |
9 | Disruptive innovation in the Industry |
10 | Technology trends in the Industry |
11 | Consumer trends in the industry |
12 | Recent Production Milestones |
13 | Component Manufacturing in US, EU and China |
14 | COVID-19 impact on overall market |
15 | COVID-19 impact on Production of components |
16 | COVID-19 impact on Point of sale |
17 | Market Segmentation, Dynamics and Forecast by Geography, 2023-2030 |
18 | Market Segmentation, Dynamics and Forecast by Product Type, 2023-2030 |
19 | Market Segmentation, Dynamics and Forecast by Application, 2023-2030 |
20 | Market Segmentation, Dynamics and Forecast by End use, 2023-2030 |
21 | Product installation rate by OEM, 2023 |
22 | Incline/Decline in Average B-2-B selling price in past 5 years |
23 | Competition from substitute products |
24 | Gross margin and average profitability of suppliers |
25 | New product development in past 12 months |
26 | M&A in past 12 months |
27 | Growth strategy of leading players |
28 | Market share of vendors, 2023 |
29 | Company Profiles |
30 | Unmet needs and opportunity for new suppliers |
31 | Conclusion |
32 | Appendix |