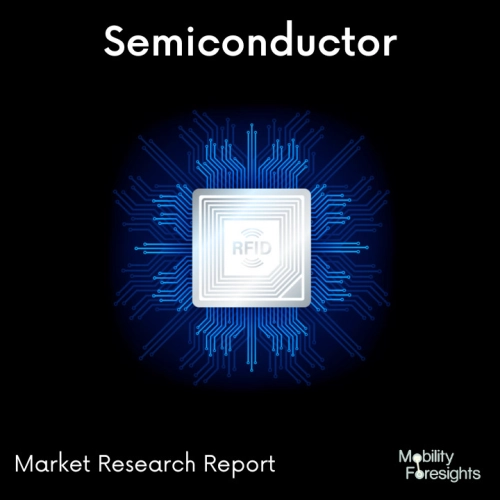
- Get in Touch with Us
Last Updated: Apr 25, 2025 | Study Period: 2024-2030
Directed Self-Assembly (DSA) lithography is an emerging nano-fabrication technology with potential to revolutionise the semiconductor industry. DSA lithography is a technique which uses self-assembling block copolymers (BCP) to create nanoscale patterns.
These block copolymers are polymers that are made up of two or more chemically distinct polymeric blocks which have a tendency to self-assemble into intricate patterns. The unique combination of the different blocks of polymers can be used to create patterns with feature sizes below the optical lithography limit.
DSA lithography provides a way to reliably fabricate nanostructures with low cost and high yield. In DSA lithography, a mask is not required and the pattern is produced by self-assembly of the block copolymers.
This process occurs in a solution and is achieved through a combination of thermal annealing and solvent annealing. Through this process, the block copolymers form into nanoscale patterns that can be used for various applications such as photonics, biosensors, and transistors.
The advantages of DSA lithography compared to traditional lithography methods include: lower cost, higher resolution, and faster turnaround. Additionally, it is more efficient and provides more precise control over the pattern formation process. Furthermore, the process is environmentally friendly and does not require the use of hazardous chemicals.
In conclusion, DSA lithography is a promising technology that could revolutionise the semiconductor industry. It is a process that offers a cost-effective, high-resolution, and efficient way of fabricating nanostructures with low cost and high yield. This technology will enable us to make smaller and more precise devices, which could lead to new possibilities in many industries.
The Global Directed Self-Assembly lithography Market accounted for $XX Billion in 2023 and is anticipated to reach $XX Billion by 2030, registering a CAGR of XX% from 2024 to 2030.
In order to enhance both optical and extreme ultraviolet lithography, the European research institute IMEC (Leuven, Belgium) co-developed a directed self-assembly (DSA) production method and constructed a suitable manufacturing line within its pilot fab.
It is anticipated that the organization will make an announcement at the SPIE Advanced Lithography Conference about the effective implementation of DSA. DSA creates ordered structures by utilizing the inherent processes of materials.
By adjusting the chemistry, some of these processes like the creation of stripes in polymeric materials may be fine-tuned to produce nanometric features that can be enhanced with optical and extreme ultraviolet lithography.
In partnership with Tokyo Electron Ltd., AZ Electronic Materials, and the University of Wisconsin, an academic lab-scale DSA process flow was upgraded to a fab-compatible flow. The partnership seeks to advance DSA to large-scale production.
The use of Directed Self-Assembly (DSA) to advance optical lithography beyond its present limitations is becoming more and more popular. Block copolymers are used in DSA, an alternate patterning technology, to enable frequency multiplication. DSA can lower the pitch when it's combined with a suitable pre-pattern that guides the orientation for patterning.
Using a high-chi block copolymer (high-Ï BCP) based process under high volume manufacturing (HVM) conditions, directed self-assembly (DSA) demonstrates for the first time its ability to pattern line/spaces with a pitch as small as 18nm at the SPIE Advanced Lithography Conference, imec, a world-leading research and innovation hub in nanoelectronics and digital technologies.
The pattern was effectively transferred into an underlying thick SiN layer using an improved dry-etch chemical, allowing for additional defectivity examination. The potential of DSA to supplement conventional top-down patterning for the industrial manufacturing of sub-2nm technology nodes is confirmed by these results. It will be necessary to pattern features with crucial pitches smaller than 20 nm in order to further reduce the size of devices.
Sl no | Topic |
1 | Market Segmentation |
2 | Scope of the report |
3 | Abbreviations |
4 | Research Methodology |
5 | Executive Summary |
6 | Introdauction |
7 | Insights from Industry stakeholders |
8 | Cost breakdown of Product by sub-components and average profit margin |
9 | Disruptive innovation in theIndustry |
10 | Technology trends in the Industry |
11 | Consumer trends in the industry |
12 | Recent Production Milestones |
13 | Component Manufacturing in US, EU and China |
14 | COVID-19 impact on overall market |
15 | COVID-19 impact on Production of components |
16 | COVID-19 impact on Point of sale |
17 | Market Segmentation, Dynamics and Forecast by Geography, 2024-2030 |
18 | Market Segmentation, Dynamics and Forecast by Product Type, 2024-2030 |
19 | Market Segmentation, Dynamics and Forecast by Application, 2024-2030 |
20 | Market Segmentation, Dynamics and Forecast by End use, 2024-2030 |
21 | Product installation rate by OEM, 2023 |
22 | Incline/Decline in Average B-2-B selling price in past 5 years |
23 | Competition from substitute products |
24 | Gross margin and average profitability of suppliers |
25 | New product development in past 12 months |
26 | M&A in past 12 months |
27 | Growth strategy of leading players |
28 | Market share of vendors, 2023 |
29 | Company Profiles |
30 | Unmet needs and opportunity for new suppliers |
31 | Conclusion |
32 | Appendix |