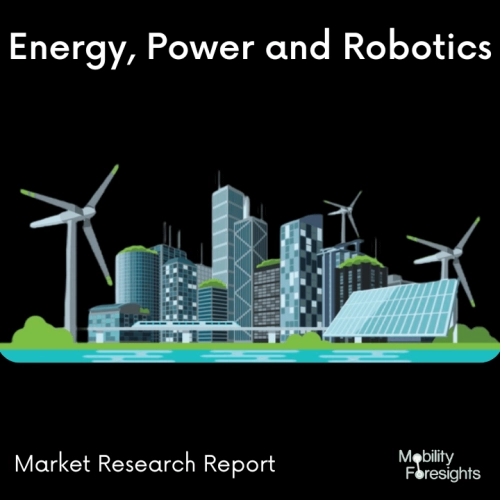
- Get in Touch with Us
Last Updated: Apr 25, 2025 | Study Period: 2024-2030
By subjecting the material to a bombardment of ionsâtypically a plasma of reactive gases such as fluorocarbons, oxygen, chlorine, and boron trichlorideâthat dislodge portions of the material from the exposed surface, dry etching refers to the removal of material, typically a masked pattern of semiconductor material.
Nitrogen, argon, helium, and other gases are occasionally added. Reactive-ion etching is a typical form of dry etching. The dry etching method often etches directionally or anisotropically, in contrast to many (but not all) of the wet chemical etchants used in wet etching.
In order to create material recesses, dry etching is utilised in concert with photolithographic processes to target specific regions of a semiconductor surface.
The Global dry etch system market accounted for $XX Billion in 2023 and is anticipated to reach $XX Billion by 2030, registering a CAGR of XX% from 2024 to 2030.
In order to give chipmakers the improved functionality and extendibility necessary for future innovation, Lam Research Corp. announced the introduction of a newly redesigned dry plasma etch technology and system solution.
The revolutionary Sense.iTM platform from Lam provides unmatched system intelligence in a small, high-density architecture to enable process performance at the greatest productivity and support logic and memory device roadmaps for the ensuing decade.
The Sense.i platform, whose foundational technology was developed from Lam's market-leading Kiyo and Flex process modules, provides the essential etch capabilities needed to keep developing uniformity and etch profile control for increasing yield and reducing wafer costs.
The Sense.i platform is made to accommodate changes in technology as screen sizes go smaller and aspect ratios get higher.
Sl no | Topic |
1 | Market Segmentation |
2 | Scope of the report |
3 | Abbreviations |
4 | Research Methodology |
5 | Executive Summary |
6 | Introduction |
7 | Insights from Industry stakeholders |
8 | Cost breakdown of Product by sub-components and average profit margin |
9 | Disruptive innovation in the Industry |
10 | Technology trends in the Industry |
11 | Consumer trends in the industry |
12 | Recent Production Milestones |
13 | Component Manufacturing in US, EU and China |
14 | COVID-19 impact on overall market |
15 | COVID-19 impact on Production of components |
16 | COVID-19 impact on Point of sale |
17 | Market Segmentation, Dynamics and Forecast by Geography, 2024-2030 |
18 | Market Segmentation, Dynamics and Forecast by Product Type, 2024-2030 |
19 | Market Segmentation, Dynamics and Forecast by Application, 2024-2030 |
20 | Market Segmentation, Dynamics and Forecast by End use, 2024-2030 |
21 | Product installation rate by OEM, 2023 |
22 | Incline/Decline in Average B-2-B selling price in past 5 years |
23 | Competition from substitute products |
24 | Gross margin and average profitability of suppliers |
25 | New product development in past 12 months |
26 | M&A in past 12 months |
27 | Growth strategy of leading players |
28 | Market share of vendors, 2023 |
29 | Company Profiles |
30 | Unmet needs and opportunity for new suppliers |
31 | Conclusion |
32 | Appendix |