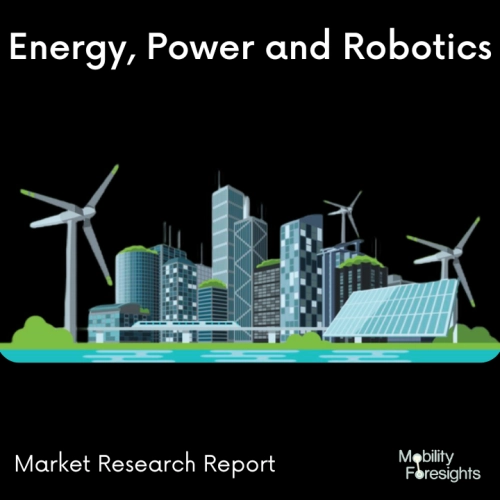
- Get in Touch with Us
Last Updated: Apr 25, 2025 | Study Period: 2023-2030
Applications in medicine and research that use dry electrodes include electroencephalography (EEG), electrocardiography (ECG), and electromyography (EMG).
Because they don't need any gel or liquid to transmit electrical signals from the body to the measurement equipment, they are referred to as "dry electrodes."The following elements are frequently found in dry electrode manufacturing equipment:
Substrate: The substrate material gives the electrode a stable foundation by covering it with a thin layer of metal or polymer. Copper, gold, silver, and polyester are typical materials.
Application of the conductive material to the substrate enables the transmission of electrical signals. Carbon, silver, and gold are typical materials.Adhesive substance: The electrode is attached to the skin or scalp using the adhesive substance.
It must not be harmful to the skin or irritate it conducting material and the substrate are cut into the required form and size using die-cutting machinery.
This apparatus might make use of a mechanical or laser cutting instrument.Equipment for packaging: After being created, dry electrodes need to be packed for distribution.
To guarantee that the electrodes remain sterile until they are used, this may entail heat sealing, vacuum sealing, or other techniques.In order to make sure that the electrodes satisfy the required requirements, quality control equipment is needed.
Dry electrode manufacturing equipment accounted for $XX Billion in 2022 and is anticipated to reach $XX Billion by 2030, registering a CAGR of XX% from 2023 to 2030.
To create and market cutting-edge dry electrode manufacturing technologies for the battery cell industry, BWP, LiCAP, and Siemens have joined forces.
Capital equipment maker BW Papersystems (BWP), a branch of Barry-Wehmiller, serves a variety of sectors. LiCAP Technologies, Inc. (LiCAP) is a producer of dry electrodes for solid-state batteries and lithium-ion batteries that are both affordable and environmentally friendly.
Siemens is a leading innovator in the world, specialising in automation, electrification, and digitalization for the manufacturing and process sectors.
Increasing battery demand is accompanied by a sharp increase in demand for machinery used to make battery cells.
The majority of the current providers of battery cells are headquartered in Asia and are already working at more than 95% capacity. Also, they might give established clients' orders priority over those from new market entrants from the US and Europe.
As a result, EV OEMs and battery cell manufacturers in North America and Europe may experience a bottleneck in the supply of equipment, jeopardising their anticipated start of production.
Sl no | Topic |
1 | Market Segmentation |
2 | Scope of the report |
3 | Abbreviations |
4 | Research Methodology |
5 | Executive Summary |
6 | Introduction |
7 | Insights from Industry stakeholders |
8 | Cost breakdown of Product by sub-components and average profit margin |
9 | Disruptive innovation in the Industry |
10 | Technology trends in the Industry |
11 | Consumer trends in the industry |
12 | Recent Production Milestones |
13 | Component Manufacturing in US, EU and China |
14 | COVID-19 impact on overall market |
15 | COVID-19 impact on Production of components |
16 | COVID-19 impact on Point of sale |
17 | Market Segmentation, Dynamics and Forecast by Geography, 2023-2030 |
18 | Market Segmentation, Dynamics and Forecast by Product Type, 2023-2030 |
19 | Market Segmentation, Dynamics and Forecast by Application, 2023-2030 |
20 | Market Segmentation, Dynamics and Forecast by End use, 2023-2030 |
21 | Product installation rate by OEM, 2023 |
22 | Incline/Decline in Average B-2-B selling price in past 5 years |
23 | Competition from substitute products |
24 | Gross margin and average profitability of suppliers |
25 | New product development in past 12 months |
26 | M&A in past 12 months |
27 | Growth strategy of leading players |
28 | Market share of vendors, 2023 |
29 | Company Profiles |
30 | Unmet needs and opportunity for new suppliers |
31 | Conclusion |
32 | Appendix |